Shop Floor Management
Key Benefits of Shop Floor Management
- Increase efficiency of personnel by relaying production data directly to their hand-held devices & machine consoles.
- Improve mobility by letting personnel to access & record shop floor data with the help of third-party applications & hand-held devices.
- Improve proactive response to breakdowns by monitoring job allocation, machine utilization & performance.
- Improve product quality and compliance standards at each production phase
- Reduce machine and labor idle time and improve utilization
- Improve overall shop floor efficiency, achieve just in time manufacturing by integrating third party applications.
Key Features of Shop Floor Management
- Utilize electronic dispatch list to publish department schedule to shop floor
- Allow each department to view job schedule and priority
- Allow operators to view and print work order related information
- Inform operators about location of upcoming jobs
- Allow operators to clock in directly from the dispatch list
- Alert operators to work orders that are running late
- Allow operators and supervisors to know progress of operations on the work order
- Allow operators to see availability of raw materials for the work order
- Display what work orders are running on the shop floor
- Gain the manufacturing intelligence to improve processes, improve on-time and reduce defects
- Analyze efficiency by departments, employees and work centers
- Analyze employee utilization, indirect labor, manufacturing PPM
- Determine productivity, efficiency using various parameters
- Publish dashboards and manufacturing metrics to various users based on their role
- Access dashboards on mobile devices fro anywhere
- Integrate to nesting software of your choice
- Group work orders based on due dates to send to nesting software
- Import layout information
- Receive and process data automatically from the machine to trigger part completions and update material usage data
- Maintain actual machine time for parts cut by laser or plasma machines
- Specify Lot numbers of material used for part completions
- Utilize a powerful and intuitive interface to collect shop floor data
- Use barcodes, mobile devices or touch screen interface to report work order information
- Allow operators to access part drawings, manufacturing instructions from data collection terminal
- Capture actual time, non-conformance, scrap, setup time, down time from a single terminal
- Print move and completion labels easily
- View work order assignments for an operator
- Collect detailed costs on actual labor time using data collection
- Collect actual material and outside process costs based on purchasing
- Analyze and compare estimated versus actual costs and determine problem areas
- Evaluate margins based on actual costs of a work order
- Determine costs for scrap and rework
- View transactional level detail for all job related costs
- Determine sources of variance for each step in routing, material usage and labor time
- Report non-conformance during in-process inspections directly from data collection terminals
- Record inspection results at every manufacturing step directly in an easy-to-use interface
- Specify user-defined inspection points and attributes
- Collect all relevant data required for quality and defect analysis
- Utilize electronic dispatch list to publish department schedule to shop floor
- Allow each department to view job schedule and priority
- Allow operators to view and print work order related information
- Inform operators about location of upcoming jobs
- Allow operators to clock in directly from the dispatch list
- Alert operators to work orders that are running late
- Allow operators and supervisors to know progress of operations on the work order
- Allow operators to see availability of raw materials for the work order
- Display what work orders are running on the shop floor
- Gain the manufacturing intelligence to improve processes, improve on-time and reduce defects
- Analyze efficiency by departments, employees and work centers
- Analyze employee utilization, indirect labor, manufacturing PPM
- Determine productivity, efficiency using various parameters
- Publish dashboards and manufacturing metrics to various users based on their role
- Access dashboards on mobile devices fro anywhere
- Integrate to nesting software of your choice
- Group work orders based on due dates to send to nesting software
- Import layout information
- Receive and process data automatically from the machine to trigger part completions and update material usage data
- Maintain actual machine time for parts cut by laser or plasma machines
- Specify Lot numbers of material used for part completions
- Utilize a powerful and intuitive interface to collect shop floor data
- Use barcodes, mobile devices or touch screen interface to report work order information
- Allow operators to access part drawings, manufacturing instructions from data collection terminal
- Capture actual time, non-conformance, scrap, setup time, down time from a single terminal
- Print move and completion labels easily
- View work order assignments for an operator
- Collect detailed costs on actual labor time using data collection
- Collect actual material and outside process costs based on purchasing
- Analyze and compare estimated versus actual costs and determine problem areas
- Evaluate margins based on actual costs of a work order
- Determine costs for scrap and rework
- View transactional level detail for all job related costs
- Determine sources of variance for each step in routing, material usage and labor time
- Report non-conformance during in-process inspections directly from data collection terminals
- Record inspection results at every manufacturing step directly in an easy-to-use interface
- Specify user-defined inspection points and attributes
- Collect all relevant data required for quality and defect analysis
Our Customers are Our Purpose and Our Strength

This was March 2020 and then COVID-19 hit. If we were still using the old FoxPro system and the manual way of operating, I don’t think we could have had everybody go home and work remotely.
