Bill of Materials (BOM)
With OmegaCube ERP’s Bill of Materials (BOM) management, you can manage, track, and document the physical configuration of your products, parts, and subassemblies.
By providing a detailed breakup of products right down to the last part along with associated costs, it simplifies quotation and material planning. You can quickly access BOMs to create quotations and send them to customers.
With its integration with CAD and Nesting software, you can get a seamless design experience and reduce design-to-delivery cycles.
Key Benefits of BOM Management
Comprehensive BOM structure, breakup, and relationships.
Automate key quality workflows, Quick quotation creation with accurate costing for each part.
Efficient material management, forecasting, and planning with BOM tracking.
A comprehensive view of parts from high level to a low level.
Seamless design experience with CAD integration.
Efficient & accurate inventory management with real-time updates
Better decision-making with accurate BOMs and real-time visibility.
Key Features of BOM Management
- Generate single or multi-level Bill of Materials.
- Define multi-level BOM from templates or from scratch.
- Edit default routings and BOMs.
- Define rules for BOM generation based on option selection.
- Define rules for single or multi-level routings based on options.
- Associate phantom & standard item BOM to options.
- Setup conditional rules for BOM calculations.
- Define main and alternate BOM/routing.
- Allows pricing, BOM, and routing rules.
- Explode BOMs from high level to lowest level.
- View item cost, quantity, procurement date, unit of measurement, and part info.
- Import BOMs from CAD design software such as Auto CAD and SolidWorks.
- Push newly created/updated BOMs to OmegaCube ERP.
- Auto-update of inventory based on BOM creation/update within ERP.
- Use scripting engine to create highly advanced rules to generate manufacturing BOMs based on configuration
- Revision tracking for finished products, BOM items and routing changes
- Ability to track revision numbers at every level of BOM
- Full history of previous revisions
- Recalculation of finished product cost based on change of BOM or routings Engineering change release
- Automatically create master Item and BOM records from the product configurator
- Use the product configurator to select options and generate pricing, BOM, and routing data
- Information on the list of affected documents linked to the given item and revisions.
- Dispatch BOMs via CAD interface to the shop floor.
- Release whole or part of BOM towards production.
- Select BOM routing from Work Order or Master.
- Communicate changes to BOM to the shop-floor before production.
- Track as-built Bill of Materials on re-manufactured equipment.
- Directly access respective BOM from within the Work Order that is scheduled on a particular work center.
- Create work orders from a particular BOM.
- Provide BOM visibility to suppliers and vendors.
- Copy top-level or multi-level BOM to quote estimate.
- Modify BOM and routing details after copying to quote estimate.
- Create BOM Routing Master From Quote.
- Maintain a comprehensive revision history of BOM and routing.
- Save multiple BOM revisions and track its history right from its creation.
- Track and manage change requests through ECNs, edit history, user permissions, and change approvals.
- Flexible cost rollup for single and multi-level BOMs.
- Auto-rollup of lower-level item costs to the higher-level item costs.
- Auto-reflection of changes done to a particular item across the entire BOM.
- Generate automatic credit memos from purchase returns.
- Conduct two way reconciliation of AP invoice with goods receipts.
- Conduct batch payment or manual payment processing.
- Conduct automatic calculation of discounts.
- Conduct down-payment processing for full or partial payments.
- Print checks for vendors using laser, dot-matrix or other methods.
- Review check batch numbers before printing checks.
- Write checks from multiple bank accounts, and credit lines.
- Block invoices from payments.
- Track accrued payables.
- Positive Pay Integration.
- Establish and track recurring Invoices & Payments.
- Conduct 3-way matching for payables and transactions.
- 1099 processing.
- Automatically create Invoicing and Credit Memo from shipping and returns.
- Apply sales and expenses directly to General Ledger account numbers.
- Generate automatic credit memos for returned goods.
- Perform batch processing from bank deposits.
- Apply cash by Bill to, full and partial payments.
- Auto calculation of discounts with ability to override.
- Receive and apply down-payments and advances.
- Sort receivables by due dates, invoice numbers, customer details etc.
- Create account statements and dunning letters.
- Drill down to source transactions.
- Reconcile bank transactions posted to cash accounts against bank statements.
- Reconcile each account separately
- Reconcile credit card transactions
- Reconcile bank account to statements.
- Store and access reconciliation history in the centralized database.
- Access flexible Chart of Accounts and sub-accounts.
- Recurring and reversing journals.
- Detailed transactional level general ledger.
- Flexible accounting periods, dates and years.
- Real time transaction postings to General Ledger.
