Gage Calibration
Key Benefits of Gage Calibration Management
- Optimize quality controls with gage calibration and management.
- Ensure correct gage and quality of tools.
- Prevent losses arising out of incorrect or out of calibration tools.
- Maintain working condition of gages through efficient tracking.
- Prevent auditing and liability issues by maintaining comprehensive documentation.
Key Benefits of Gage Calibration Management
- Create Gage master record and enter NIST number, Serial number, calibration frequency and procedure.
- Issue gages to the production floor with or without work order numbers.
- Issue single or multiple gages against a work order.
- Access gage report to check gages that can be issued.
- Return gages back from production after successful completion of work orders.
- Return single or bulk gages.
- Set gage calibration schedule in the gage master.
- Get system alerts for gages that need calibration based on set criteria.
- Auto-update of calibration date in the gage master.
- Access Gage Issue & calibration history, pending gage return by WO, upcoming calibrations, and next gage calibration list.
Our Customers are Our Purpose and Our Strength

With OmegaCube ERP, we have expanded our production schedule by 7 times i.e., from one day to one week. Previously, the crew would know the scheduling only for the following day. However, with the ERP they know what to do for the entire week. They also have an approximate production schedule for the next 30 days but that keeps adjusting based on various factors.”

If I know how much capacity I have and I know my bookings I can decide on whether we can handle a particular order or if we need to buy another machine, subcontract the job or turn down the business. Before OmegaCube ERP, it was pretty much guesswork.”

