Lot Control & Management
Key Benefits of Lot Control & Management
- Trace movement of goods by assigning lot numbers to product groups.
- Streamline goods identification & movement by assigning SKU codes to each product.
- Improve inventory tracking and efficiency.
- Know product landing cost, fluctuating inventory cost and shelf life cost.
- Efficiently track bad product batches for instant product recall.
Key Features of Lot Control & Management
- Track lot-levels for perishable goods, harmful products, and commodities with expiration date.
- Issue own SKU codes specific to the product or services.
- Assign a unique lot number whenever inventory is created for an item that can be stocked.
- Material is received from a vendor through purchase receipt.
- Work order completion is done at the shop floor using a time card.
- Manual inventory is created.
- Nested layout completion is done through layout completion.
- New lot is created using material consumption/bar consumption.
- Opening inventory is loaded into the system.
- Configure lot number generation sequences using tools.
- View lot information by clicking on a lot number in any transaction page where lot is used.
- Get details on Items, Unit of Measurements, Cost data, lot transactions, location-wise balance, and dimensional item info.
- View lot hierarchy and how a lot is manufactured using different raw material/sub assembly lots.
- Attach mill certifications and Heat numbers to Lot and track them throughout the production process.
- View associated Work Order number against each lot number.
Our Customers are Our Purpose and Our Strength

We have been able to thin down our inventory carrying costs by about a third i.e. from approximately 3 million to 1 million. This is a huge deal for us. This was one of the prime reasons we needed an ERP, because we had inventory coming out of our ears, and we wanted to make sure that we had the right products at the right time.”

As soon as jobs are completed everyone knows an order is ready to ship. An email is sent via mobile devices so people throughout the facility are notified no matter where they are. When new jobs are created people can immediately check BOMs and inventory levels, so tools and materials can be ordered within minutes.”

We have to coordinate truckloads of steel, castings and other components from foreign suppliers, and PowerERP helps us balance, plan and schedule our ordering and inventory movements.”
