Work Order Management
Key Benefits of Work Order Management
- Save man-hours & cost required to manually create Work Orders and dispatch to the production floor.
- Improve accessibility by using a single dashboard interface to access work orders and related information.
- Automate job scheduling based on Work Order generation.
- Improve response to inventory stock-outs and sudden order due-date modifications.
- Improve capacity planning, demand forecasting with accurate data on entire work order flow and progress.
Key Features of Work Order Management
- Automatically create work orders from Sales Orders, MRP, Quality repairs, and Kanban.
- Manage regular, repair, rework and stock work orders in one database.
- Utilize alternate routings, BOMs and part revisions.
- Generate pick lists based on work centers and move material using bar codes.
- Decide priority of work order based on demand due date.
- Define routing instructions, tools, fixtures, quality inspections to parts on a work order.
- Allow shop operators to view all work order information on a single data collection interface.
- Modify job scheduling, material, labor and machine requirement based on changes to work order due dates.
- Utilize data collected on the work order to update standard routings.
- Collect and provide comprehensive job costing information.
- Link 1st piece inspections, in-process quality inspections to each routing step.
Our Customers are Our Purpose and Our Strength

OmegaCube ERP’s capability to integrate with machine monitoring systems has significantly helped Power Brace to improve capacity utilization to almost 100%. They can track utilization at operator levels and find out reasons for deviation. This helps them with training and certification which in turn helps to improve efficiency. They are also in the process of implementing an incentive program for their operators which would have been impossible earlier without OmegaCube ERP.”

This was March 2020 and then COVID-19 hit. If we were still using the old FoxPro system and the manual way of operating, I don’t think we could have had everybody go home and work remotely.