With OmegaCube ERP, we were able to work remotely and still operate during the pandemic. Even though we just completed setting up our initial ERP system, our employees were able to run with it while working remotely and that ended up working out great. The system operated efficiently for sales, engineering, and purchasing.
I don’t think we could have done that with the old FoxPro system as we did with OmegaCube ERP. So the timing of implementing OmegaCube ERP was perfect.

OmegaCube has gone to a painstaking amount of work to make sure that we can instantaneously navigate to all the data we need. That applies to the front office as well as the shop floor, which means we’re saving time, doing more work and cutting costs throughout the operation – without sacrificing quality or delivery. When customers call for information on orders we can give them answers right away. That used to take 10 minutes or more. Being able to answer questions quickly gives our customers a real sense of confidence in us and shows we’re in control of our manufacturing process.”

I sit down every morning and look at a report which tells me how much I owe, how much I have coming in and helps me plan for incoming orders. It’s become an integral part of running my business effectively, efficiently and profitably, and we could add six more businesses without having to change our software.”
Browse through our Latest ERP and Technological Insights
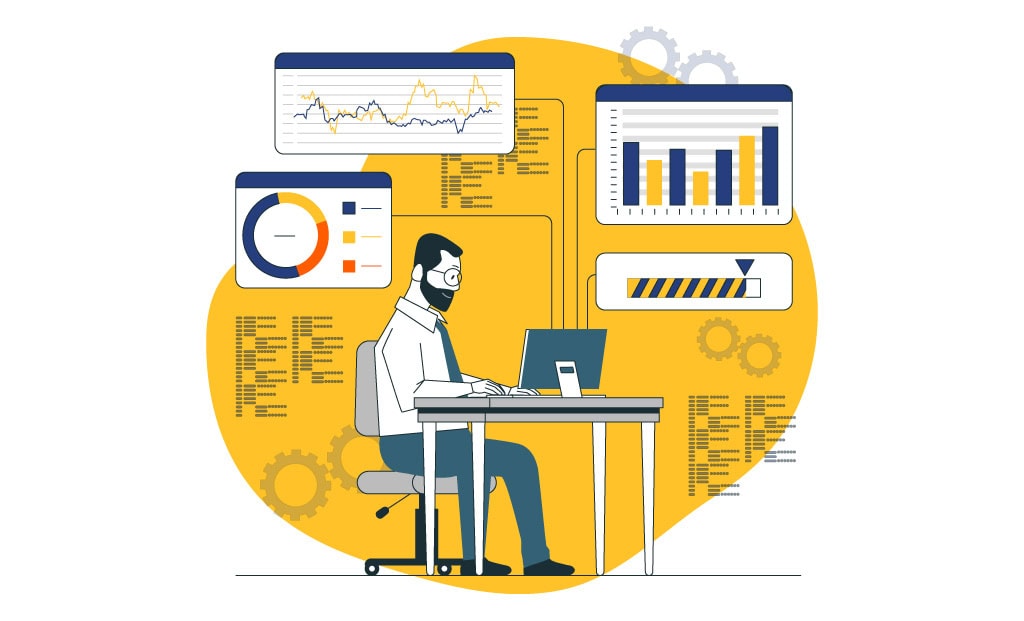
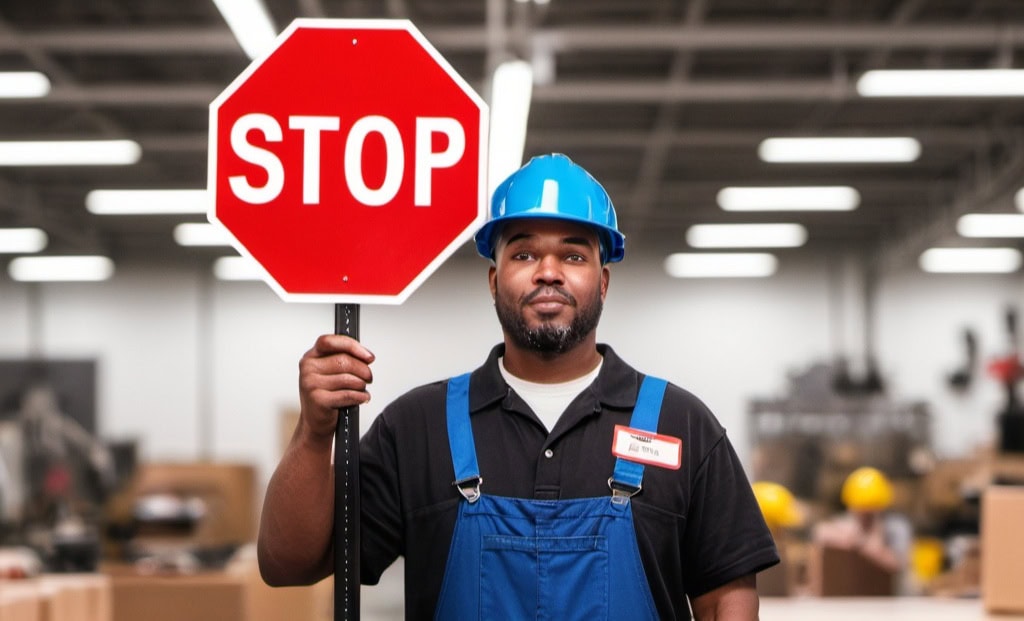
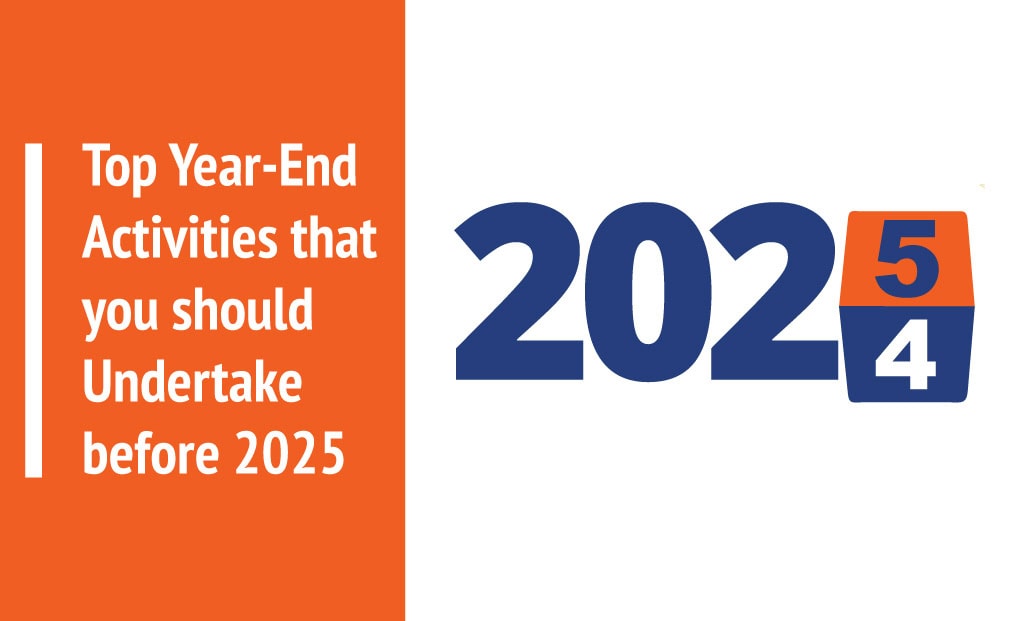
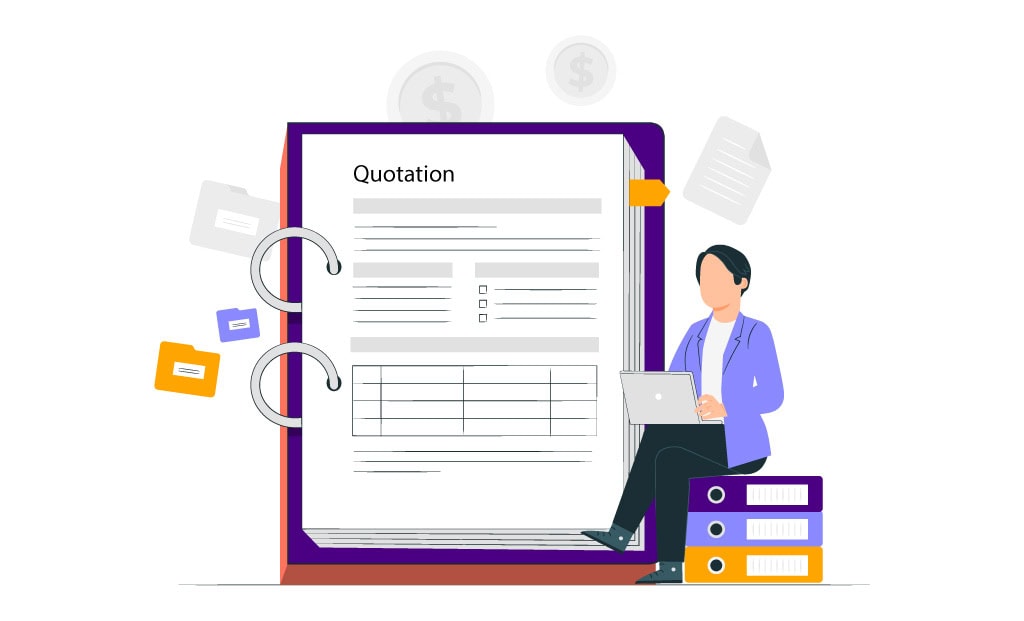
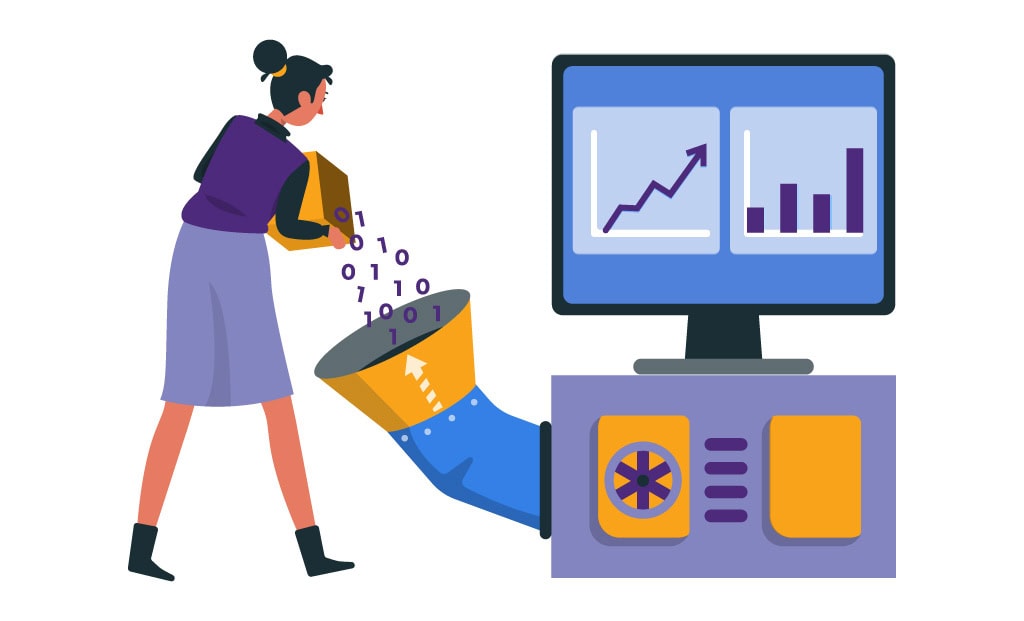
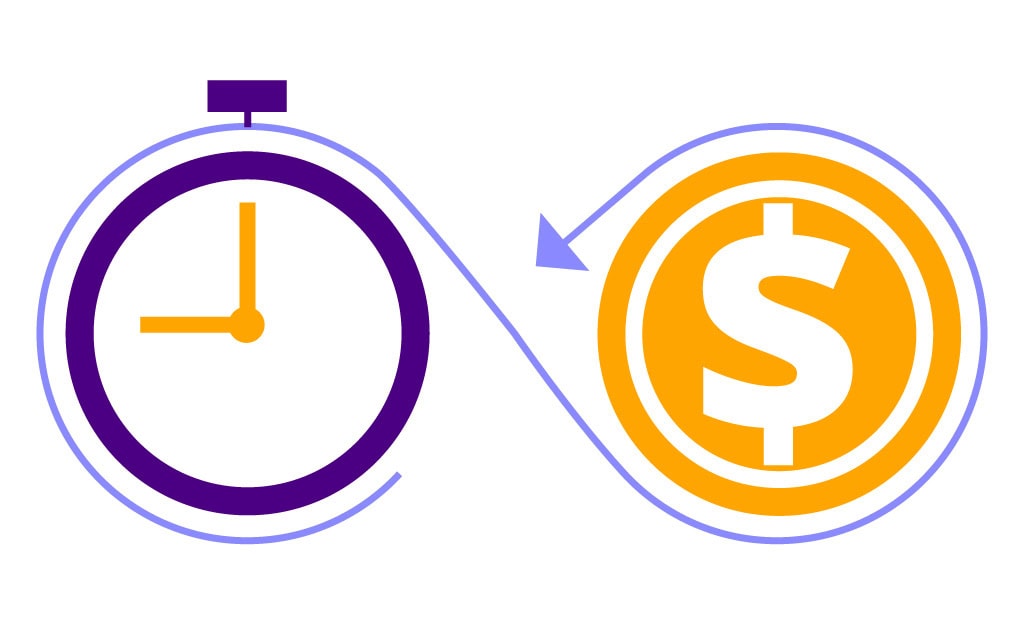
FAQ
Work Order Management in OmegaCube ERP helps manufacturers to accurately schedule work orders, prioritize based on customer requirement and dispatch them to the shop floor. They can track work order progress throughout the production process, combine work orders and increase overall manufacturing efficiency.
Inventory Management in OmegaCube ERP enables manufacturing enterprises to efficiently plan, procure, build, manage and track inventory in real time. They can maintain optimum inventory levels, improve material traceability and cash flows by ordering the right materials at the right time for the right cost from the right supplier.
Planning and Scheduling in OmegaCube ERP automates production planning and scheduling workflows by taking material, manpower and machine availability into consideration. It improves capacity utilization during production, operator productivity, optimum supply chain planning, and on-time delivery to customers.