- OmegaCube Technologies
- Solutions
- By Manufacturing Problem
- By Manufacturing Problem No Real Time Shop Floor Updates
Machines fail regularly, work orders are hard to track, tools and parts are hard to find and machine maintenance is erratic. The main cause of these issues are limited visibility of what’s happening on the shop floor and the lack of communication between machines and personnel.
In a conventional shop floor setup, machines operate individually and are not connected to a particular monitoring system.
Due to this, the shop floor worker has to constantly, manually keep tabs on machine performance, availability and ensure that work order allocation happens evenly across all the machines. This is easier said than done, as there are multiple orders to attend to simultaneously and multiple machines to monitor. In the rush of completing customer orders, machines are over-worked leading to their breakdown and production disruption.
Current Shop Floor Problems that you Face
- Work Orders are manually created on paper and passed from one phase to another or on spreadsheets and updated later.
- Machines break down abruptly leading to chaos on the shop floor and delaying production.
- There is no track of what is the inventory available to carry out production, how much material is consumed during production and how much rework is required.
- Machines lie idle without the shop floor personnel knowing about it.
- Multiple orders get piled up without the means to prioritize and allocate them to machines and personnel.
- Machine maintenance is poorly managed leading to frequent machine breakdowns.
- Cannot determine Overall Equipment Effectiveness (OEE) for the machines and equipment.
- Overhead costs increase with labor overtime costs, machine repair, delayed production, customer dissatisfaction etc.
Make Shop Floor, the HERO of your Manufacturing Operations with OmegaCube ERP
- Automated Work Order management with WO creation, job prioritization, allocation and shop floor dispatch.
- Real time shop floor operation status visible to personnel at all times.
- Auto update of work orders post completion of each manufacturing stage.
- Improved mobility for shop personnel with job status entry from handheld devices and machine consoles.
- Real-time shop floor information on quantity of materials consumed, inventory available, scrap quantity, job rework etc.
- Efficient inventory movement tracking with the help of third-party tracking applications.
- Create and maintain overall information on machine repair, spare parts, bill of materials, preventive maintenance, repair schedules, procedures, instruction manuals etc.
It’s time to stop asking the question,
“How to know what is happening on my shop floor in real-time?.”
Get Manufacturing under your control with the help of OmegaCube ERP’s other advanced enterprise modules
Our Customers are Our Purpose and Our Strength

I sit down every morning and look at a report which tells me how much I owe, how much I have coming in and helps me plan for incoming orders. It’s become an integral part of running my business effectively, efficiently and profitably, and we could add six more businesses without having to change our software.”

OmegaCube ERP enabled us to get real-time visibility of our production schedules and inventory levels. Everyone on the shop floor knew the number of pending orders, how much inventory was ordered, how much was consumed and how much was needed to go out in the coming days. They now have the entire reporting history of how much inventory was consumed in the last 30/60/90 days, allowing them to analyze and manage inventory procurements better. “

This was March 2020 and then COVID-19 hit. If we were still using the old FoxPro system and the manual way of operating, I don’t think we could have had everybody go home and work remotely.
With OmegaCube ERP, we were able to work remotely and still operate during the pandemic. Even though we just completed setting up our initial ERP system, our employees were able to run with it while working remotely and that ended up working out great. The system operated efficiently for sales, engineering, and purchasing.
I don’t think we could have done that with the old FoxPro system as we did with OmegaCube ERP. So the timing of implementing OmegaCube ERP was perfect.