With OmegaCube ERP, we were able to work remotely and still operate during the pandemic. Even though we just completed setting up our initial ERP system, our employees were able to run with it while working remotely and that ended up working out great. The system operated efficiently for sales, engineering, and purchasing.
I don’t think we could have done that with the old FoxPro system as we did with OmegaCube ERP. So the timing of implementing OmegaCube ERP was perfect.

“If I know how much capacity I have and I know my bookings I can make a decision on whether we can handle a particular order or if we need to buy another machine, subcontract the job or turn down the business. Before OmegaCube ERP, it was pretty much guesswork.”
Browse through our Latest ERP and Technological Insights
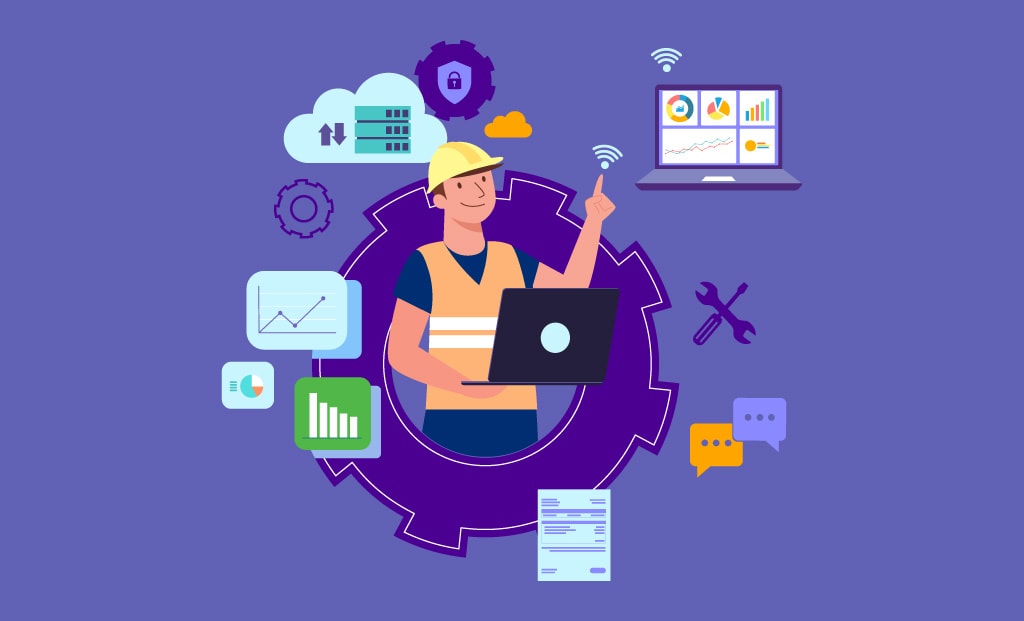
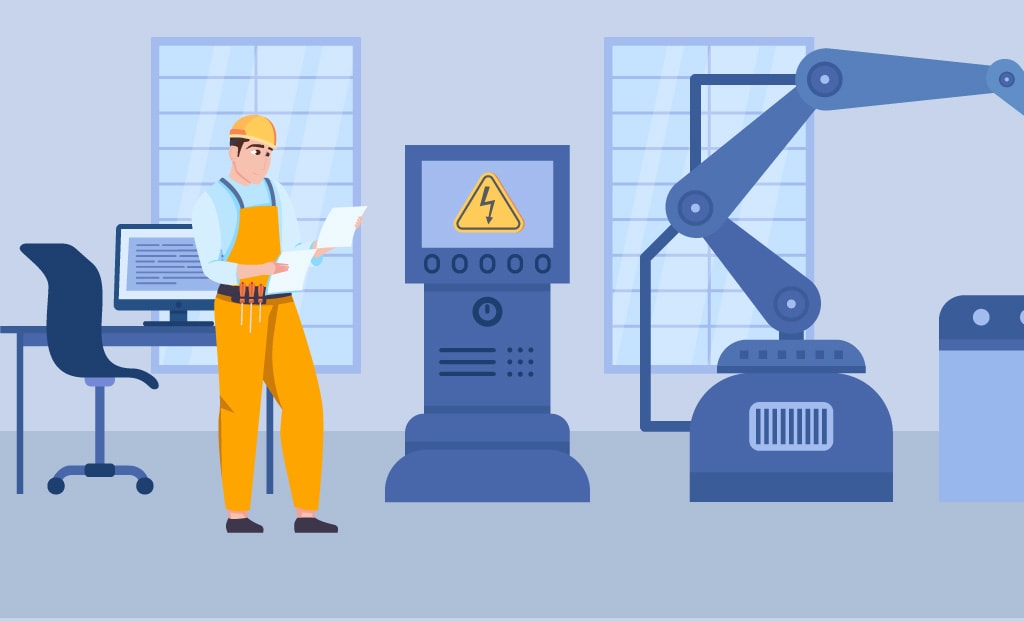
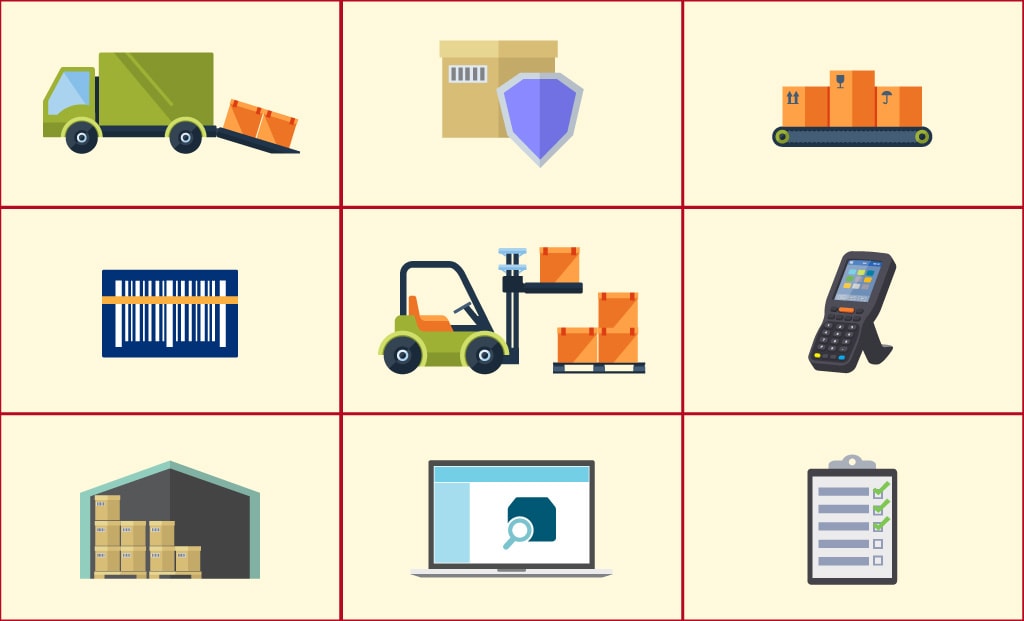
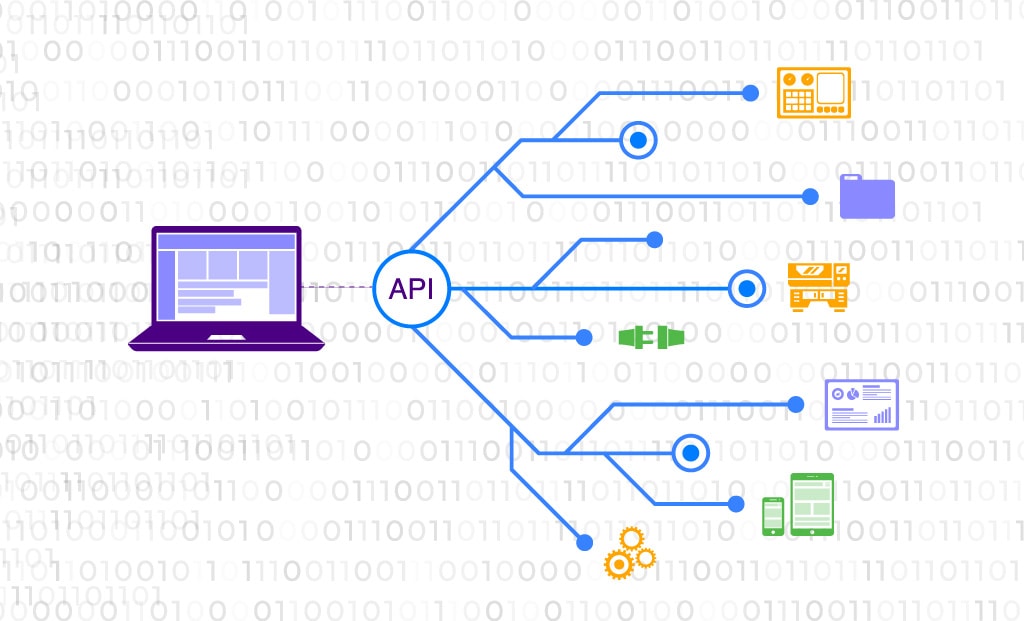
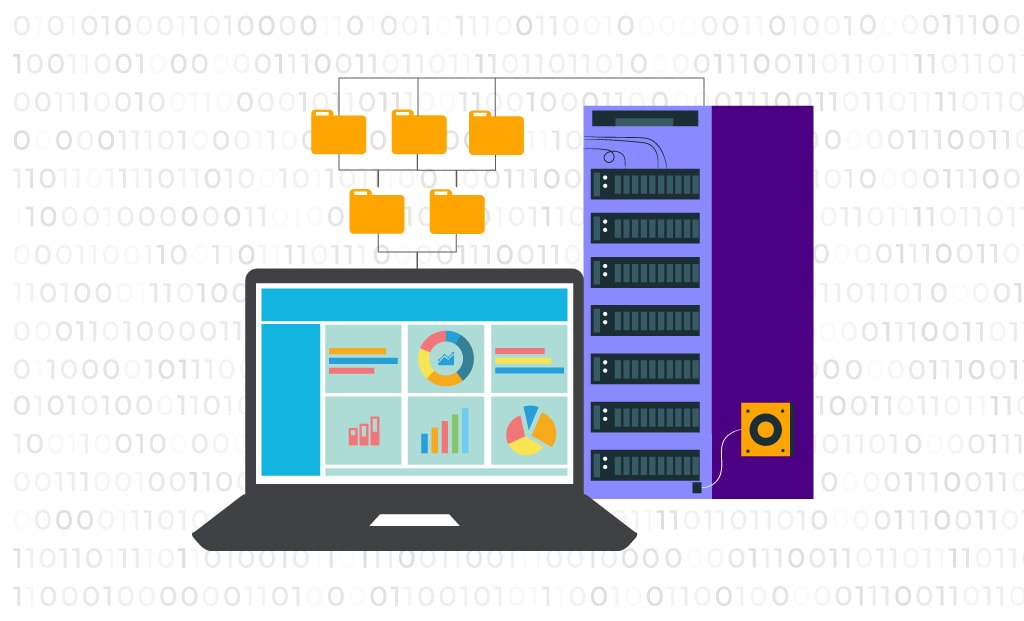
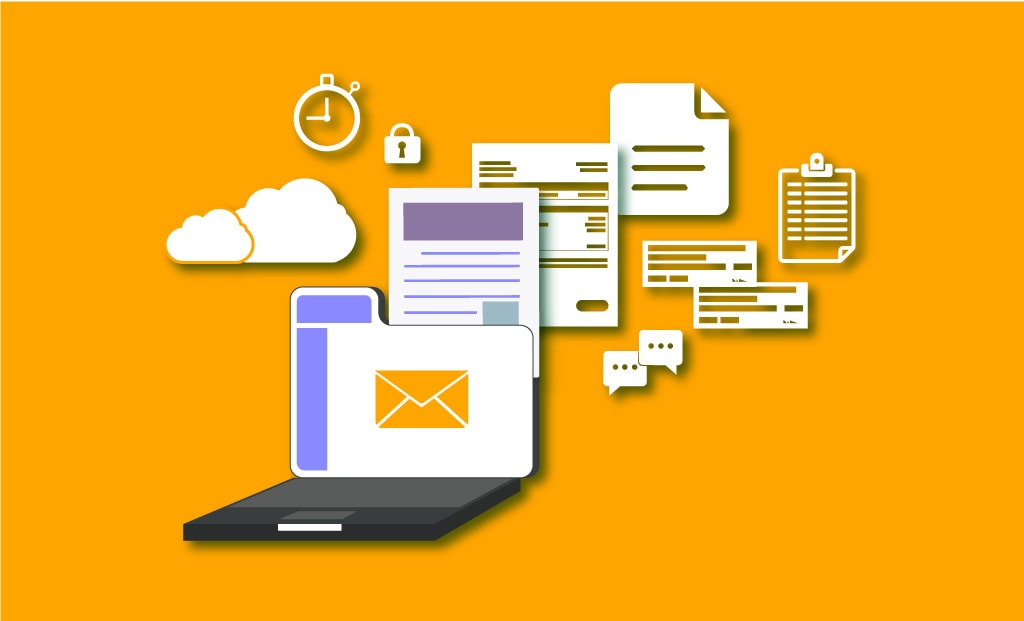
How can you Automate Document Distribution to Improve Enterprise Efficiency and Productivity?
FAQ
Sales Management in OmegaCube ERP automates and streamlines end-to-end sales workflows such as Order management, Quotation & Estimating, Customer Relationships, and billing. Through advanced capabilities such as CRM and EDI, sales management module helps manufacturers to improve customer response, order efficiency, and order tracking from order placement till customer shipment.
Order Management in OmegaCube ERP helps manufacturers to get a real-time view of their sales orders from various sources such as, website, e-commerce, cold calls, incoming enquiries etc. It automates order management workflows and helps them to improve customer response, service efficiency, supplier relationships and eliminate manual methods/paperwork.
Shop Floor Management in OmegaCube ERP helps manufacturers to get real-time view of their shop floor operations, track & improve resource utilization, improve yield quality, meet compliance standards, reduce machine breakdown/idle time and improve overall efficiency.