Browse through our Latest ERP and Technological Insights
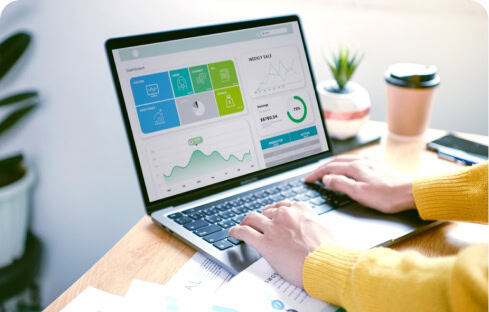
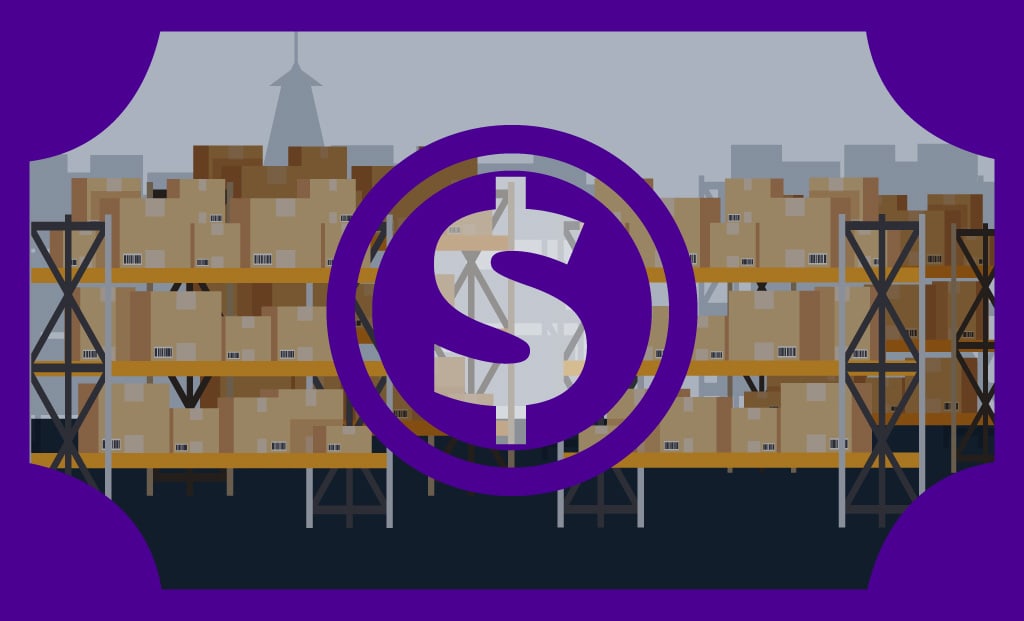
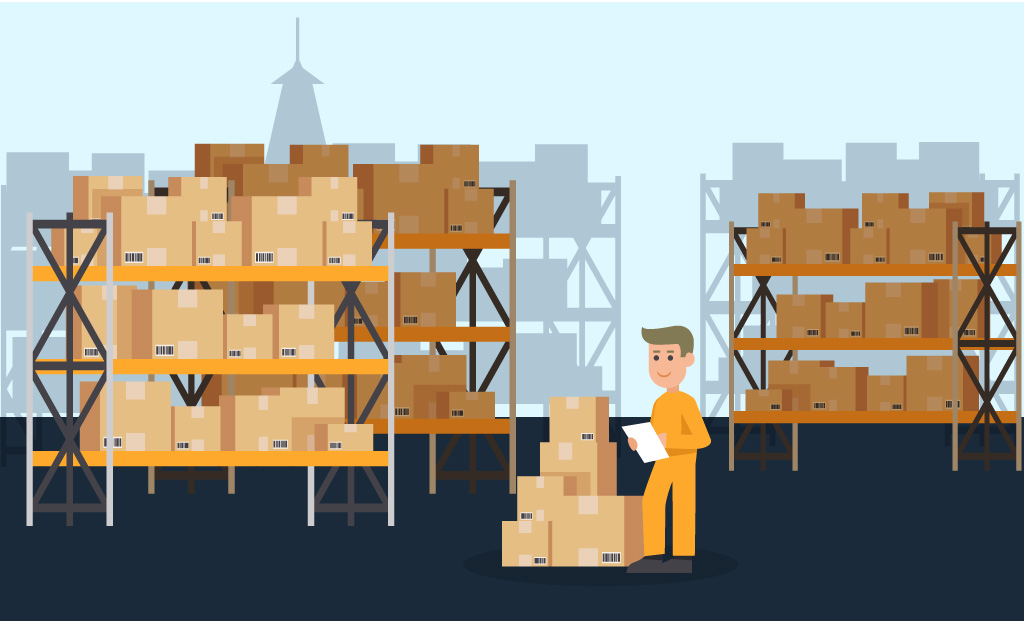
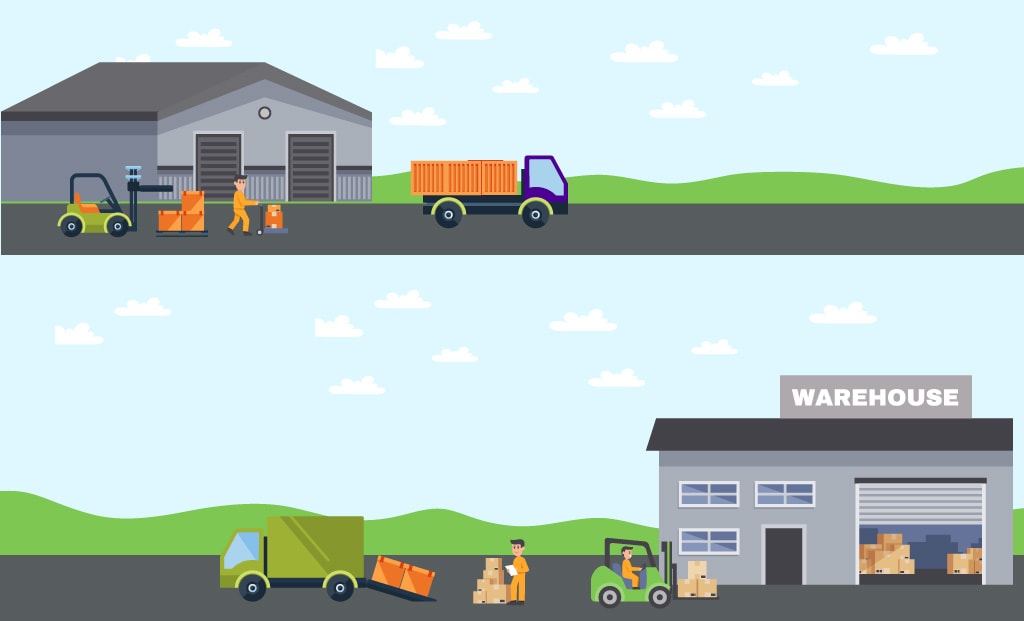
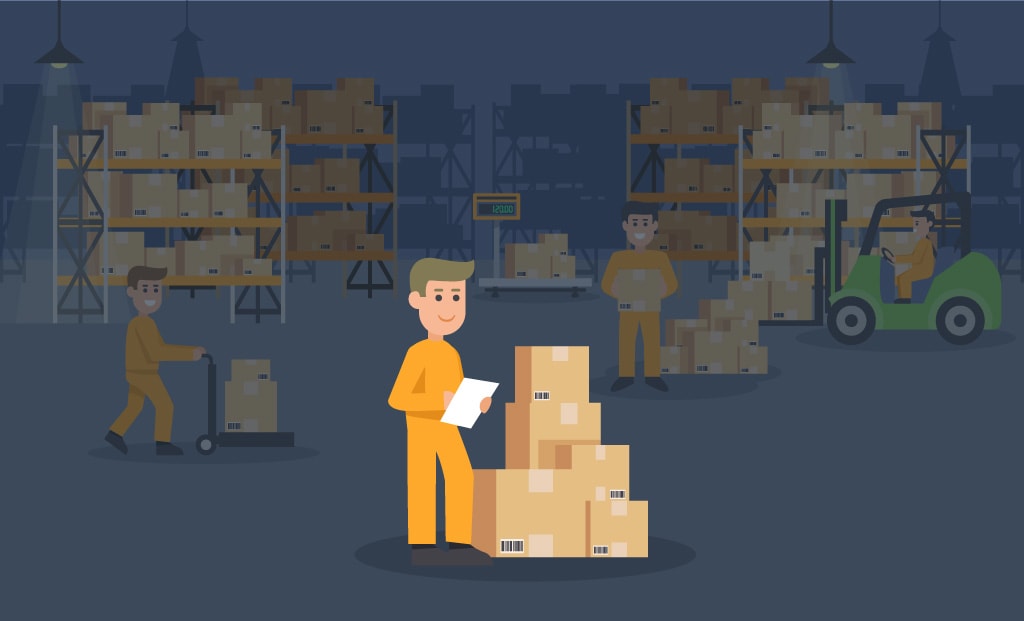
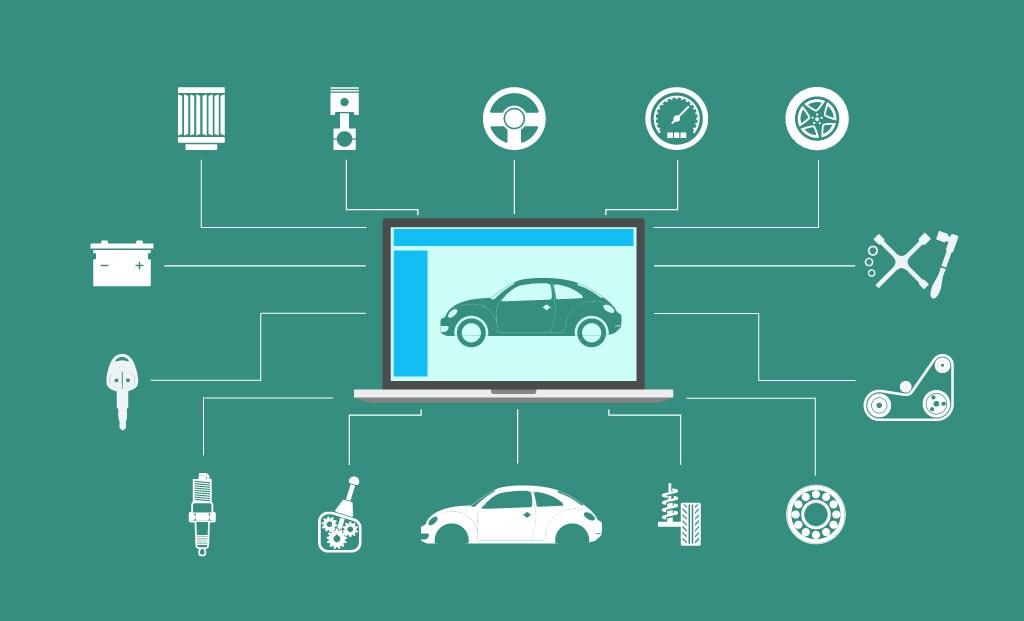
FAQ
Inventory Management in OmegaCube ERP enables manufacturing enterprises to efficiently plan, procure, build, manage and track inventory in real time. They can maintain optimum inventory levels, improve material traceability and cash flows by ordering the right materials at the right time for the right cost from the right supplier.
Shop Floor Management in OmegaCube ERP helps manufacturers to get real-time view of their shop floor operations, track & improve resource utilization, improve yield quality, meet compliance standards, reduce machine breakdown/idle time and improve overall efficiency.
OmegaCube ERP can be easily integrated with a host of manufacturing applications such as Nesting, CAD, E-commerce, Shipping & Logistics, Barcode & RFID, Machine Monitoring, Email etc. Manufacturers can completely automate inventory, design, planning, and shipping & production workflows with the help of advanced integration capability.