We keep talking about workflow automation for manufacturing and distribution enterprises in our blogs, and how vital its role is in improving the speed of doing business, operational efficiency cost control, and achieving paperless operations.
But how do we see workflow automation happening in real-time? What are its real-life examples?
In most small & medium enterprises, workflows solely depend on paper documents, spreadsheets, calls and emails. We often get to hear,
“I have sent you an email, please read it urgently.”
“I haven’t got an approval from your end. Please review and approve immediately.”
“I have misplaced the spreadsheet, Could you please send it again.”
“The order file is missing. We will have to find it.”
These phrases indicate bottlenecks and operational hurdles In the age of today’s modern software and systems. Manual methods often create a lot of confusion, chaos, frustration, and mistrust amongst employees, managers, and departments. There are no concrete methods or processes and the enterprise functions with sheer luck till the tipping point.
Successful enterprises function with centralized, core processes with the help of a robust workflow management system within ERP software.
What is Workflow Management?
Workflow management involves a sequence of tasks and actions leading to data generation. In manufacturing, they determine how raw materials go from procurement to the final product that is delivered to the customer in the most efficient and cost-controlled manner. The data generated is used to trigger the next operational steps or workflows till the sequence of tasks is complete.
Workflow management eliminates redundant tasks and bottlenecks that hinder the smooth flow of enterprise operations. It helps identify areas for improvement and helps enterprises inch towards their short-term and long-term goals.
Key features
Steps
Steps are simply predefined tasks within the workflow depending on the type of industry and respective operations. Each step leads to a concrete conclusion that triggers the next step till the objective is achieved. Workflow steps can be manual or automated.
Key Stakeholders
The key stakeholders are personnel who are responsible to execute or oversee the execution of workflow steps and achieve key objectives. They can be anyone from the top floor to the shop floor depending on the kind of work and objective to be achieved. They can be assigned to each step, a sequence of steps, or the entire workflow.
Conditions
Conditions are rules and exceptions that determine the next steps after the existing step is completed. These can be easily set up and configured within the ERP software depending on the workflow requirements.
How does Workflow Management function within an ERP software?
Today, modern ERP software offers workflow management for manufacturing, inventory, CRM, accounting, quality, project management, sales and purchases, planning etc. Based on individual requirements, these workflows can be customized and included in the ERP.
Below is a typical workflow for the manufacturing process within OmegaCube ERP.
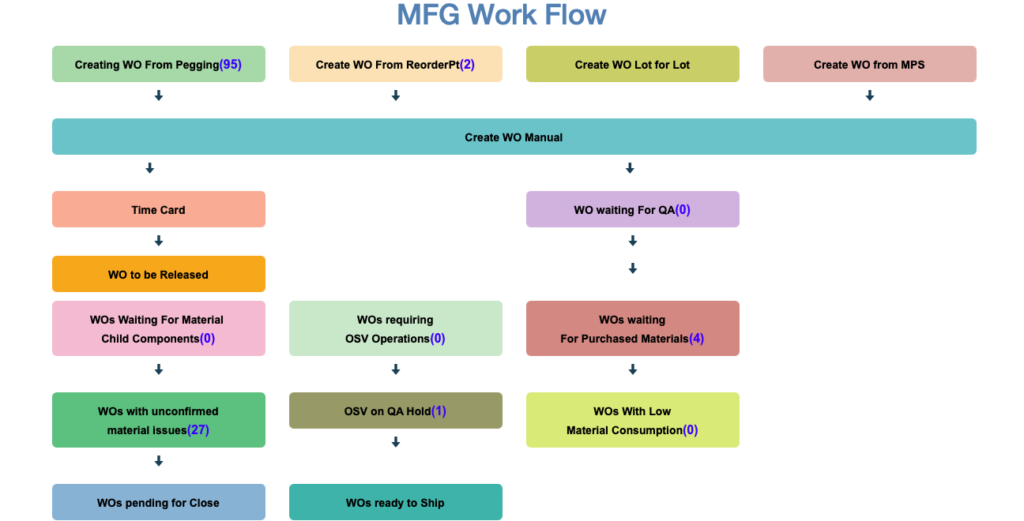
The workflow dashboard focuses on how to create and track work orders from various phases of manufacturing. Each task or action item also carries a real-time number of work orders that were created and pending further action.
