Electronic Data Interchange (EDI)
OmegaCube ERP’s Electronic Data Interchange (EDI) functionality helps you to speedily exchange accurate and reliable data with your branches, suppliers, third-party vendors, customers etc.
It eliminates traditional and manual communication methods leading to streamlined workflows, faster operational & production life-cycles, improved supplier relationships, supply chain efficiency, increased cash flow, and productivity.
Key Benefits of Electronic Data Interchange (EDI)
- Exchange critical information with your suppliers and third-party vendors in real-time.
- Reduce communication gaps, increase supply chain efficiency, uphold supplier relationship & reputation, and increase the speed of operations.
- Reduce overhead costs that go into procuring paper, printing, storing, filing, and posting them to stakeholders.
- Reduce human efforts and costs that go into maintaining them.
- Eliminate manual keying of information both at the customer and manufacturer’s end at every transaction stage.
- Reduce typo errors, misinformation due to bad handwriting, missing documents, etc.
- Reduce usage of papers to naught as transactions are conducted electronically.
- Efficient and quicker means of conducting transactions.
- Environment friendly, as carbon footprints are reduced due to less paper usage.
- Automate business processes and tranasctions.
- Eliminate manual and human intervention.
- Speed up manufacturing lifecycle by over 60%.
- Secure transactions owing to high-security compliance standards and communications protocols.
- Apart from enterprises, financial institutions and banks use EDI on a large scale owing to high security.
Key Features of Electronic Data Interchange (EDI)
- Transact with trading partners for orders, releases, ASN, and invoices.
- Use excel based EDI processor for trading partners where only a download is available.
- Benefit from automatic integration into MRP and scheduling modules.
- Get multiple interface options i.e. Direct, Text, and XML-based.
- Connect to on-premises or online EDI translation packages.
- Automatically compute the net change in demand.
- Utilize exception handling workbench to evaluate supply shortages.
- Supports hosted option and file formats such as ANSI X.12, EDIFACT, Odette, XML, CSV, VDA, etc.