Our Customers are Our Purpose and Our Strength

Our customers have highlighted the reduction in quality issues ever since we adopted OmegaCube ERP into our system because we are not mixing up materials or revisions. OmegaCube ERP ensures that old BOM versions are inactive and we are using the most up-to-date version of the Bill of Materials.”

As soon as jobs are completed everyone knows an order is ready to ship. An email is sent via mobile devices so people throughout the facility are notified no matter where they are. When new jobs are created people can immediately check BOMs and inventory levels, so tools and materials can be ordered within minutes.”
Browse through our Latest ERP and Technological Insights
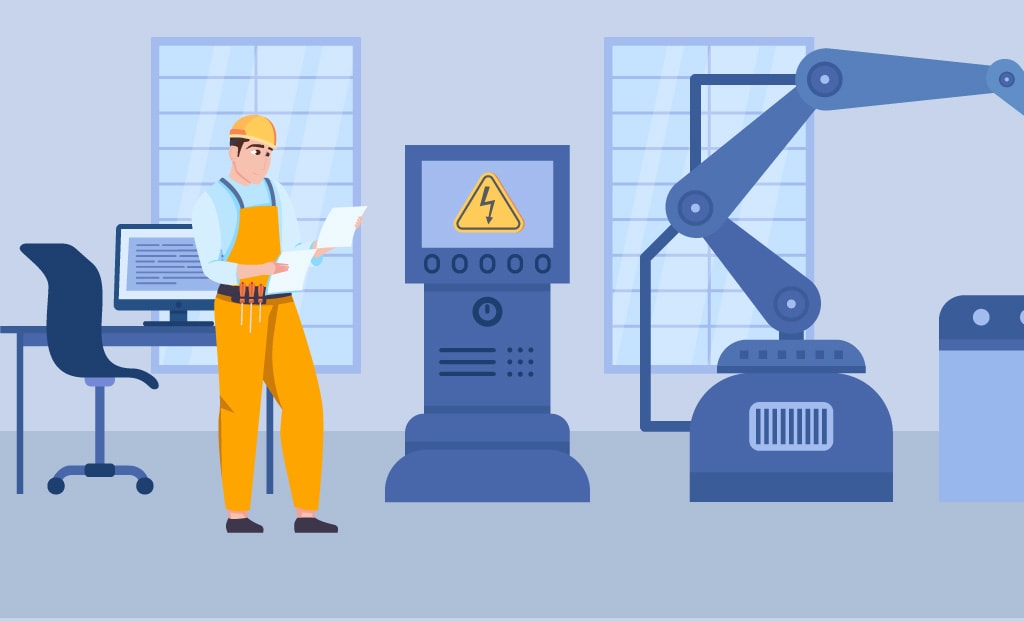
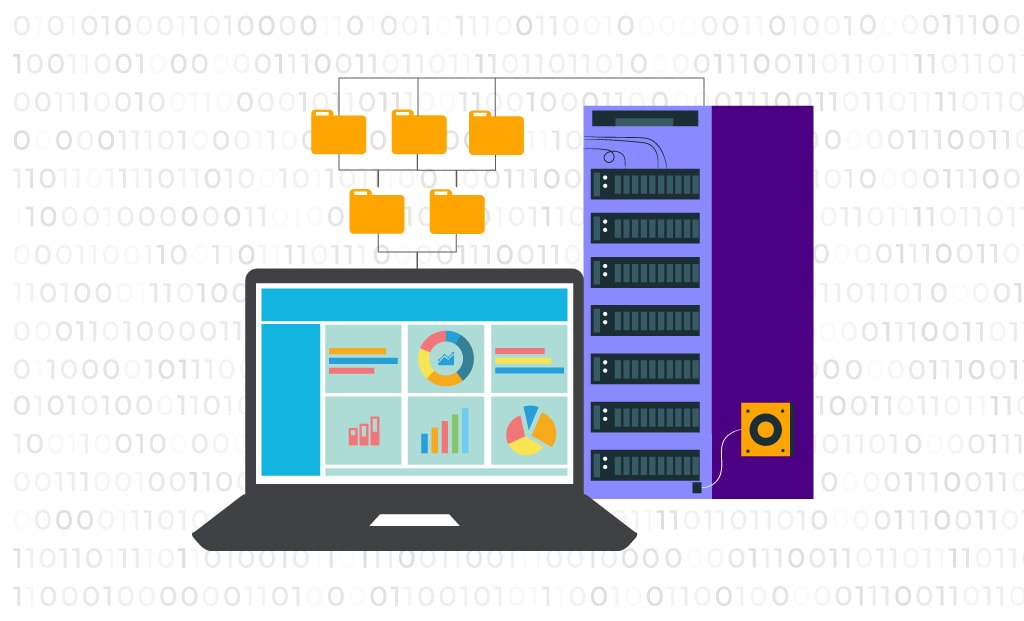
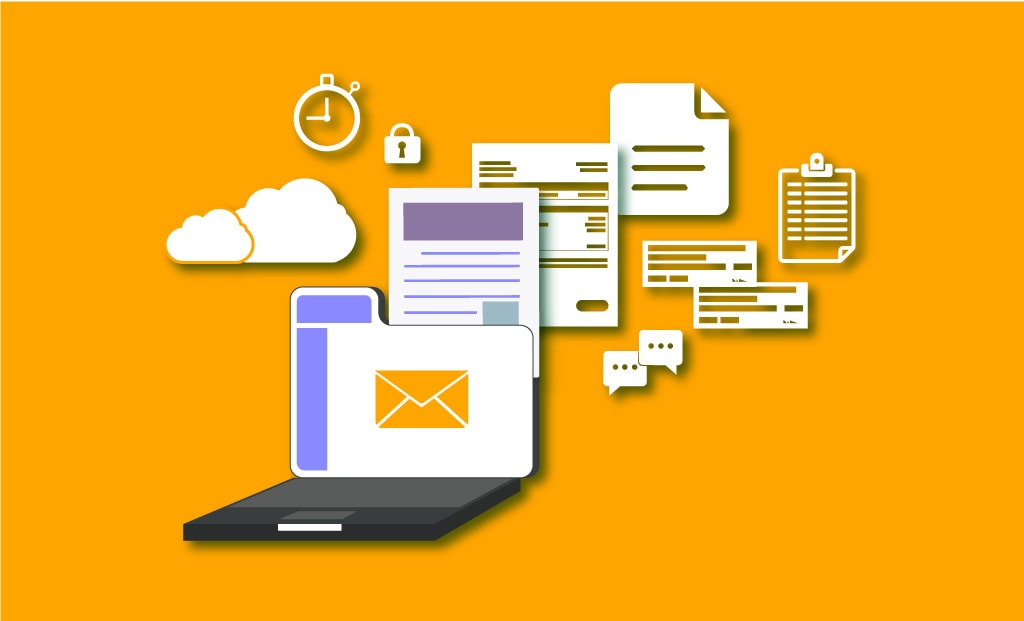
How can you Automate Document Distribution to Improve Enterprise Efficiency and Productivity?
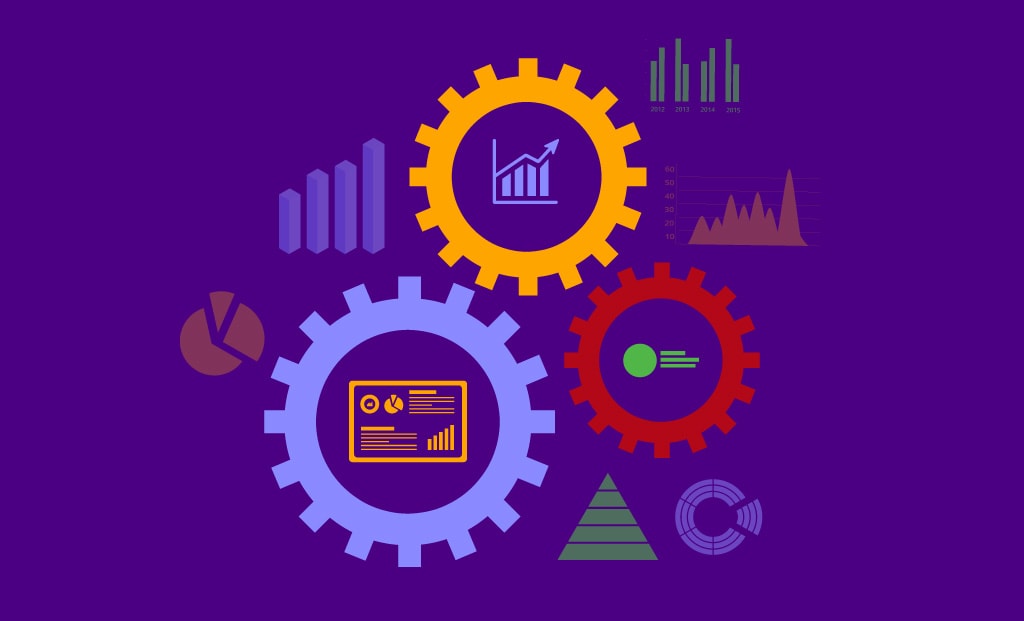
How Advanced Analytics and Business Intelligence Dashboards boost Enterprise’s Efficiency?