With this workflow, personnel gets a real-time view of work orders that are created and are in the various stages of operational progress. With a single click, they know the details of work orders that are,
- Waiting for purchased materials
- Waiting for child components
- Waiting to be released to manufacturing
- Waiting for QA
- Require OSV operations
- With unconfirmed material issues
- With low material consumption
- Pending closure
- Ready to ship etc.
Personnel can easily track work order progress and initiate corrective measures for pending work orders.
Similarly, the project specific workflow provides clear action items to execute and manage project related tasks.
Personnel can easily create quotes, purchase orders, project tasks & budgets, work orders, project BOMs etc. They can track pending quotations, shipments, and project time. They can review project documents and initiate the next steps.
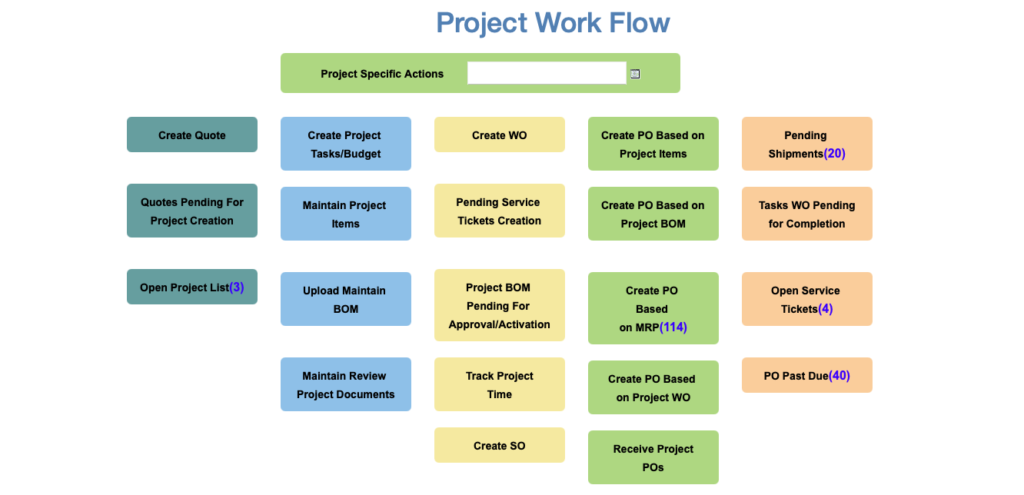
Hallmark of a successful Workflow Management System
In manufacturing and distribution operations, there are countless workflows and they differ with each industry type and segment. For a successful workflow management system, enterprises need to follow the basic three steps.
Workflow Clarity
Before implementing an ERP or Workflow Management System (WMS), enterprises need to identify existing workflows (both manual and automated) that are currently operational. Even the ones that are deemed small or the ones that differ from employee to employee. They have to then identify important workflows that need to be automated, the ones that can be merged, and the ones that can be eliminated. The ones that cannot be automated can be documented for future reference.
Workflow Prioritization
Workflows that have the ability to impact day to day operations and overall business should be prioritized over the rest. They need to be as clear as possible within the system. Some examples of top-level workflows are sales management, inventory and procurement, production scheduling, accounting etc. Once these workflows are documented and configured, they can proceed to the next level of workflows that are linked to the primary ones.
Continuous Monitoring & Optimization
Some workflows are automated while some are not. However, both workflow types need to be monitored continuously, their outcomes need to be tracked and clearly document the scope of improvement. The manual workflows depend on personnel’s decision making abilities and efficiency in their day to day operations. Therefore, proper training will help them to function efficiently alongside automated workflows.
Get in touch with us to know more about the Workflow Management System within OmegaCube ERP. Contact us for an in-depth demo.