Material Requirement Planning (MRP)
Key Benefits
- Meet stringent delivery deadlines, dynamic customer demands and market fluctuations through effective Material Requirement Planning (MRP)
- Anticipate material requirements and trigger auto purchase through effective Material Requirement Planning (MRP) & Scheduling.
- Quick ordering of material and outside services necessary for the job or project
- Identify sources of demand and trigger purchasing with one-click
- Ensure adequate raw materials required to initiate production and fulfil the orders.
- Eliminate over-stock by constantly monitoring inventory levels and thereby reducing procurement and storage costs.
- Schedule production based on material availability, thereby reducing production disruption, material wastage, job delays etc.
- Anticipate requirements well in advance based on demand and purchase trends, and reduce inventory overstock.
Key MRP Features
- Evaluate BOM requirements at all levels.
- Flexibly define vendor lead time in BOM level or in items.
- Compute lead time calculation of due dates based on demand size and process times.
- Get automatic guidance on purchases to delay and/or expedite.
- Get automatic pegging of supply when demand due dates change.
- Override system computed pegging data with user defined hard pegging window.
- Incorporate outside process lead time into calculation.
- Integrated EDI functionality to compute and generate net requirements change.
- Consider revision numbers in MRP calculations.
- System generated actions to create requisitions, PO or RFQs to suppliers.
- Lot size taken into consideration for supply triggers.
- Generate releases to blankets from MRP trigger.
- Trigger creation of sub-assembly work orders.
- Trigger creation of picking and shipping transaction.
- Automatic exception generation for excess supply in make-to-order environments.
- Automatically generated alerts and exceptions allow users to take actions to create, delay, expedite, or cancel supply based on fluctuating demand.
- Predicts delay in schedule due to delays in purchasing.
- Generates exceptions for delays due to outside services purchase.
- Arrive at material requirements using MRP output and in conjunction with purchase module.
- Add or create existing purchase orders from MRP.
- Consolidate multiple purchases into a single PO per supplier and reduce tons of paperwork.
- Create and release blanket POs to suppliers from MRP.
- Evaluate BOM requirements at all levels.
- Flexibly define vendor lead time in BOM level or in items.
- Compute lead time calculation of due dates based on demand size and process times.
- Get automatic guidance on purchases to delay and/or expedite.
- Get automatic pegging of supply when demand due dates change.
- Override system computed pegging data with user defined hard pegging window.
- Incorporate outside process lead time into calculation.
- Integrated EDI functionality to compute and generate net requirements change.
- Consider revision numbers in MRP calculations.
- System generated actions to create requisitions, PO or RFQs to suppliers.
- Lot size taken into consideration for supply triggers.
- Generate releases to blankets from MRP trigger.
- Trigger creation of sub-assembly work orders.
- Trigger creation of picking and shipping transaction.
- Automatic exception generation for excess supply in make-to-order environments.
- Automatically generated alerts and exceptions allow users to take actions to create, delay, expedite, or cancel supply based on fluctuating demand.
- Predicts delay in schedule due to delays in purchasing.
- Generates exceptions for delays due to outside services purchase.
- Arrive at material requirements using MRP output and in conjunction with purchase module.
- Add or create existing purchase orders from MRP.
- Consolidate multiple purchases into a single PO per supplier and reduce tons of paperwork.
- Create and release blanket POs to suppliers from MRP.
Our Customers are Our Purpose and Our Strength

OmegaCube ERP enabled us to get real-time visibility of our production schedules and inventory levels. Everyone on the shop floor knew the number of pending orders, how much inventory was ordered, how much was consumed and how much was needed to go out in the coming days. We now have the entire reporting history of how much inventory was consumed in the last 30/60/90 days, allowing us to analyze and manage inventory procurements better.”

With our visibility into demand schedules, we know which parts we can pull in to get a more complete nest, get better utilization of material and estimate our costs much more accurately. Similarly, when we have jobs requiring material of like-thickness OmegaCube pools those together into a single work-center, making workflow much more efficient.”

As soon as jobs are completed everyone knows an order is ready to ship. An email is sent via mobile devices so people throughout the facility are notified no matter where they are. When new jobs are created people can immediately check BOMs and inventory levels, so tools and materials can be ordered within minutes.”