Our Customers are Our Purpose and Our Strength

We’ve lowered lead times and reduced our costs across all four profit centers. The system essentially traces each job from the initial quotation entered in its CRM module through the manufacturing cycle, into the warehouse, out the door and into the billing process. PowerERP does everything we need to operate our business, from shop-floor to front-office.”

If we want to know anything about production, sales, a particular job, maintenance on a job or raw material costs on a job we only have to go one place to look for it. That’s powerful.”

With the capability of handling complex pricing, for instance, I was able to handle various pricing types that are unique to a distribution environment. Using Point-of-sale hand-held applications, order processing has cut down the time it takes for us to replenish shelves at supermarkets. These improvements have translated into increased sales. “Getting our sales and inventory data used to be a nightmare, and now it is clean and easily accessible”.
Browse through our Latest ERP and Technological Insights
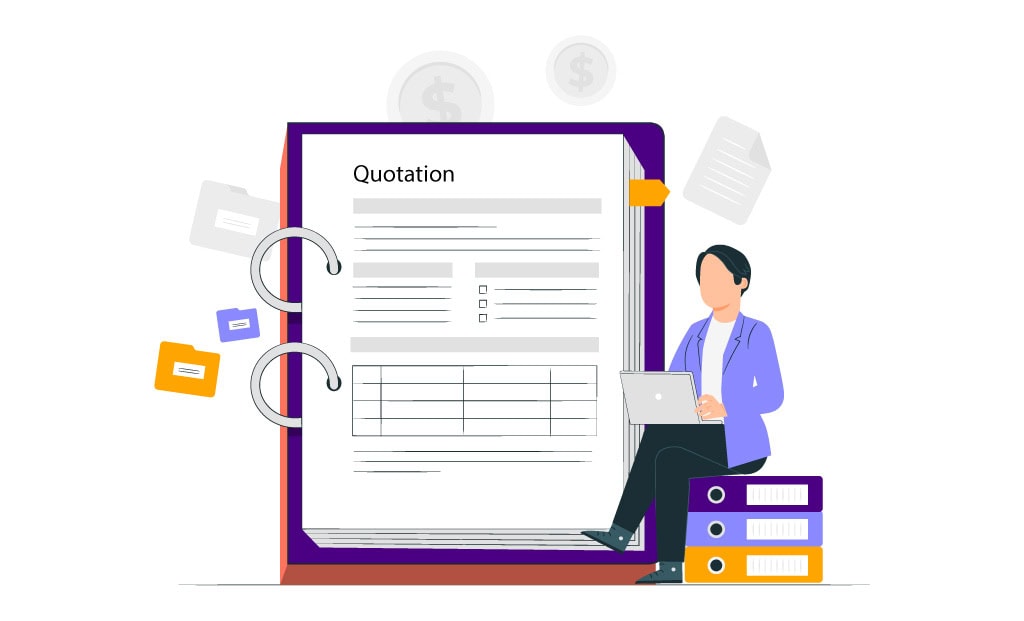
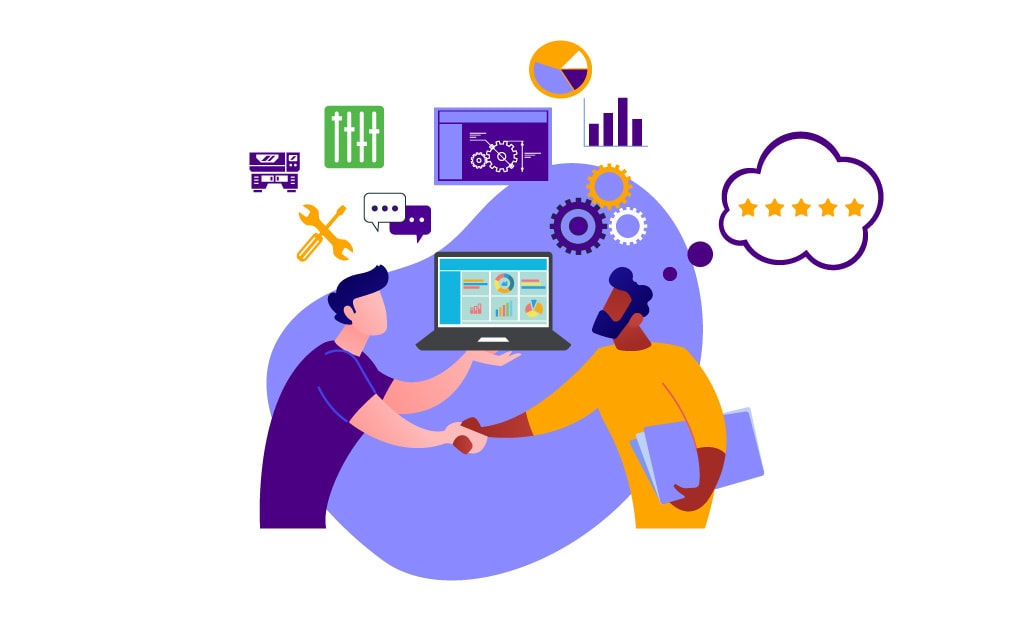
