- OmegaCube Technologies
- Solutions
- By Industry
- Automotive
Reduce ‘product planning to delivery’ gap, ensure continuous compliance to TS/ISO 16949 standards, minimize production and quality costs.
Automotive
Key Benefits to Automotive Manufacturers
- Speed up business cycles, and cut down EDI processing & dynamic planning times by over 50%.
- Save time by eliminating errors, and redundant tasks by referring to the latest revisions using Revision Control.
- Adhere to TS/ISO 16949 standards right from product planning to delivery via automation of key quality parameters.
- Reduce recall rates, rework & processing costs by proactive identification of defects.
- Eliminate overheads, delays and save huge revenue with real-time Inventory Management.
- Reduce manual work and human dependency by automating key EDI processes.
Top Functional Areas in OmegaCube ERP for Automotive
- Electronically transact with your trading partners for order status, releases, ASN & invoices
- Maintain EDI formats in-line with your trading partners through on-premises or online EDI translation packages.
- Track non-conformance through a centralized database integrated with RMA, Shop Floor transactions & Inventory.
- Analyze quality metrics for suppliers, parts, manufacturing, and operations using quality management dashboards.
- Assign tasks, generate automatic emails/reminders, and document corrective & preventive action using 8D methodology.
- Trace the origin of a specific part/unit/entire product batch located within the supply chain.
- Maintain lot items using Bar Code Scanner and Auto Inventory Transfer (Bar Code).
- Track heat numbers, material composition data and attach mill certificates to lot numbers.
- Gain complete visibility to document life-cycle along with time stamps & personnel details.
- Link workflow and design documents to BOMs, inventory, supply chain, and customers.
- Prevent unauthorized and simultaneous document edits.
- Get real-time visibility into inventory levels for quick order fulfillment.
- Auto-update of inventory levels owing to integration with sales & purchase, order management, and accounting systems.
- Auto reorder of raw materials, and components in case of shortage detected by the inventory monitoring system.
- Schedule key EDI processes such as Accounting, Inventory control, Revision Control, etc.
- Synchronize operations between internal departments, with your vendors & customers.
- Manage simultaneous operations that can possibly cause conflicts.
- Have a complete view of in-process jobs on the shop floor along with their status.
- Integrated scheduling to determine start/stop times for all assembly and sub-job operations.
- Have visibility of shop-floor performance including efficiency ratios via manufacturing metrics.
- Record time and job information quickly and accurately.
- On-demand label printing for continuous production.
- Generate & print bar code labels using an in-built report writer or with industrial applications such as Bartender.
- Electronically transact with your trading partners for order status, releases, ASN & invoices
- Maintain EDI formats in-line with your trading partners through on-premises or online EDI translation packages.
- Track non-conformance through a centralized database integrated with RMA, Shop Floor transactions & Inventory.
- Analyze quality metrics for suppliers, parts, manufacturing, and operations using quality management dashboards.
- Assign tasks, generate automatic emails/reminders, and document corrective & preventive action using 8D methodology.
- Trace the origin of a specific part/unit/entire product batch located within the supply chain.
- Maintain lot items using Bar Code Scanner and Auto Inventory Transfer (Bar Code).
- Track heat numbers, material composition data and attach mill certificates to lot numbers.
- Gain complete visibility to document life-cycle along with time stamps & personnel details.
- Link workflow and design documents to BOMs, inventory, supply chain, and customers.
- Prevent unauthorized and simultaneous document edits.
- Get real-time visibility into inventory levels for quick order fulfillment.
- Auto-update of inventory levels owing to integration with sales & purchase, order management, and accounting systems.
- Auto reorder of raw materials, and components in case of shortage detected by the inventory monitoring system.
- Schedule key EDI processes such as Accounting, Inventory control, Revision Control, etc.
- Synchronize operations between internal departments, with your vendors & customers.
- Manage simultaneous operations that can possibly cause conflicts.
- Have a complete view of in-process jobs on the shop floor along with their status.
- Integrated scheduling to determine start/stop times for all assembly and sub-job operations.
- Have visibility of shop-floor performance including efficiency ratios via manufacturing metrics.
- Record time and job information quickly and accurately.
- On-demand label printing for continuous production.