Browse through our Latest ERP and Technological Insights
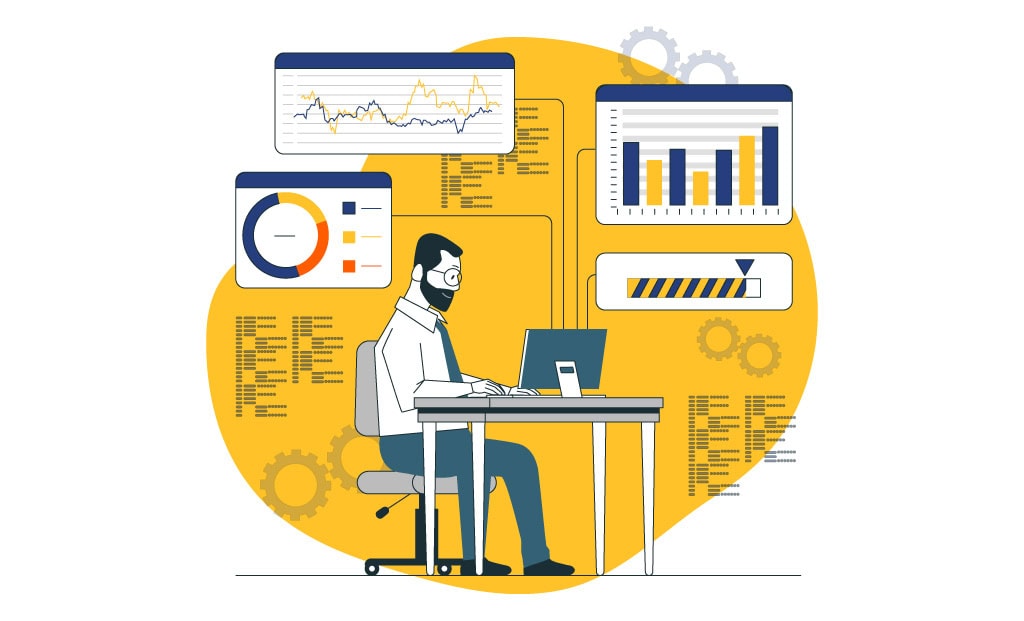
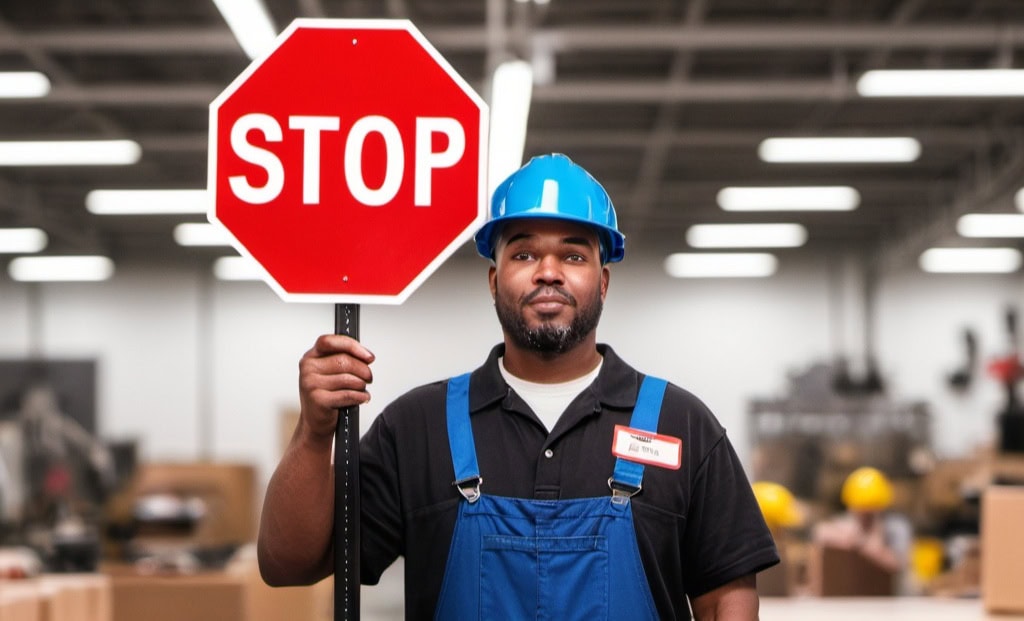
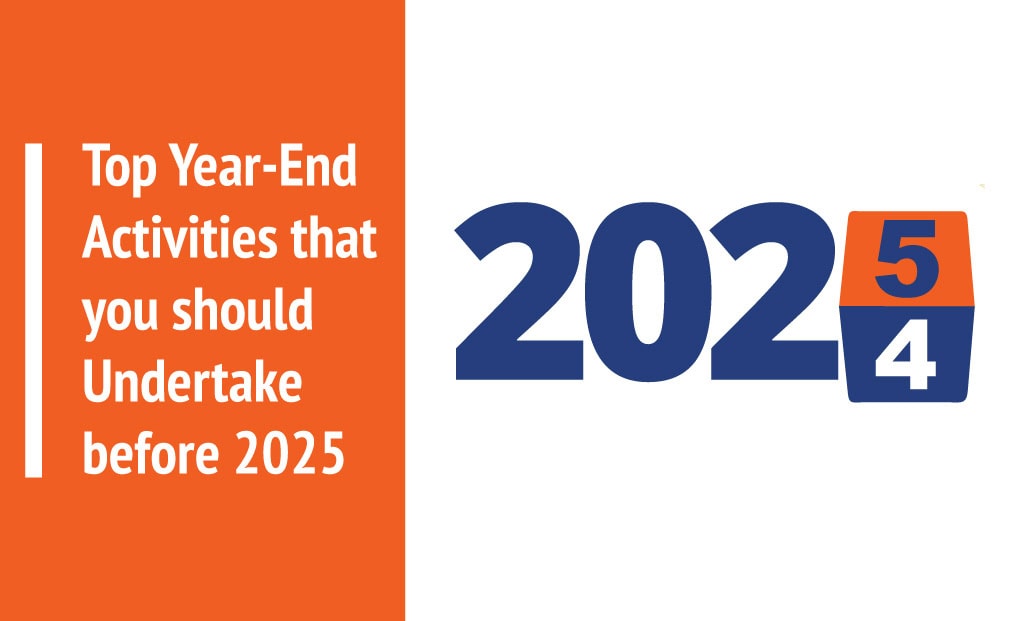
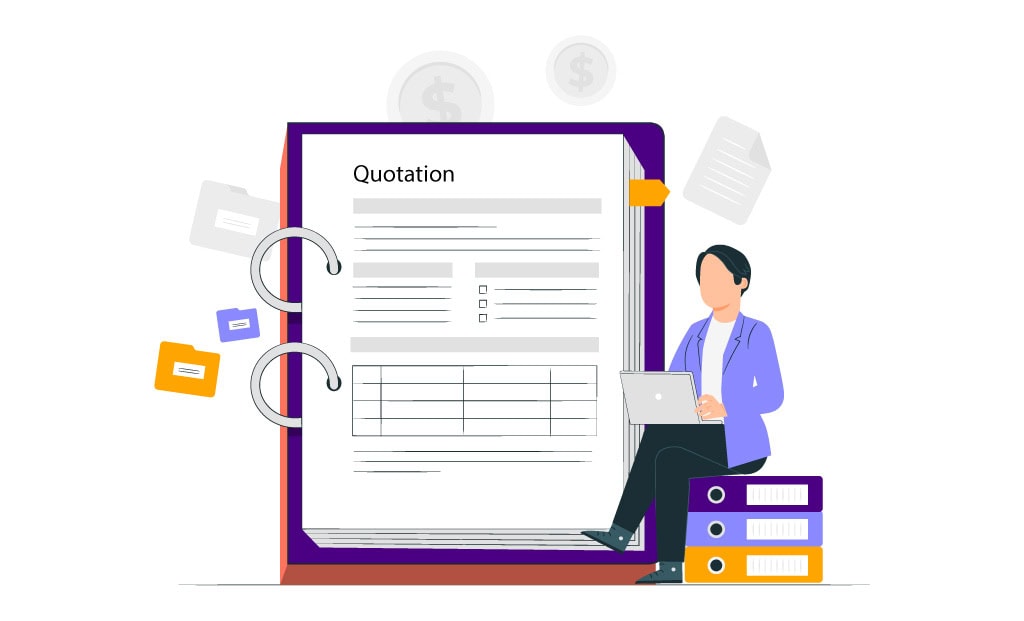
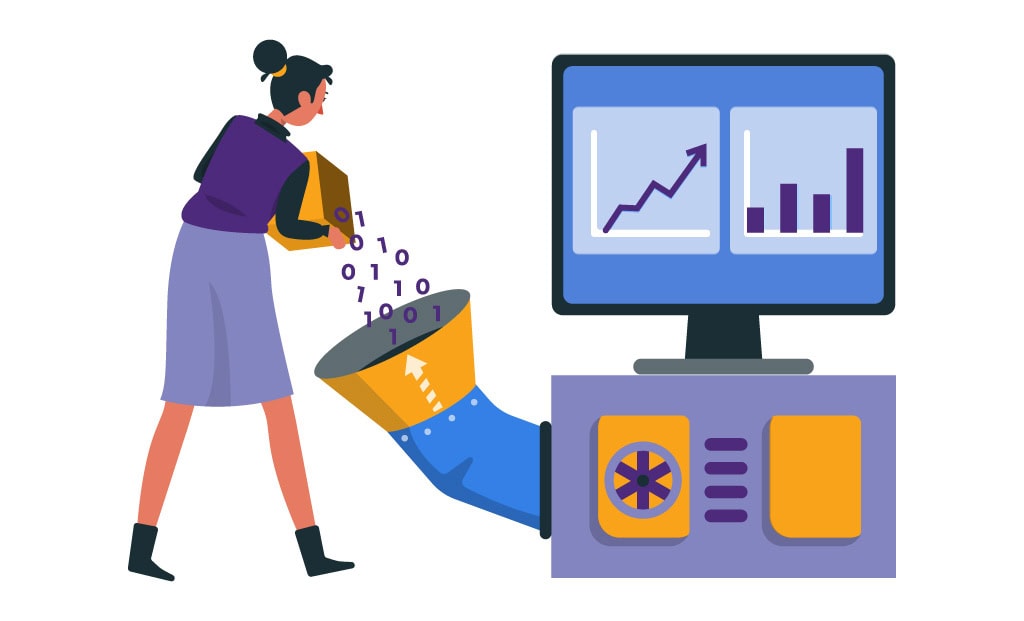
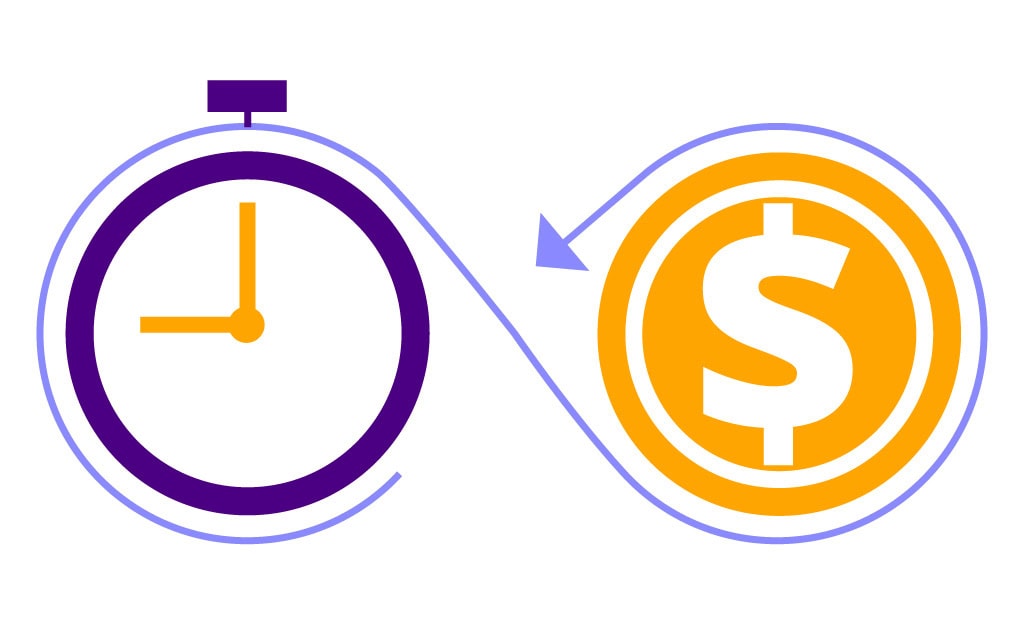
FAQ
Inventory Management in OmegaCube ERP enables manufacturing enterprises to efficiently plan, procure, build, manage and track inventory in real time. They can maintain optimum inventory levels, improve material traceability and cash flows by ordering the right materials at the right time for the right cost from the right supplier.
Suppliers and Purchasing in OmegaCube ERP helps manufacturers to efficiently track and manage the entire flow of raw materials right from its suppliers to the warehouse, to the factory till the final product reaches the customer. It helps improve supplier relationships via continuous goods monitoring, quality control, data-sharing via EDI, and self-service portals for suppliers.
Planning and Scheduling in OmegaCube ERP automates production planning and scheduling workflows by taking material, manpower and machine availability into consideration. It improves capacity utilization during production, operator productivity, optimum supply chain planning, and on-time delivery to customers.