Discrete manufacturers are too often lumped in with process manufacturers, but you know that your operations are different and require separate support systems. Thankfully, many manufacturing ERPs are now designed specifically with discrete in mind.
When you’re looking through these systems, it can be a little tough to choose which is the best fit for your operations. To get started, it’s best to consider four of the biggest decision questions for your software selection.
Guarantee the essentials
Discrete manufacturers can benefit from an ERP, but it must cover some of the basics. While the full list depends on your operations, there are a few uniform requirements.
First and often most important is support for the tracking technology you use, most often RFID and barcode scanners. These tools ensure you have accurate counts for all aspects of your operation and make your ERP better at demand planning as well as order management.
Other must-haves include material requirements planning modules that support multiple functions. An MRP tool within an ERP allows you to control inventory and understand lead times, keeping you lean while ensuring you don’t run out of materials. Plus, everything can be accounted for more easily.
Many discrete manufacturers will also look for product lifecycle tools as a baseline because the nature of your goods includes a defined lifecycle.
Sort by your industry
ERP systems are often designed with certain customers in mind, and you want to find one where you’re the right fit. Narrow your potential list of vendors and platforms by your specific industry so that you get the right quality controls and regulatory support you need.
There are ERPs designed for discreet operations serving the automotive, medical, aerospace, and other industries that all come with unique requirements. If you don’t get something that supports the data or reports that you need, especially when it comes to audits, when you’ll have to spend time and money building out that functionality yourself.
Specialize for your products
After you’ve narrowed down by your industry, considering the products you create and the new designs you might have in the future. Be sure to include the tools that you’ll need to generate new products too.
Get an ERP that covers both CAD and CAM links, but also ask your engineers for other requirements that they have. You might find some needs around your production schedules or support for managing the transition of product design to prototyping and development.
If you’re in an industry like aerospace, where rapid prototyping is becoming the norm, get the functionality that allows you to be a leader, not just a follower.
Address your pain points
The final selection criteria we’re going to mention are your problem areas. Those places causing pain that you need to solve, not just support. Start with a look at your methodology and processes and then see where they lead to issues on your floor.
Look for issues around flexibility, making the best use of your data, addressing vendor changes, or just daily struggles with a poorly designed existing dashboard.
If you’re choosing an ERP to improve efficiency, reduce legacy systems, or one of the many other common issues, then make sure the vendor can show you how its functionality specifically speaks to those problem areas. It’s your best bet to make a smart choice.
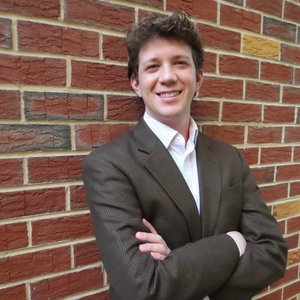
Guest blog by Geoff Whiting
Geoff is an experienced journalist, writer, and business development consultant with a focus on enterprise technology, e-commerce, and supply chain development. Outside of the office he can be found toying with the latest in IoT, searching for classic radio broadcast recordings, and playing the perpetual tourist in his home of Washington D. C.
One Response
Just exploring your services