- Generate & print bar code labels using an in-built report writer or with industrial applications such as Bartender.
Enterprise solution for every industry
Our Customers are Our Purpose and Our Strength

People expect that an ERP system will allow them to run their business exactly how they want to, but more often than not, the ERP system is the glove and you’re the hand that has to squeeze into it.
Not so with OmegaCube. They helped us meet our vision rather than requiring us to formulate our processes around their solution.

There were competitors who weren’t as flexible as OmegaCube. OmegaCube assured us that they can do whatever we want them to do and they can adjust to fit our organization and not the other way around. They provided us insights into what they did for other customers and we saw what work they have done for them. This was, eventually, the final selling point for us.”

This was March 2020 and then COVID-19 hit. If we were still using the old FoxPro system and the manual way of operating, I don’t think we could have had everybody go home and work remotely.
With OmegaCube ERP, we were able to work remotely and still operate during the pandemic. Even though we just completed setting up our initial ERP system, our employees were able to run with it while working remotely and that ended up working out great. The system operated efficiently for sales, engineering, and purchasing.
I don’t think we could have done that with the old FoxPro system as we did with OmegaCube ERP. So the timing of implementing OmegaCube ERP was perfect.
Browse through our Latest ERP and Technological Insights
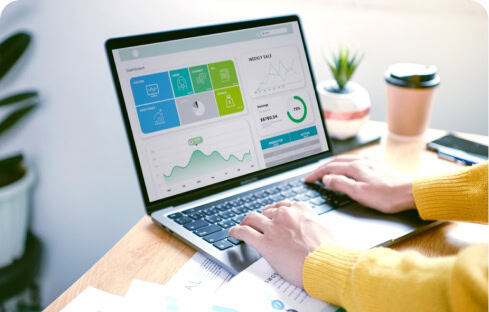
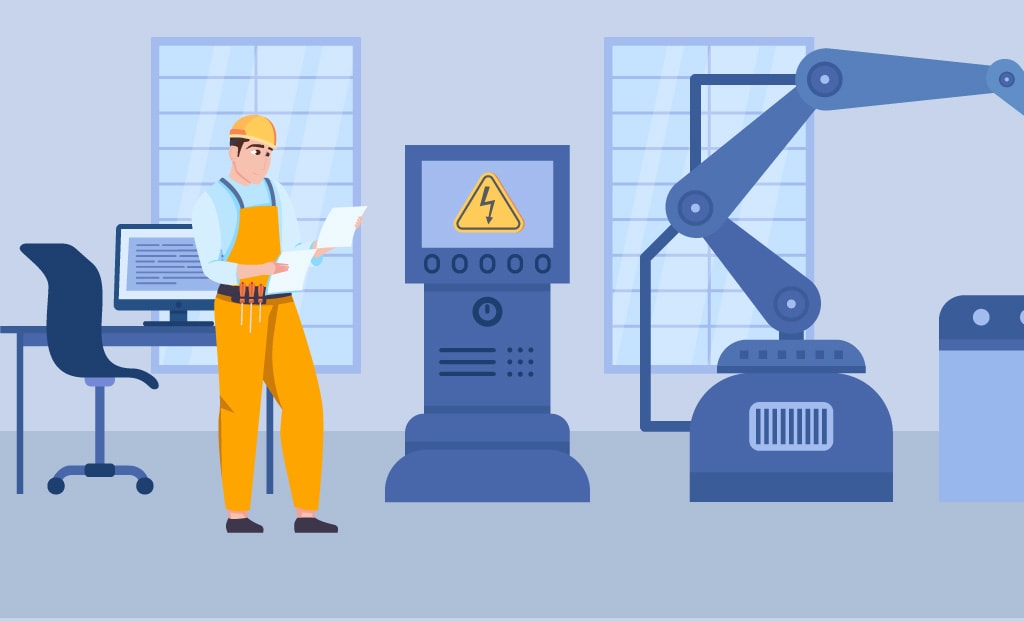
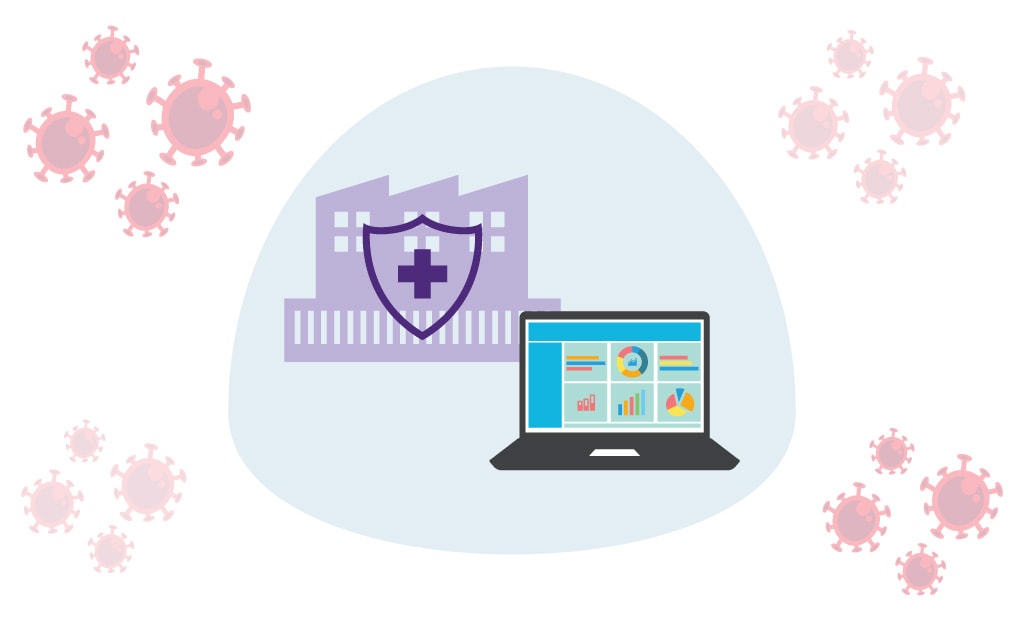
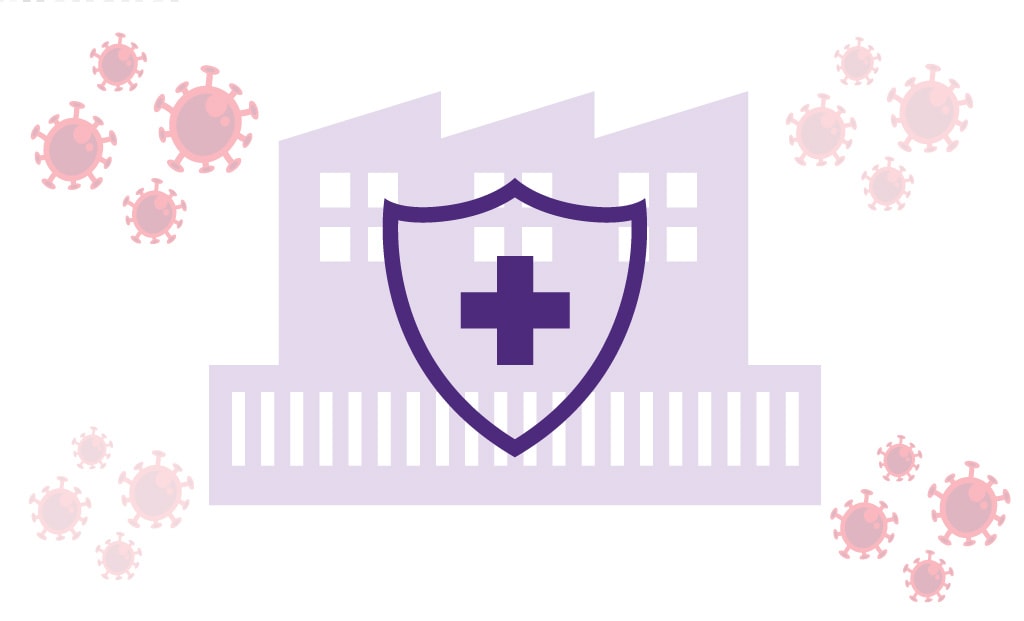
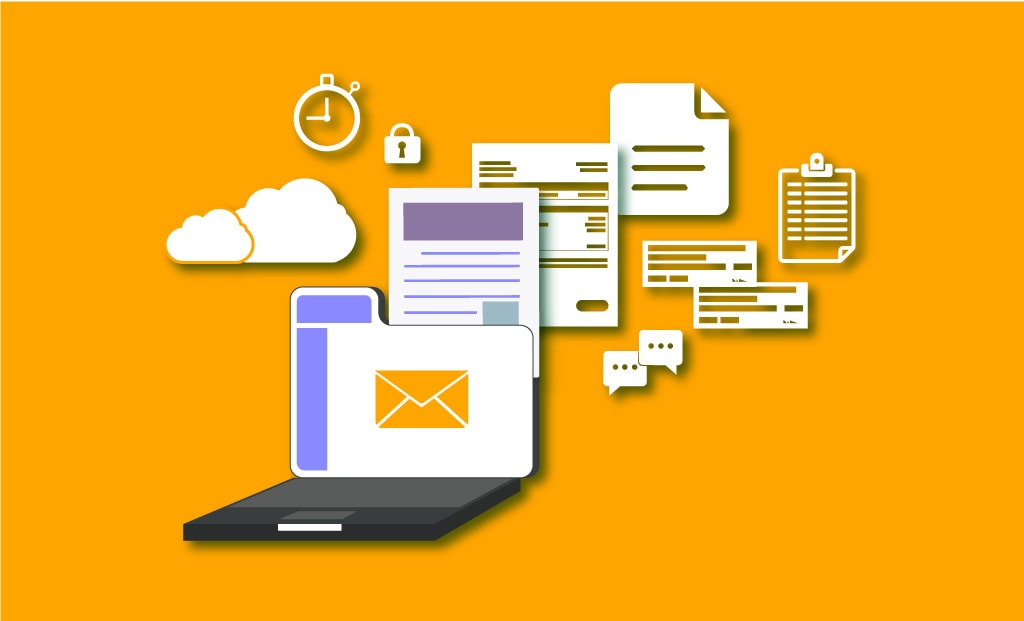
How can you Automate Document Distribution to Improve Enterprise Efficiency and Productivity?
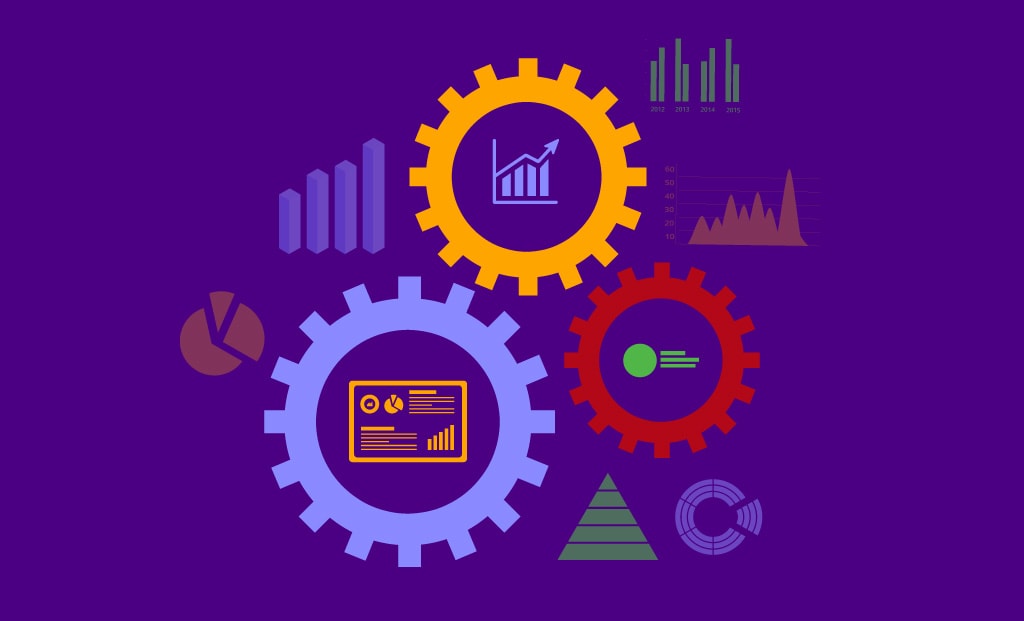