In our previous blog, we explained how an ERP automates critical manufacturing workflows such as Sales, Purchase, Inventory, Production Scheduling, and Supply Chain Management. Most of these workflows handle prospect and client-related processes and form a part of front-office operations.
While front-office operations keep your customers happy by delivering their orders at the earliest, there is another set of people who ensure the front-office is able to do that, and they are the back-office team. This team does not interact directly with the customers, but plays a vital role in managing key manufacturing departments such as Order Fulfillment, Human Resources, Payroll, Accounting & Finance, Scheduling, IT, Security etc. These are primary internal functions of an organization and a manufacturer needs to pay close attention in streamlining these activities if they want to speed up production, achieve profitability and business growth.
The Back Office usually determines,
- How much profitability was achieved in the previous financial year?
- How many raw materials were consumed for ‘x’ number of orders?
- How many orders are WIP, completed?
- When should a particular job be planned in order to deliver the end-product to the Customer on time?
- When to procure fresh inventory from which supplier in a cost & time-effective manner?
Much more.
Apart from these, they are the bridge between the Customer and the Front Office providing vital manufacturing information proactively and on-demand. This ensures the manufacturing unit is always on top of their operations and averts any possible crisis.
Most manufacturers specially in Small & Medium segment rely on manual methods/legacy systems to manage operations in each department (HR, Accounting, Payroll, Warehouse, Inventory etc.). This includes maintaining data on spreadsheets and even worse, books and registers. These systems are primarily used for the purpose of tracking work in each individual departments and not with an intention to interact with each other. This leads to a disconnected work environment between departments and considerably slows down information-flow leading to increased manufacturing lead times, delayed response, product delivery and in the end, a frustrated customer.
How does an ERP handle Front & Back Office integration?
Today’s ERP software carries the capability of integrated workflow management and can be easily integrated with third-party modules/software and customization. Data Consistency is a key factor and an ERP helps achieve this without any added effort thereby assisting manufacturers to run their operations efficiently.
Let us take a scenario to understand how an ERP makes both front and back offices work like clockwork with the help of an infographic.
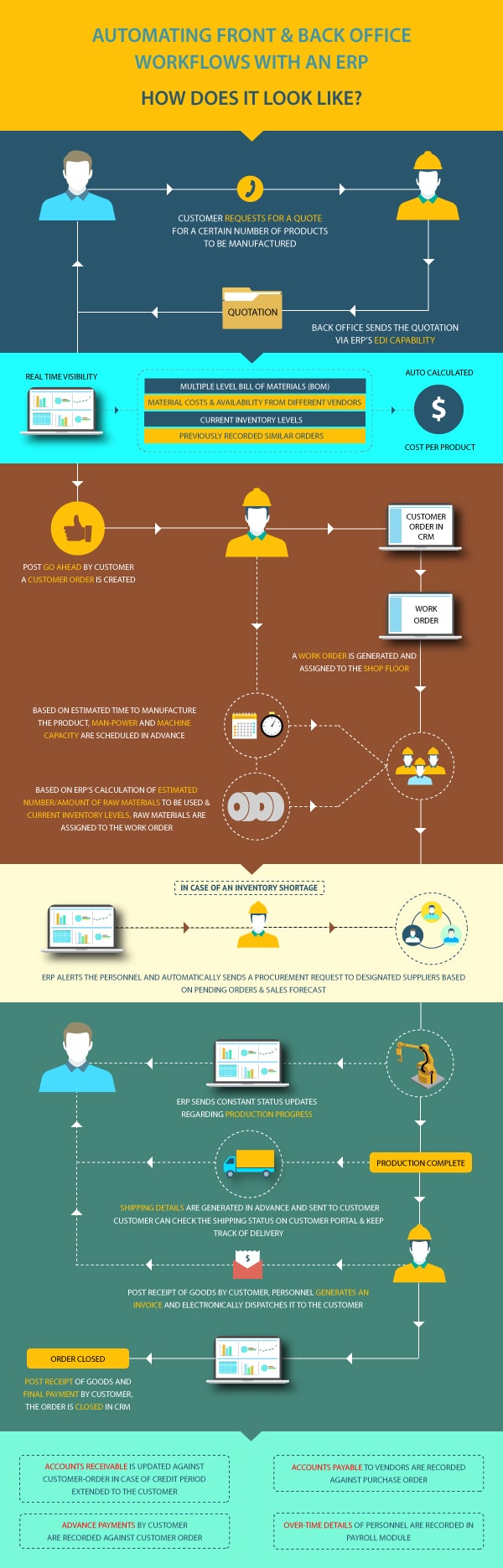