- OmegaCube Technologies
- Solutions
- By Manufacturing Problem
- I am unable to schedule my production properly leading to delay in customer delivery, loss of margins and profitability
This problem arises as a direct result of not having enough visibility on the movement of materials from suppliers and to the shop floor, allocation of manpower and improper upkeep and maintenance of machines.
When you do not know if there are enough materials in stock or your machines breakdown frequently or there is a crunch in manpower availability, you cannot schedule your jobs accurately, leading to delay in materials arriving at the shop floor, delay in manufacturing and on-time delivery to customers.
These delays eat up your margins, profitability and dents your market reputation.
Current Production Problems that you Face
- Scheduling is manually done using spreadsheets, sticky notes and writing board.
- Customer orders are taken based on assumption that materials, manpower and machines are available at a given point of time.
- Job prioritization is a mess as they are executed randomly and not because of their due dates.
- Every job on the shop floor becomes an emergency job due to lack of visibility.
- Material procurement from suppliers and shipping times are not considered while scheduling jobs.
- Product quality takes a hit as jobs are manufactured and shipped quickly.
- Overhead costs increase, margins decrease due to delay in production.
- Customers are unhappy due to late deliveries consistently.
Become the Master Planner that your Manufacturing Enterprise needs with OmegaCube ERP
- Improved on-time delivery to customers with automated production schedules.
- Streamlined supply chain collaboration and planning based on demand & availability.
- Accurate capacity planning based on resource availability and real-time data.
- Improved shop floor productivity through activity auto-alerts to personnel.
- Improved customer satisfaction with order and shipment tracking via self-service portal.
- Manage expedited job schedules with auto simulation of jobs.
- Accurate schedules & customer due dates based on factual real-time data.
It’s time to stop asking the question, “How to schedule production and deliver goods on time?”
Get Manufacturing under your control with the help of OmegaCube ERP’s other advanced enterprise modules
Our Customers are Our Purpose and Our Strength

We would cross our fingers and hope for the best. Now we have a realistic assessment of whether the job can be done on time. OmegaCube allows us to update our individual work center schedules every 90 seconds, ensuring that our employees are always working on the most critical demand schedules at any given point during the day.”

OmegaCube ERP enabled us to get real-time visibility of our production schedules and inventory levels. Everyone on the shop floor knows the number of pending orders, how much inventory is ordered, how much is consumed and how much is needed to go out in the coming days. They now have the entire reporting history of how much inventory was consumed in the last 30/60/90 days, allowing them to analyze and manage inventory procurements better.”

We have improved our scheduling efficiency by releasing a job to the fabricator within 3-4 weeks after the engineering team has released the job for purchasing as compared to 6-9 weeks, prior to OmegaCube ERP. We are continuing to work on improving our scheduling efficiency, striving to release stock equipment within 3-4 days.”