Browse through our Latest ERP and Technological Insights
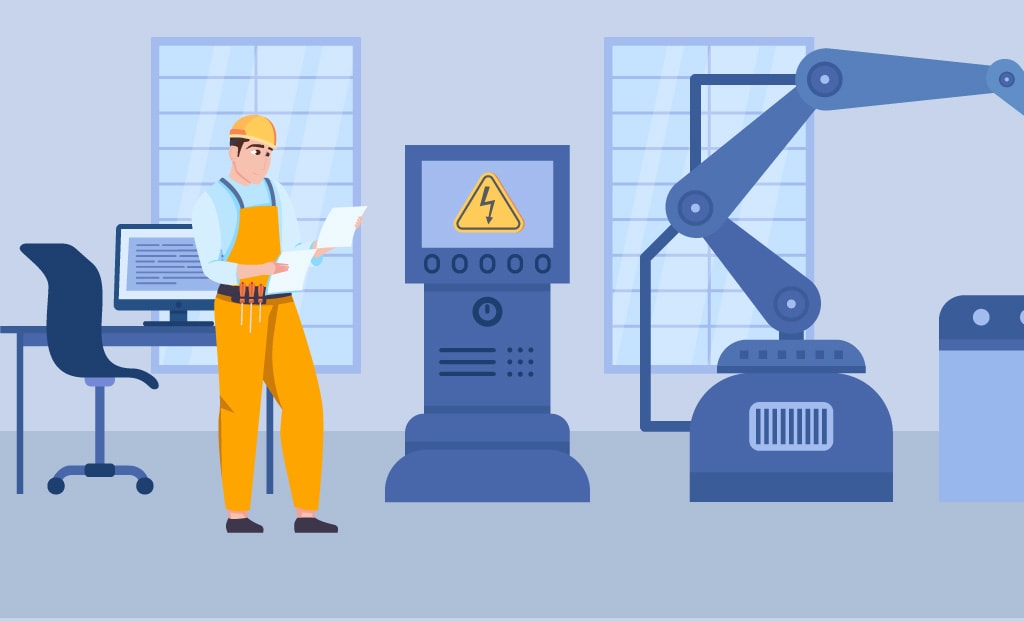
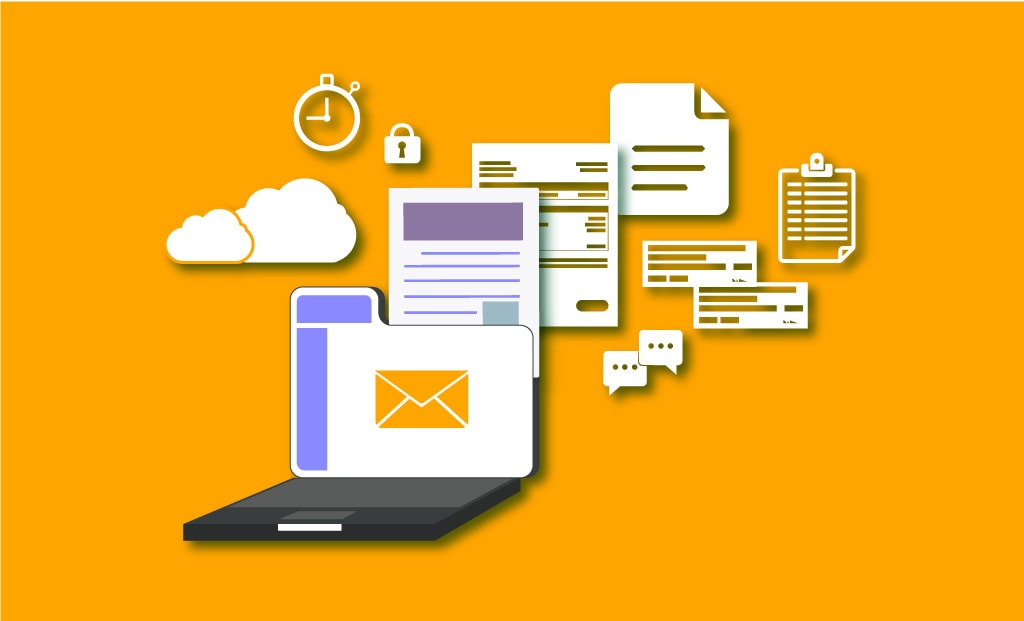
How can you Automate Document Distribution to Improve Enterprise Efficiency and Productivity?
