CAD Integration
Key Benefits of CAD Integration
- Easy-to-integrate with a wide array of CAD applications.
- Automate BOM import and reconciliation.
- Various configuration options for sharing design and product data.
- Combine CAD designs with manufacturing to reduce time and costs.
- Have complete control over complex designs and specifications within the ERP during the design stage itself.
- Avoid production delays by dispatching BOMs via CAD interface to the shop floor.
- Maintain up-to-date inventory based on constantly changing designs.
- Minimize the overall impact of engineering changes on the entire production process.
- Eliminate error-prone and time consuming manual data entry.
Key Features of CAD Integration
- Import Bill of Materials (BOM) from CAD software such as AutoCAD, SolidWorks, etc.
- Import material data from Cabinet Vision.
- Keep inventory up-to-date with the help of imported BOMs from CAD software.
- Incorporate design changes via the CAD interface and update it to the ERP.
- Instant auto-update of design changes & requirements to master design documents, sales orders, and work orders.
- Instantly share designs with customers and suppliers through EDI to ensure total collaboration and transparency.
- Get rule-based solutions for configure-to-order, make-to-order, assemble-to-order, and engineer-to-order environments.
- Set up your own sequence of questions, screen layouts, color schemes.
- Attach drawings, specifications, notes, etc. to the configured product.
- Define a multi-level bill of material using templates or from scratch.
Our Customers are Our Purpose and Our Strength