Browse through our Latest ERP and Technological Insights
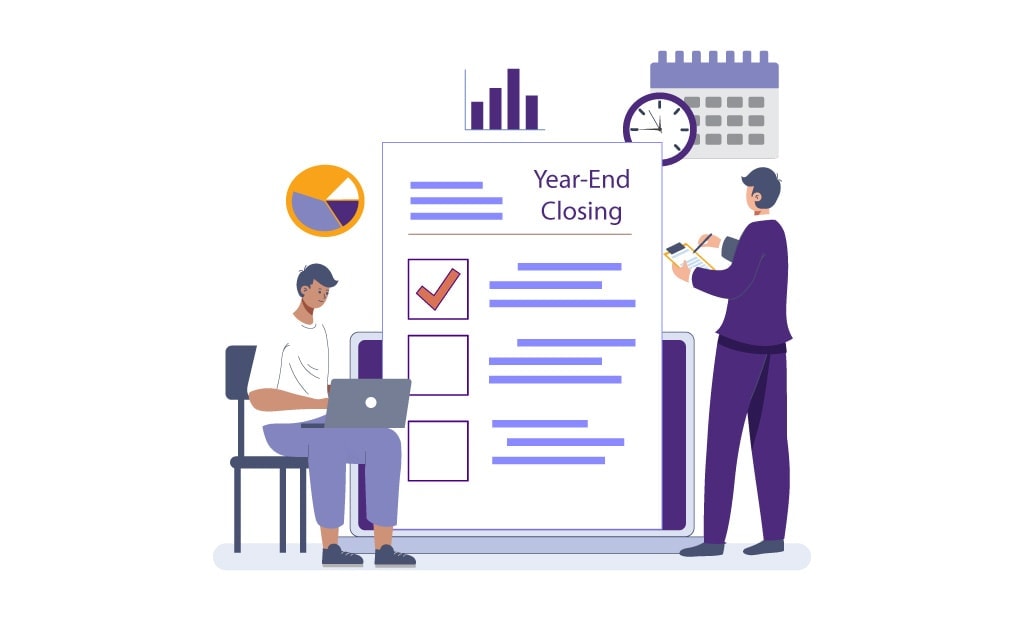