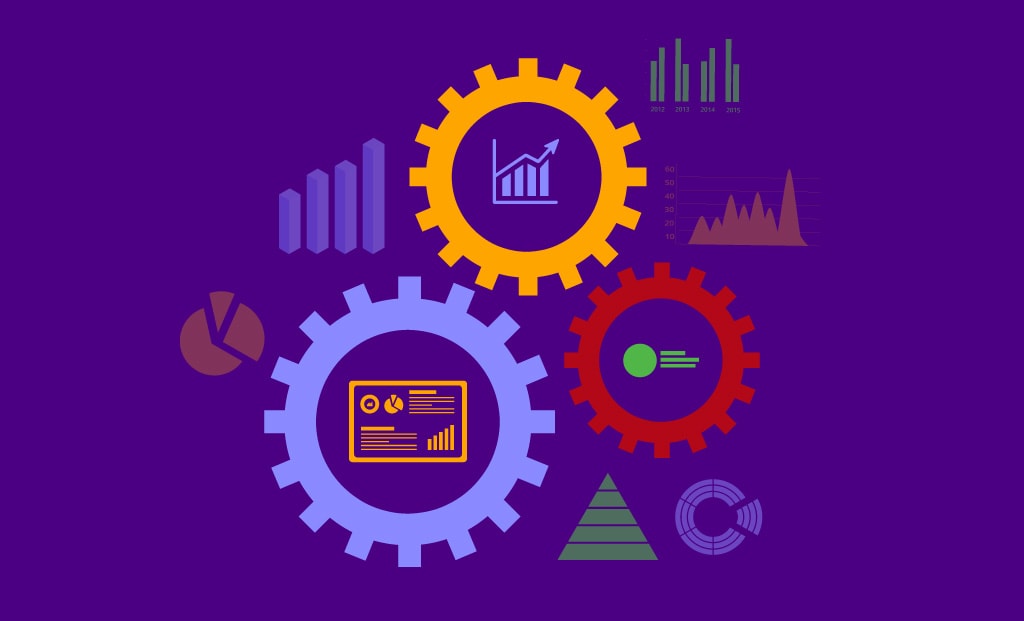
How Advanced Analytics and Business Intelligence Dashboards boost Enterprise’s Efficiency?