People expect that an ERP system will allow them to run their business exactly how they want to, but more often than not, the ERP system is the glove and you’re the hand that has to squeeze into it.
Not so with OmegaCube. They helped us meet our vision rather than requiring us to formulate our processes around their solution.

There were competitors who weren’t as flexible as OmegaCube. OmegaCube assured us that they can do whatever we want them to do and they can adjust to fit our organization and not the other way around. They provided us insights into what they did for other customers and we saw what work they have done for them. This was, eventually, the final selling point for us.”

This was March 2020 and then COVID-19 hit. If we were still using the old FoxPro system and the manual way of operating, I don’t think we could have had everybody go home and work remotely.
With OmegaCube ERP, we were able to work remotely and still operate during the pandemic. Even though we just completed setting up our initial ERP system, our employees were able to run with it while working remotely and that ended up working out great. The system operated efficiently for sales, engineering, and purchasing.
I don’t think we could have done that with the old FoxPro system as we did with OmegaCube ERP. So the timing of implementing OmegaCube ERP was perfect.
Browse through our Latest ERP and Technological Insights
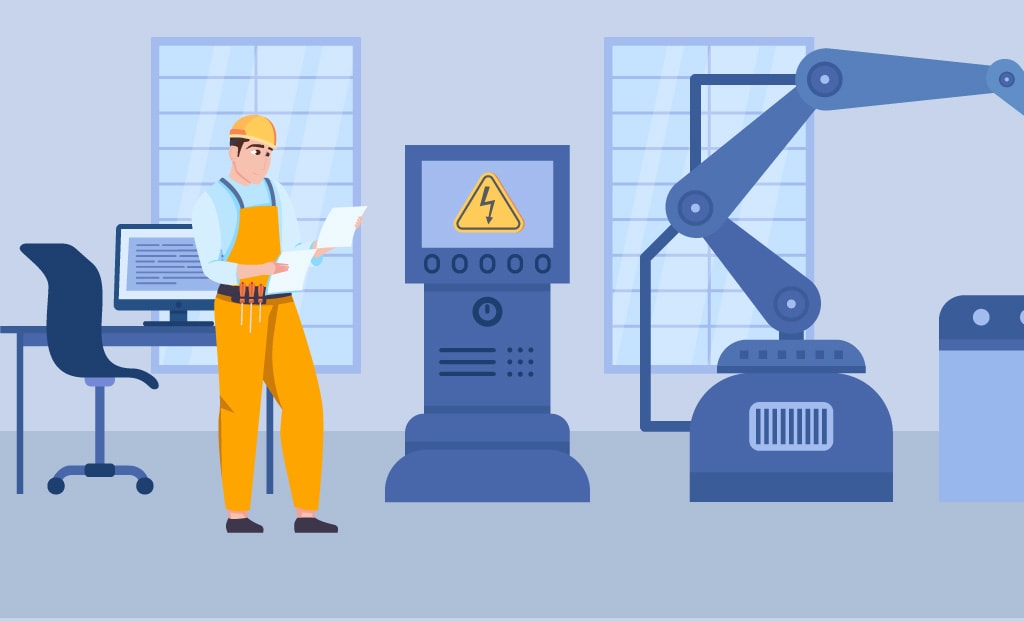
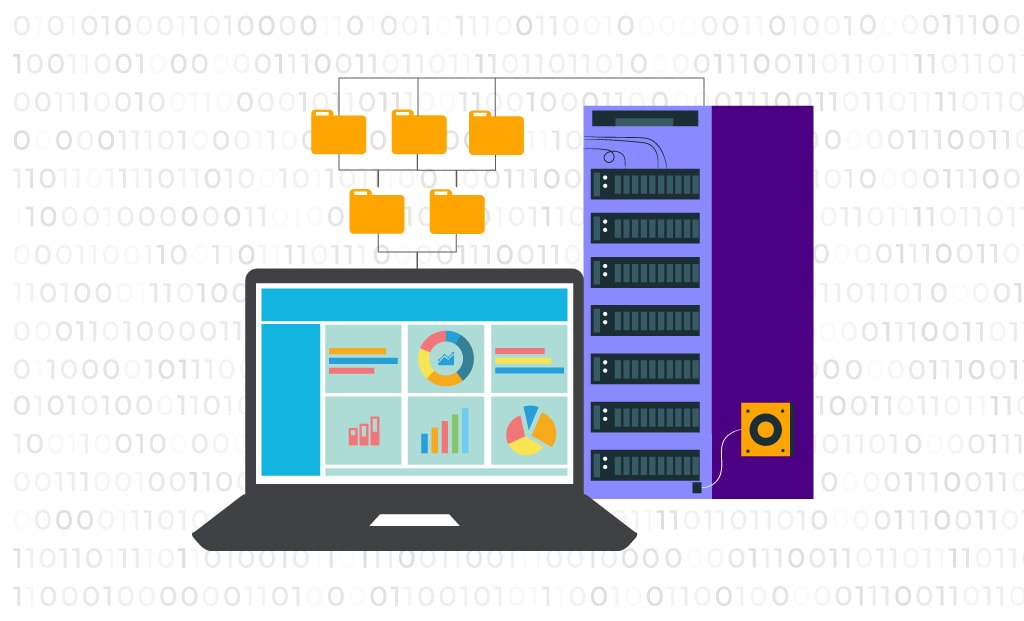
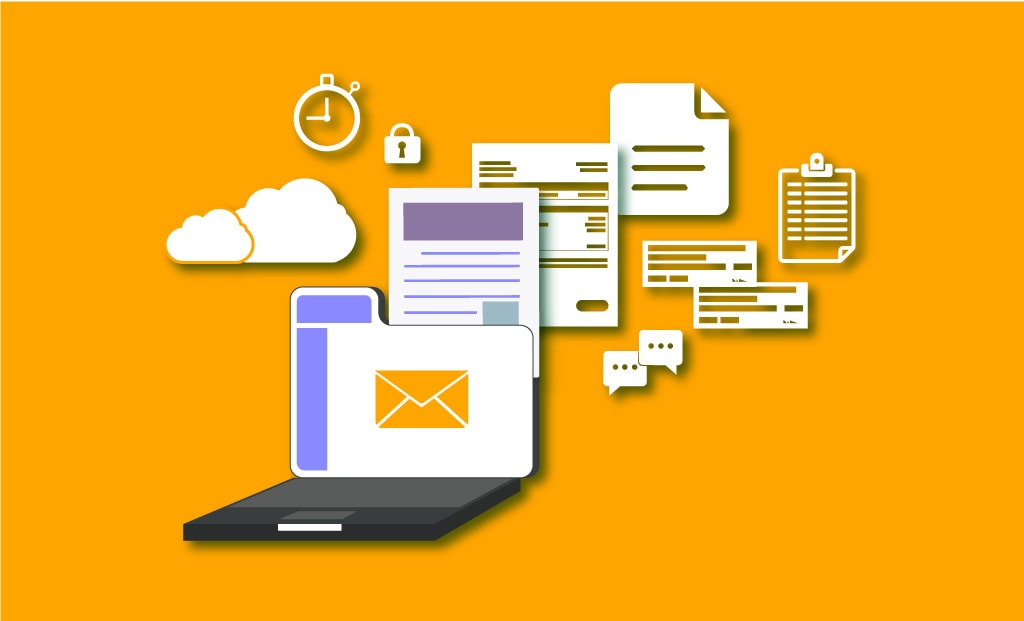
How can you Automate Document Distribution to Improve Enterprise Efficiency and Productivity?
