Equipment Maintenance
Key Features of Equipment Maintenance
- Increase operating life-span of machines, equipment, gages and tools.
- Minimize production disruption through reduction of equipment/machine failure during production.
- Reduce maintenance, repair and overhaul costs with effective cost tracking methods.
- Eliminate maintenance & repair scheduling issues, and minimize emergency and last minute repairs.
- Avoid cash-draining repairs for out-of-warranty equipment
Key Features of Equipment Maintenance
- Create and maintain machine/equipment information, and associated repair bill of materials.
- Create user-defined preventive maintenance plans (PM), repair procedures, check lists, spare parts list and link them to specific equipment.
- Automatically generate repair and maintenance work orders and dispatch to personnel.
- Allocate personnel and material inventory against the work order.
- Link drawings, instruction manuals and electronic documentation to equipment and PM plans.
- Link maintenance to scheduling and capacity planning.
- Trigger maintenance alerts and reminders based on equipment usage directly from shop floor data collection.
- Maintain comprehensive maintenance logs and repair history.
- Collect labor-time reported against maintenance work orders.
- Access maintenance work orders & create new ones from any mobile or tablet device.
Our Customers are Our Purpose and Our Strength

With OmegaCube ERP, we have expanded our production schedule by 7 times i.e., from one day to one week. Previously, the crew would know the scheduling only for the following day. However, with the ERP they know what to do for the entire week. They also have an approximate production schedule for the next 30 days but that keeps adjusting based on various factors.”