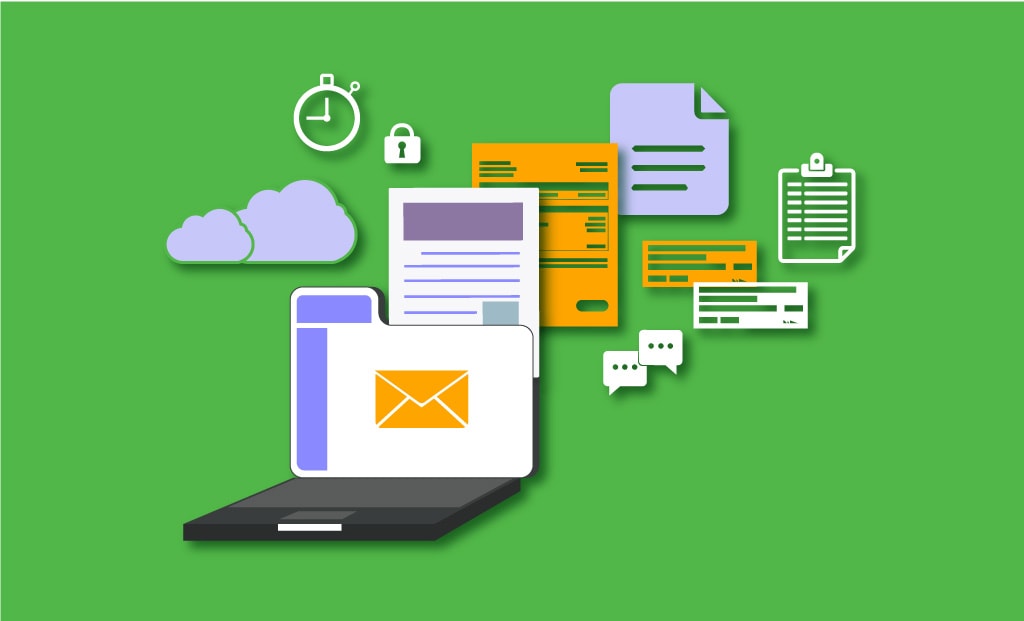
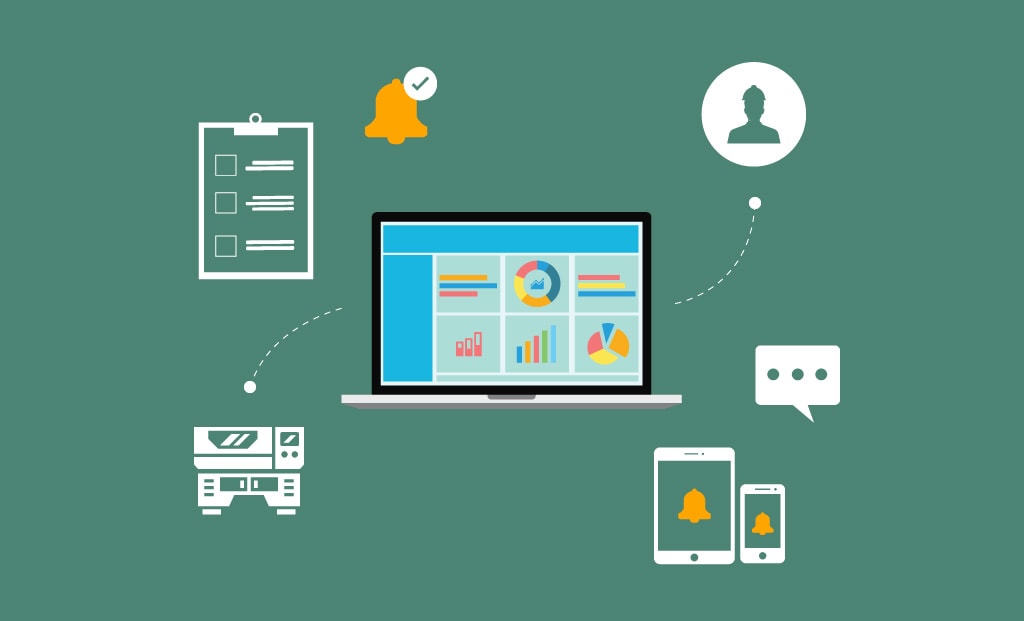
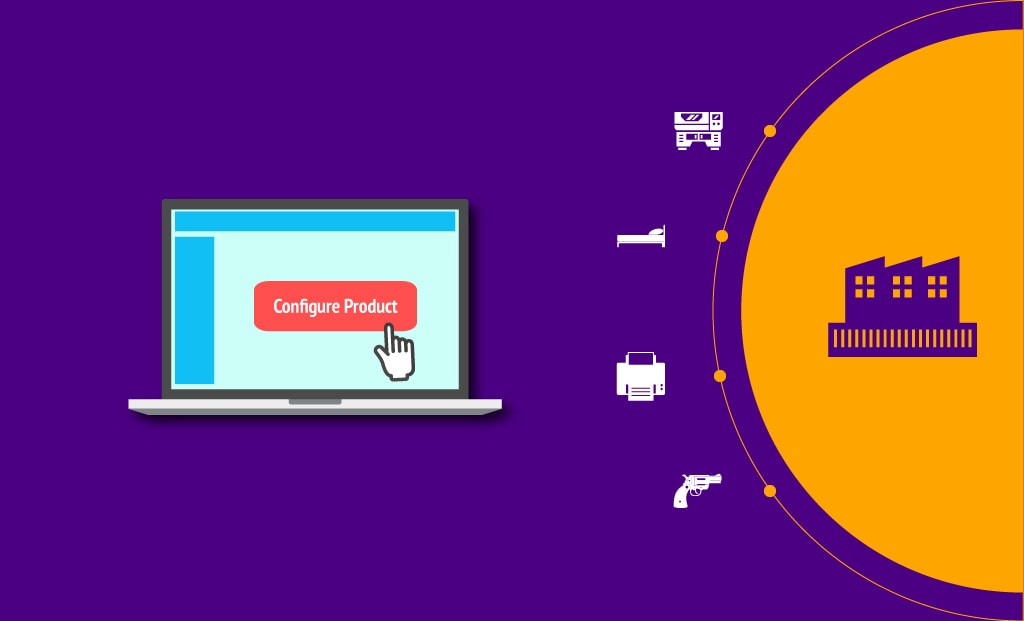