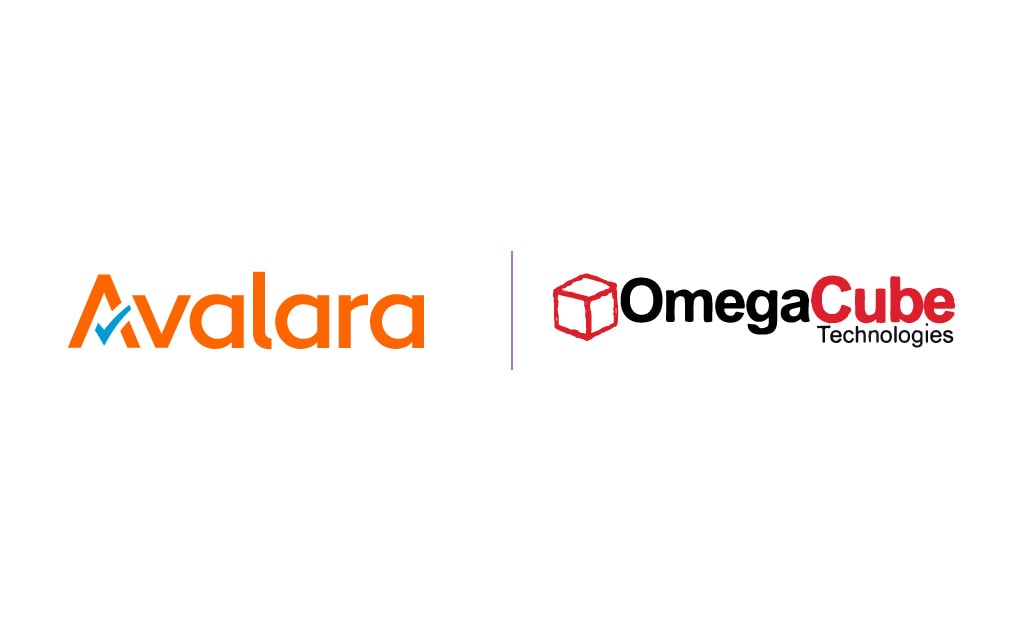
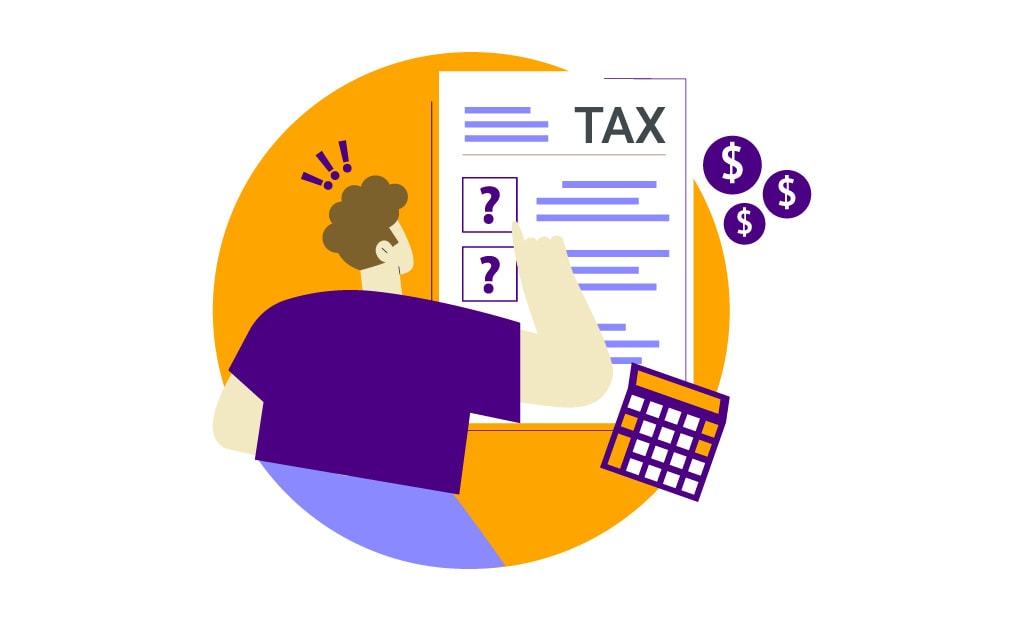
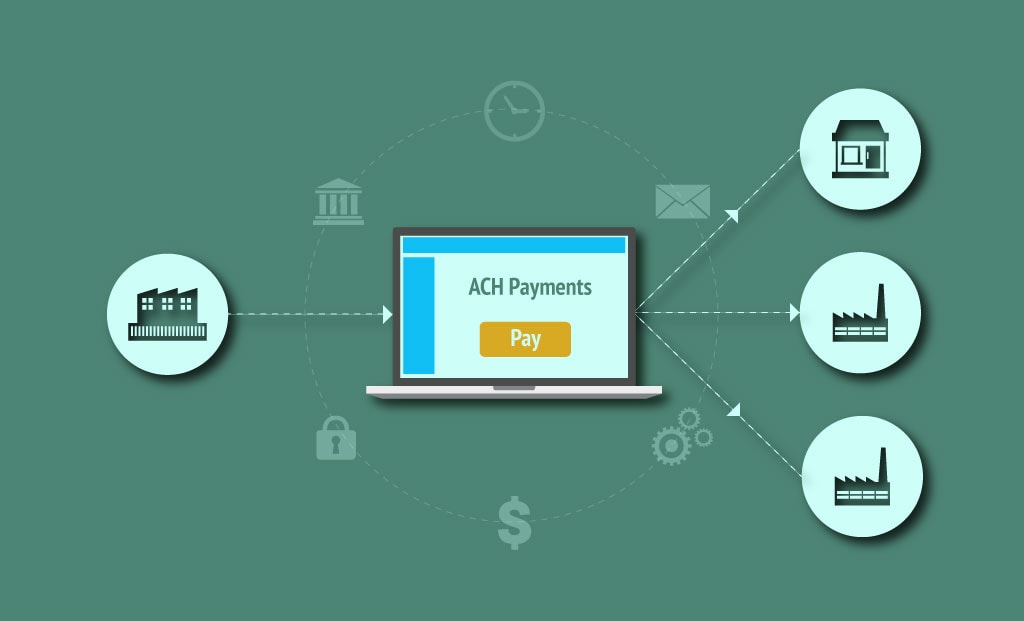