If I know how much capacity I have and I know my bookings I can decide on whether we can handle a particular order or if we need to buy another machine, subcontract the job or turn down the business. Before OmegaCube ERP, it was pretty much guesswork.”

OmegaCube has gone to a painstaking amount of work to make sure that we can instantaneously navigate to all the data we need. That applies to the front office as well as the shop floor, which means we’re saving time, doing more work and cutting costs throughout the operation – without sacrificing quality or delivery.”
Browse through our Latest ERP and Technological Insights
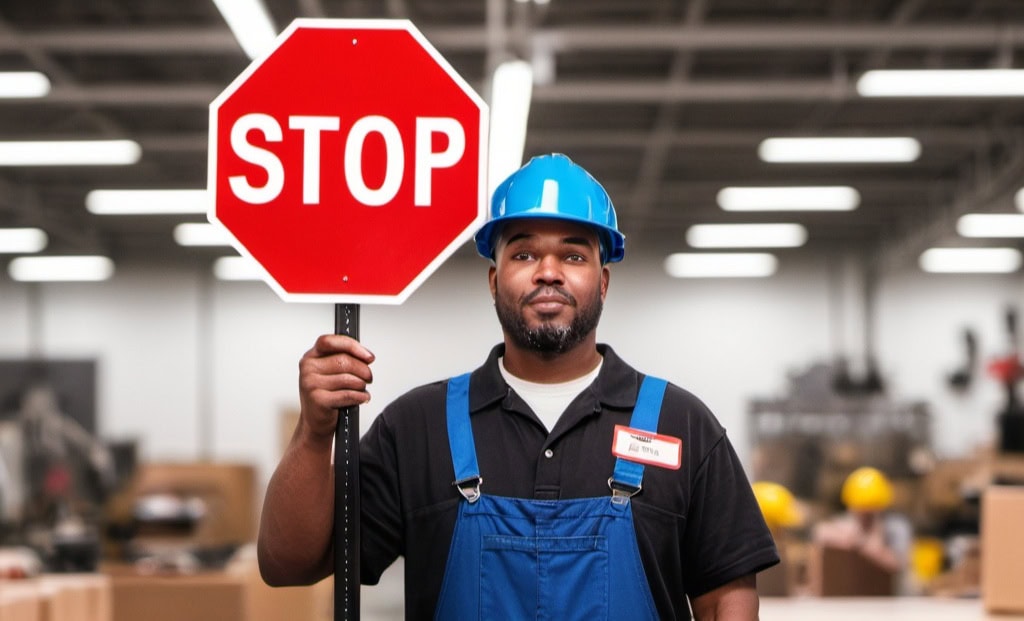
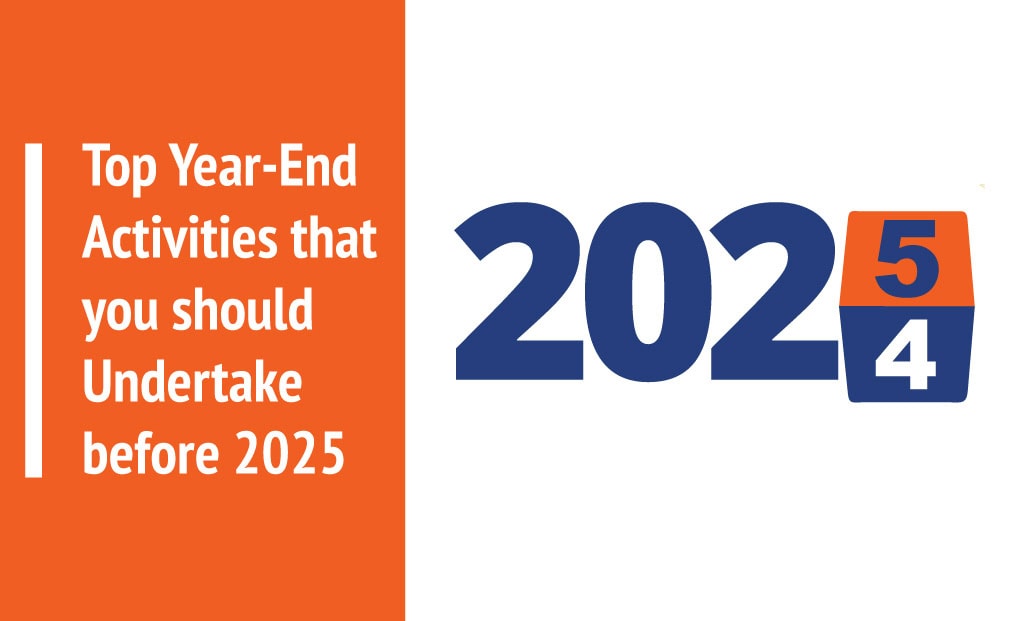
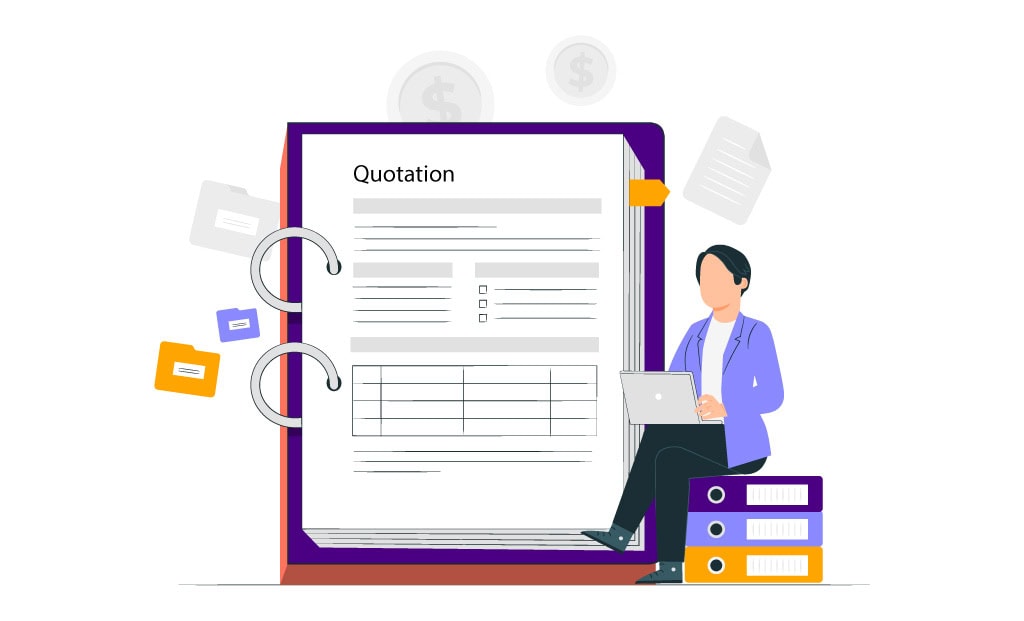
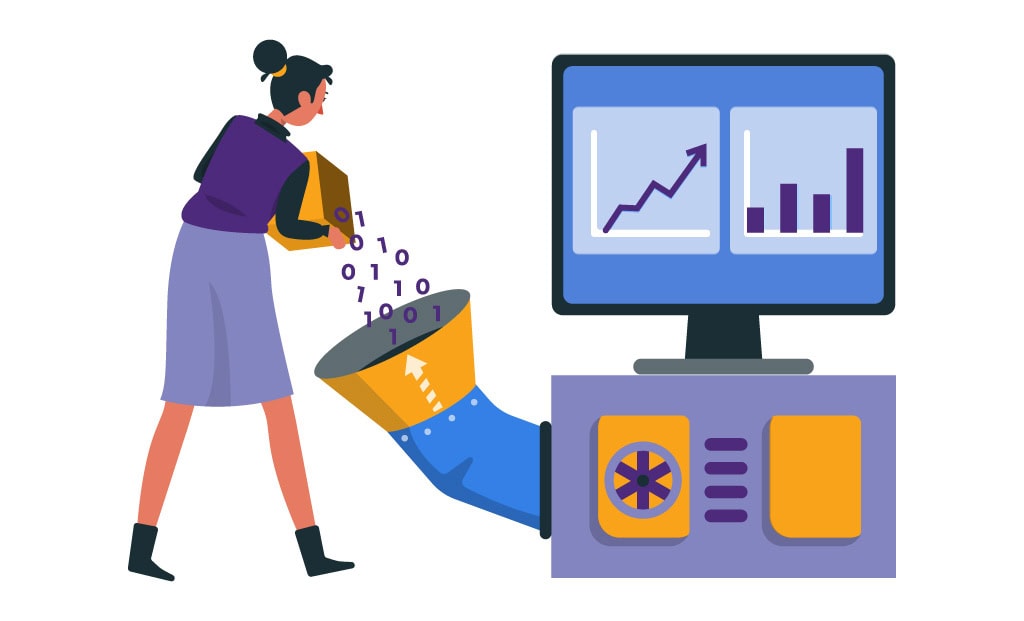