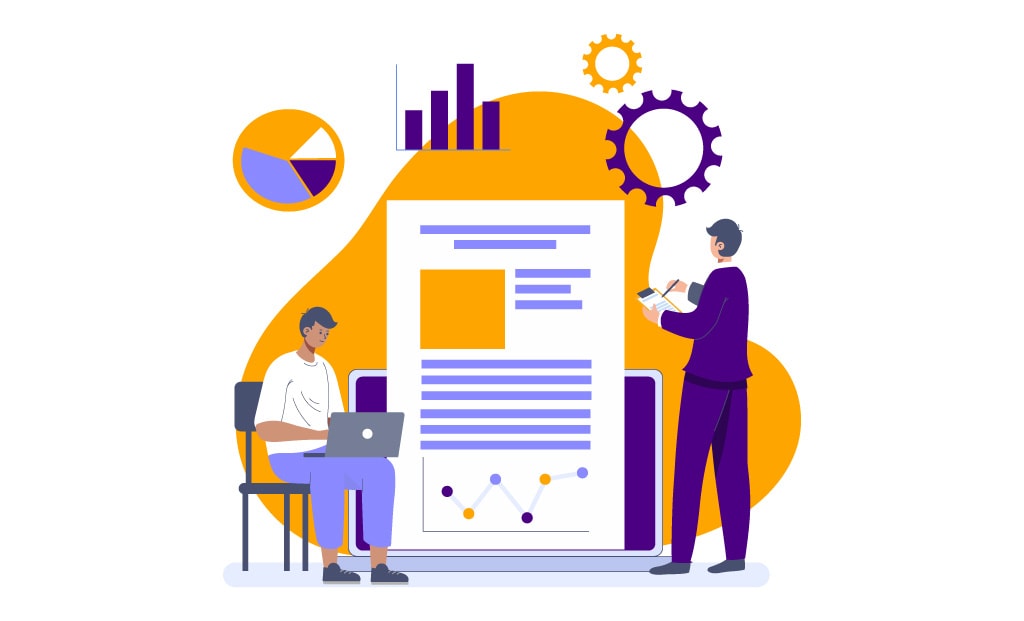
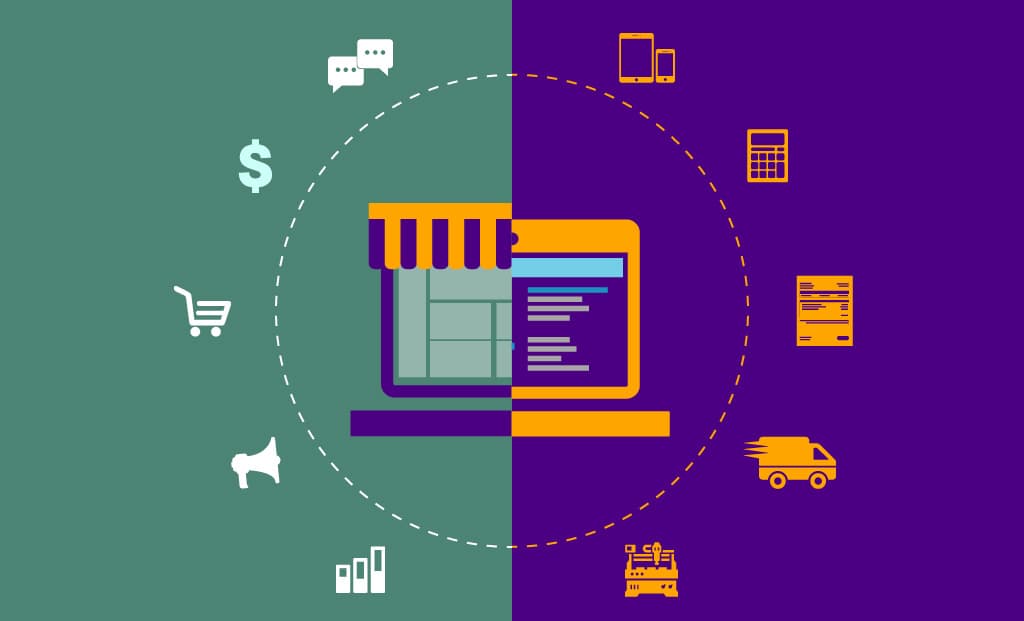
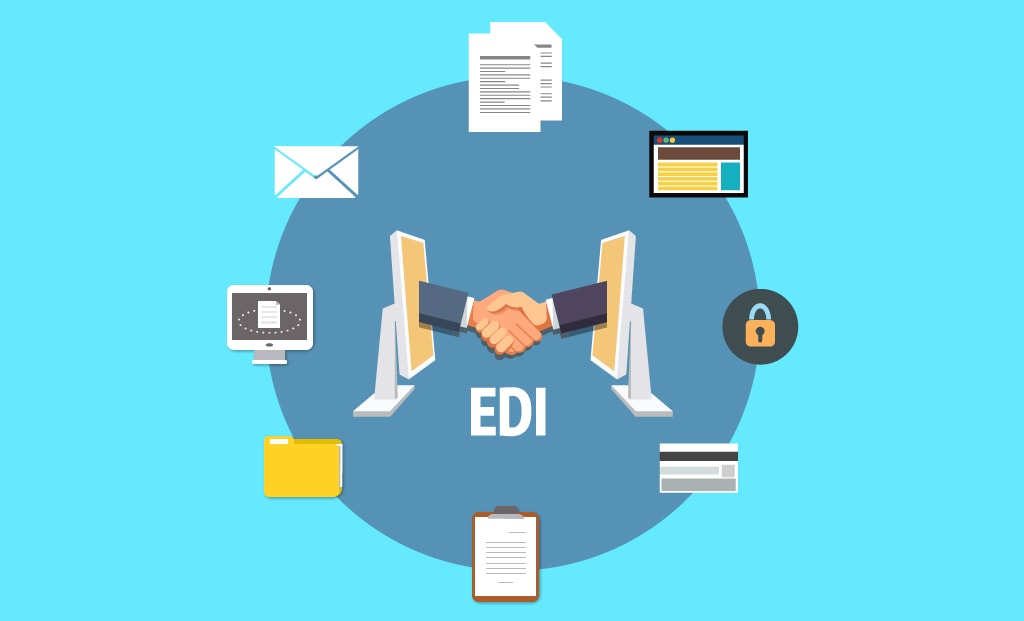
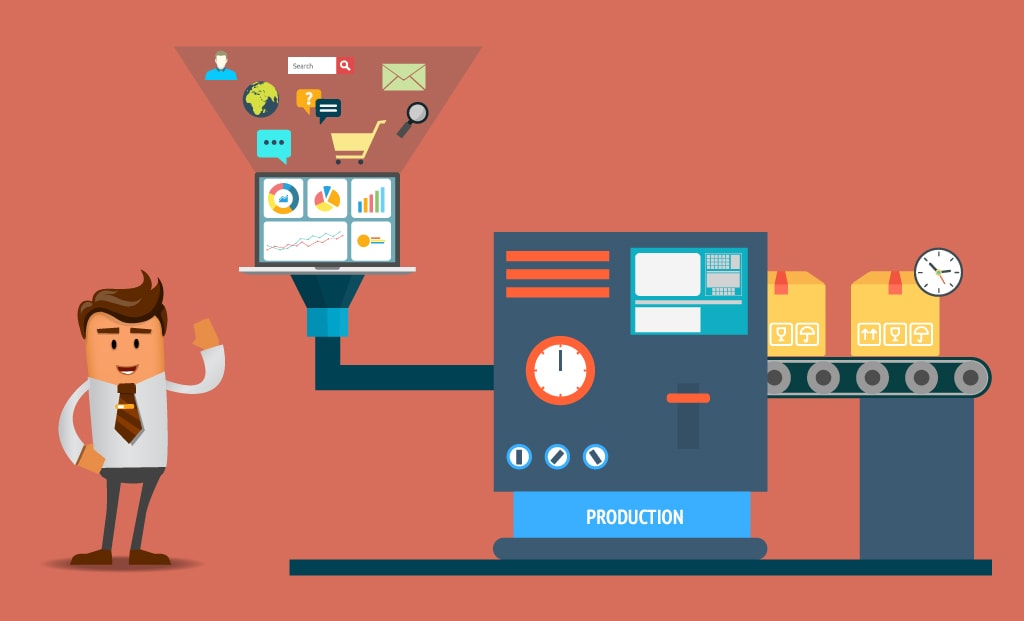
FAQ Headline goes here
Sales Management in OmegaCube ERP automates and streamlines end-to-end sales workflows such as Order Management, Quotation & Estimating, Customer Relationships, and billing. Through advanced capabilities such as CRM and EDI, the sales management module helps manufacturers to improve customer response, order efficiency, and order tracking from order placement till customer shipment.
Suppliers and Purchasing Management in OmegaCube ERP streamline material procurement process from suppliers, improves supplier collaboration, reduces procurement cost, improves cash flow and inventory management.
Material Requirement Planning (MRP) in OmegaCube ERP helps manufacturers to accurately calculate the amount of materials and components to manufacture a product. The calculation takes into account, the total number of orders in-hand, existing inventory levels and the delivery due date. Based on these parameters, material procurement is initiated from approved suppliers.