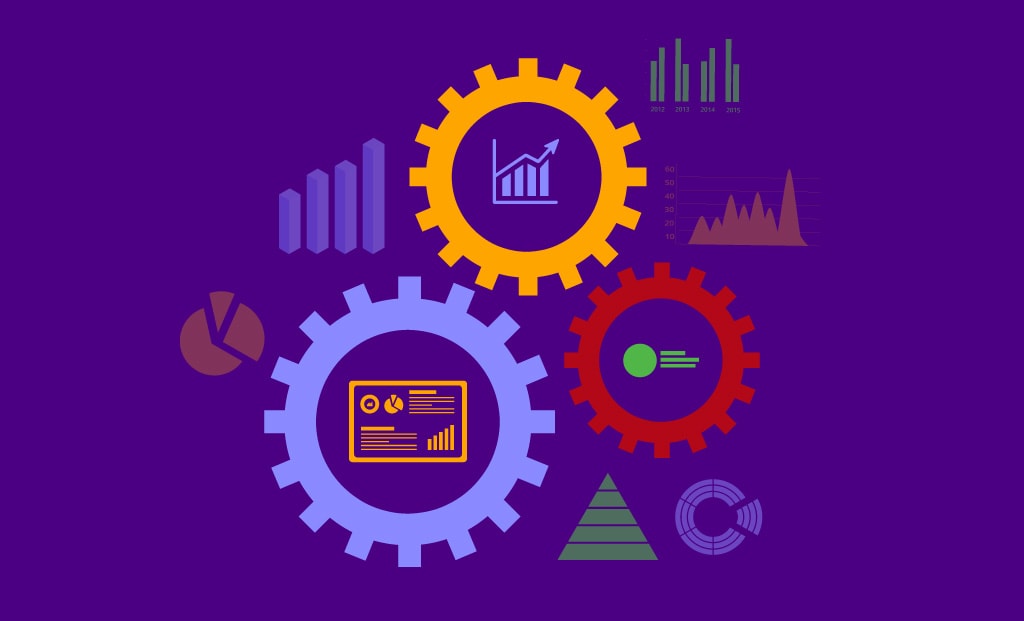
How Advanced Analytics and Business Intelligence Dashboards boost Enterprise’s Efficiency?