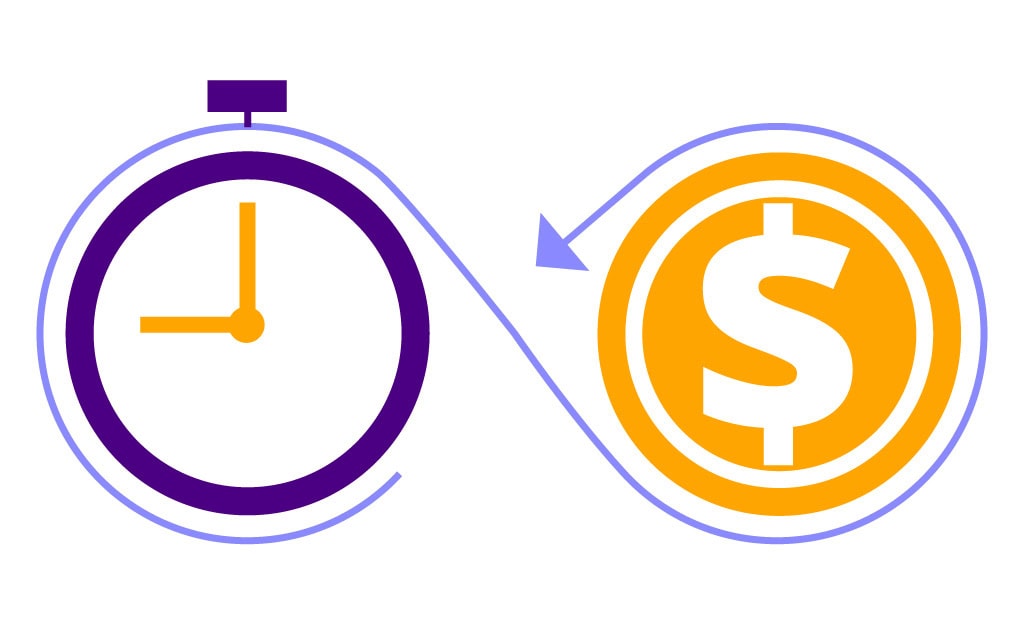
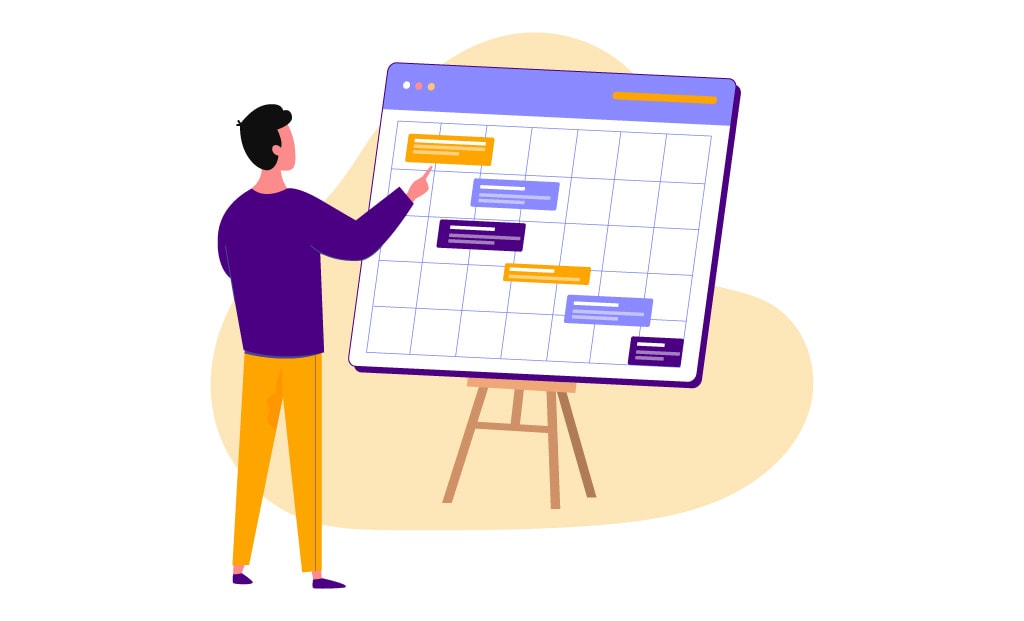
FAQ
Shop Floor Management in OmegaCube ERP helps manufacturers to get real-time view of their shop floor operations, track & improve resource utilization, improve yield quality, meet compliance standards, reduce machine breakdown/idle time and improve overall efficiency.
OmegaCube ERP can be integrated with CAD Applications such as, AutoCAD and SolidWorks. This lets manufacturers combine manufacturing and design workflows, save overall engineering time, costs and avoid production delays.
Planning and Scheduling in OmegaCube ERP automates production planning and scheduling workflows by taking material, manpower and machine availability into consideration. It improves capacity utilization during production, operator productivity, optimum supply chain planning, and on-time delivery to customers.