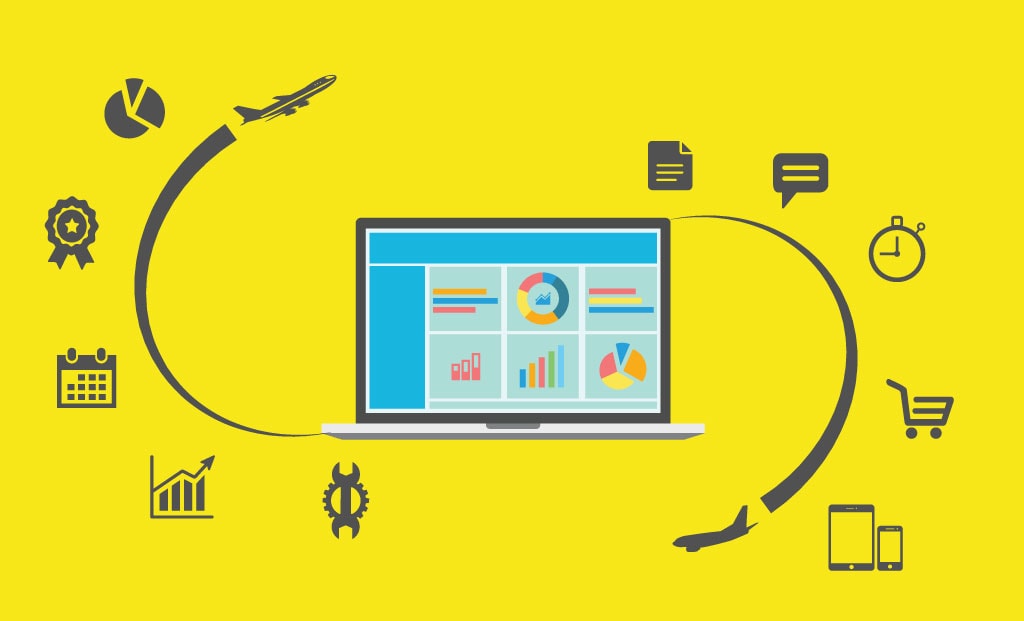
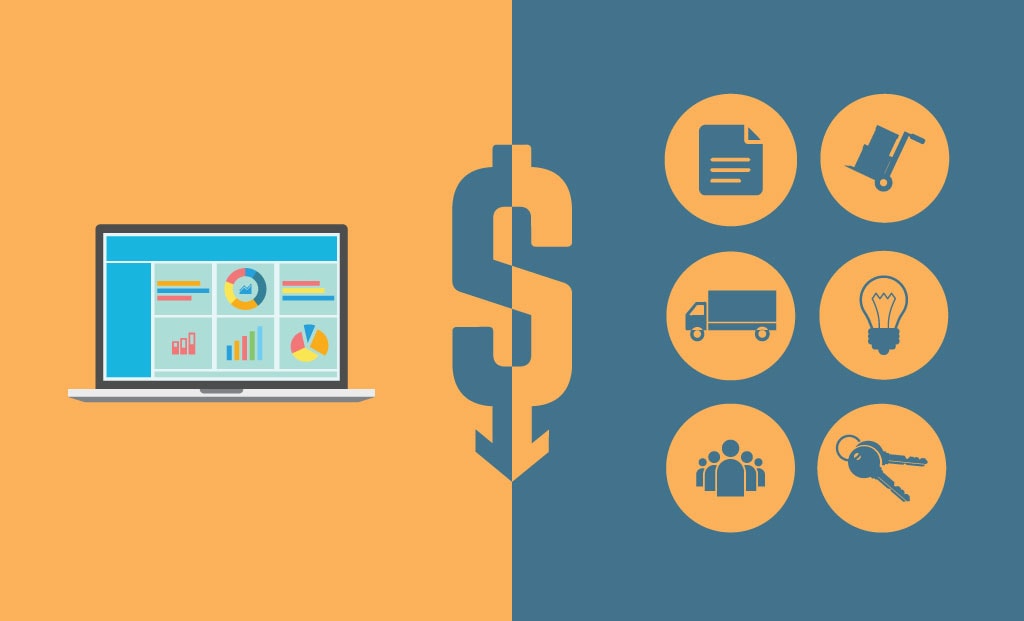