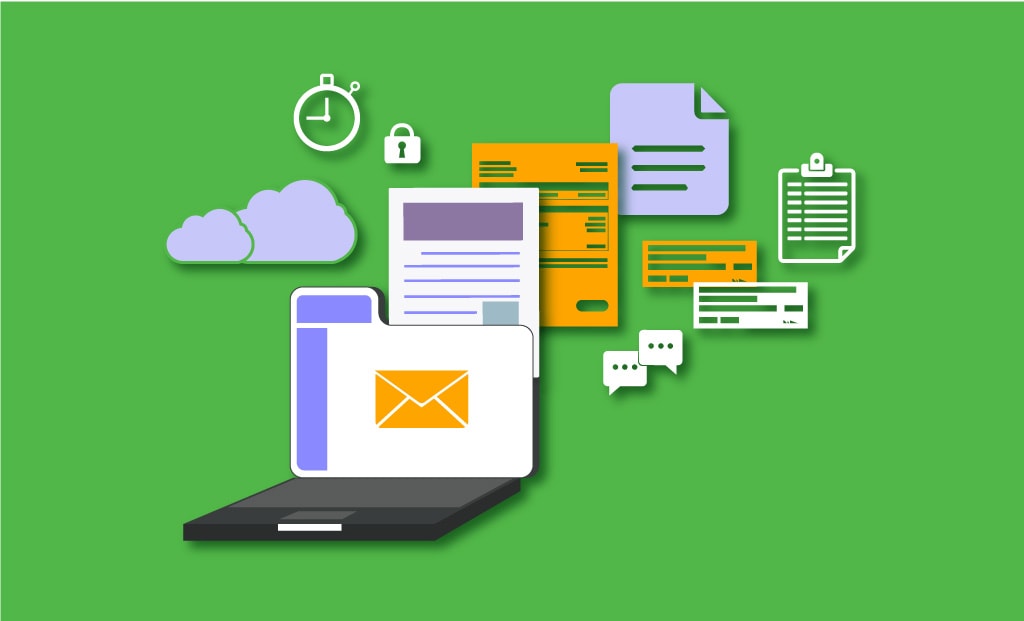
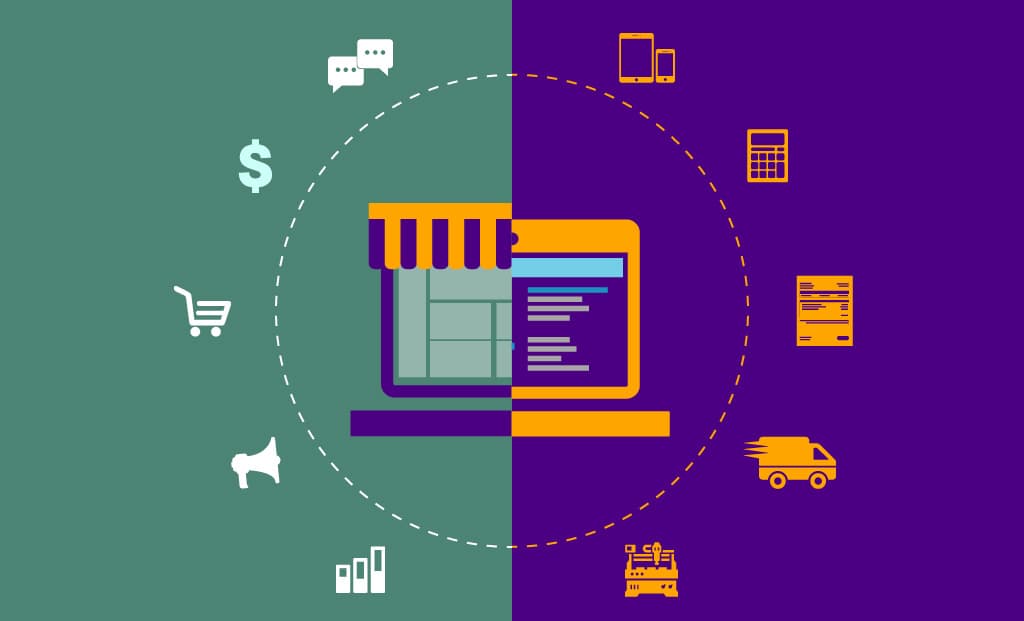
FAQ
Shop Floor Management in OmegaCube ERP helps manufacturers to get real-time view of their shop floor operations, track & improve resource utilization, improve yield quality, meet compliance standards, reduce machine breakdown/idle time and improve overall efficiency.
OmegaCube ERP can be integrated with Nesting Applications such as, SigmaNest and ProNest. Manufacturers can eliminate manual cutting methods & speed up production by automating nesting operations and ensuring easy data flow between the ERP and nesting applications.
Electronic Data Interchange (EDI) in OmegaCube ERP eliminates manual methods of data sharing and enables manufacturers to electronically share accurate and reliable information with branches, suppliers, vendors and customers in a standardized format.