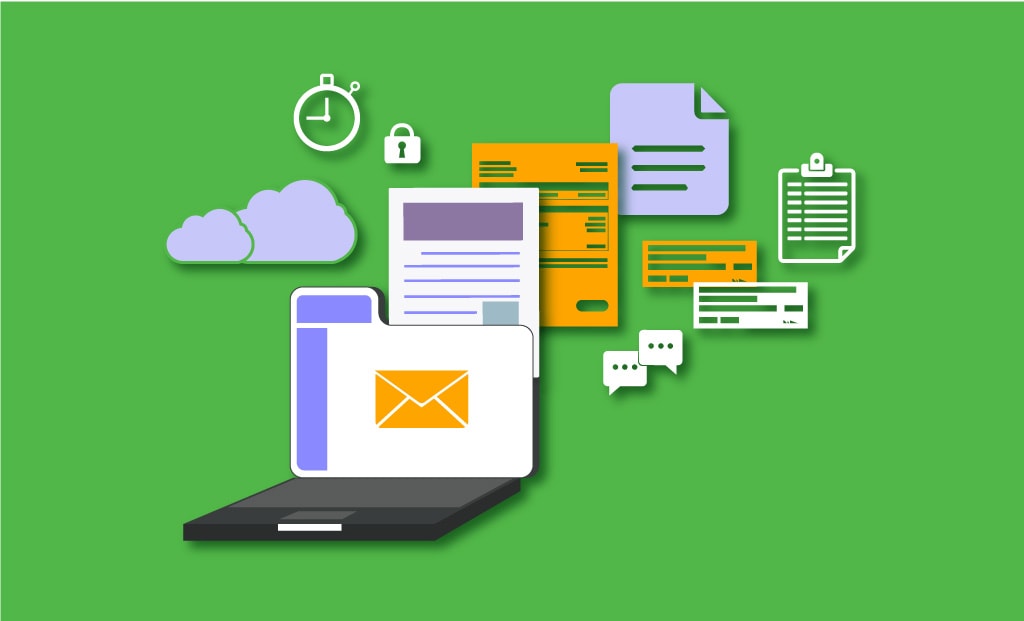
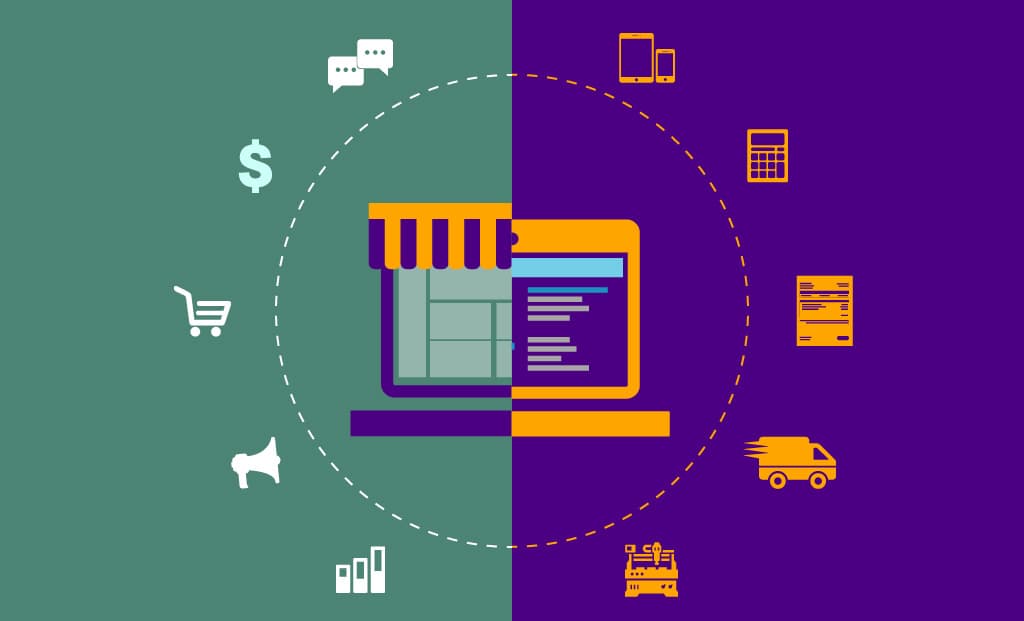