OmegaCube has gone to a painstaking amount of work to make sure that we can instantaneously navigate to all the data we need. That applies to the front office as well as the shop floor, which means we’re saving time, doing more work and cutting costs throughout the operation – without sacrificing quality or delivery.”
Browse through our Latest ERP and Technological Insights
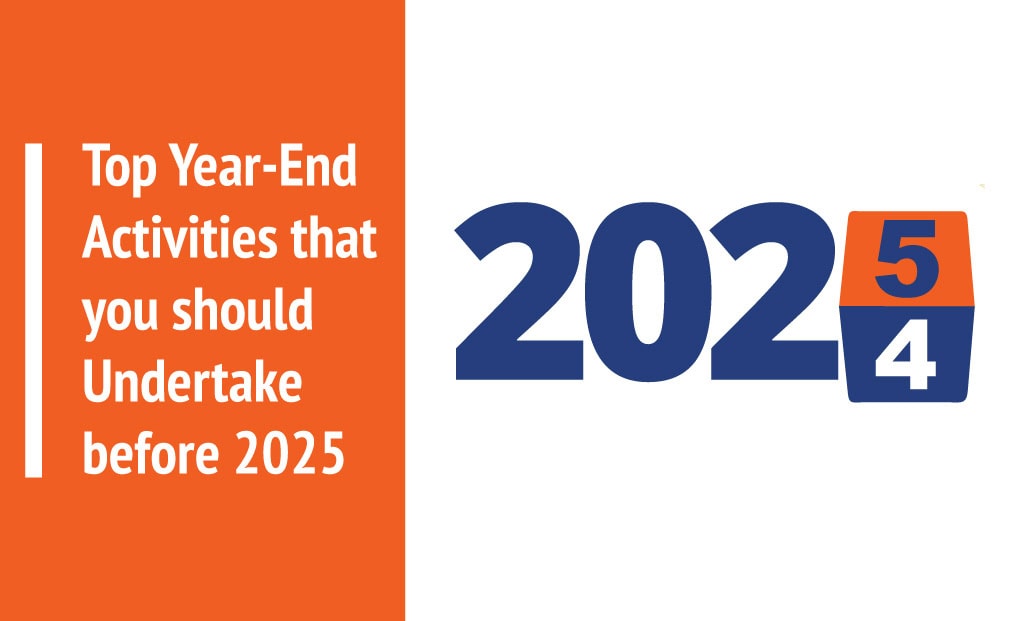
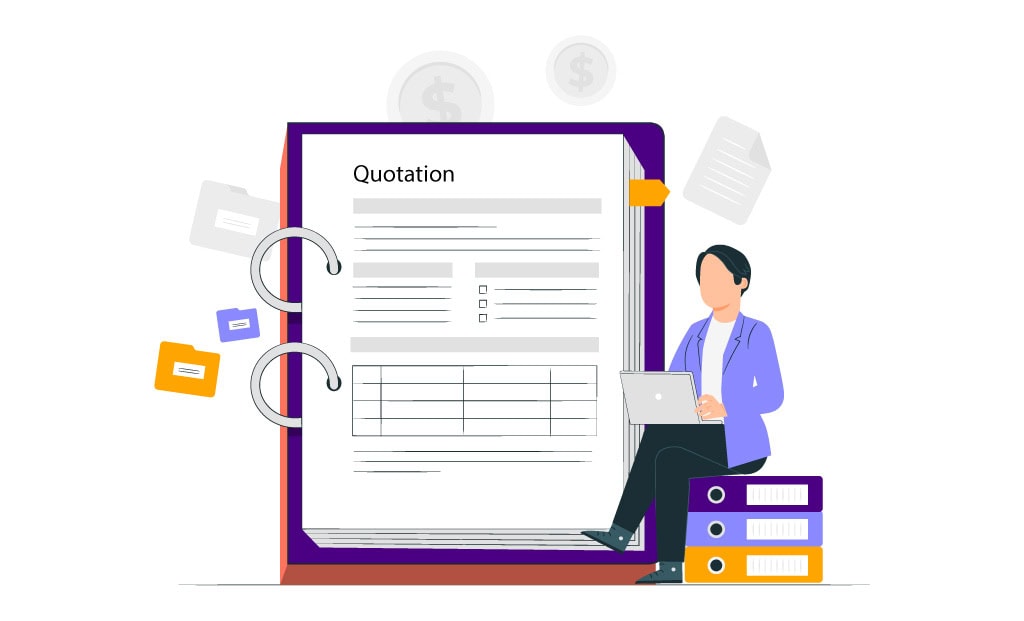
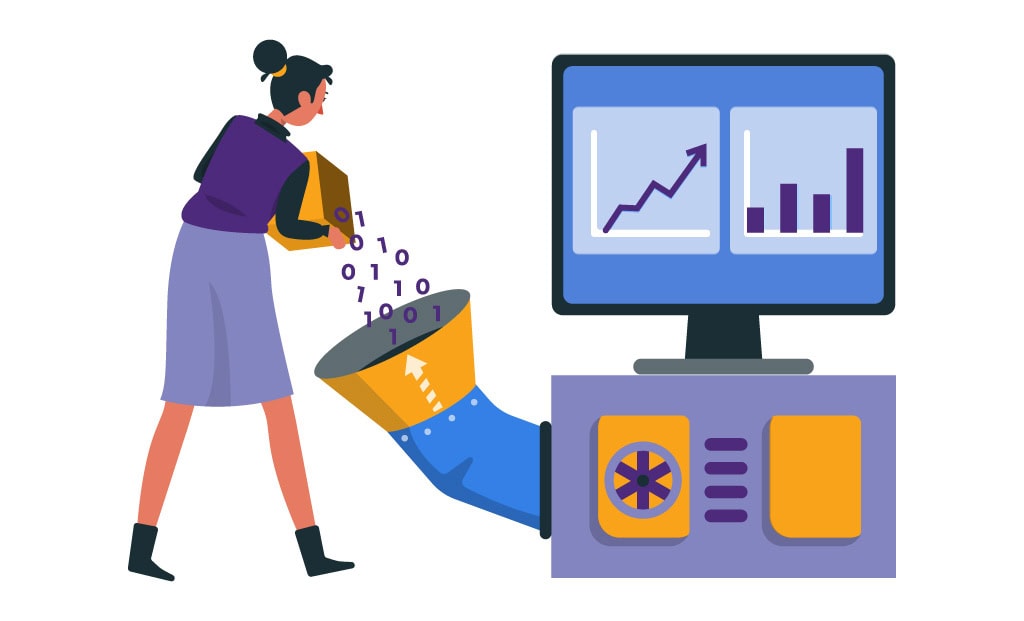
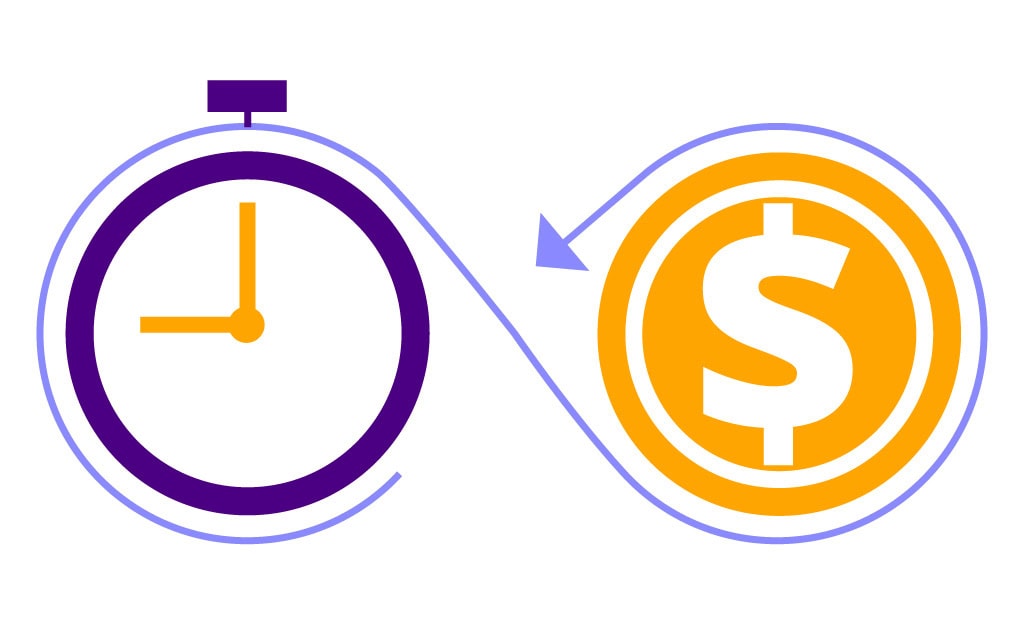
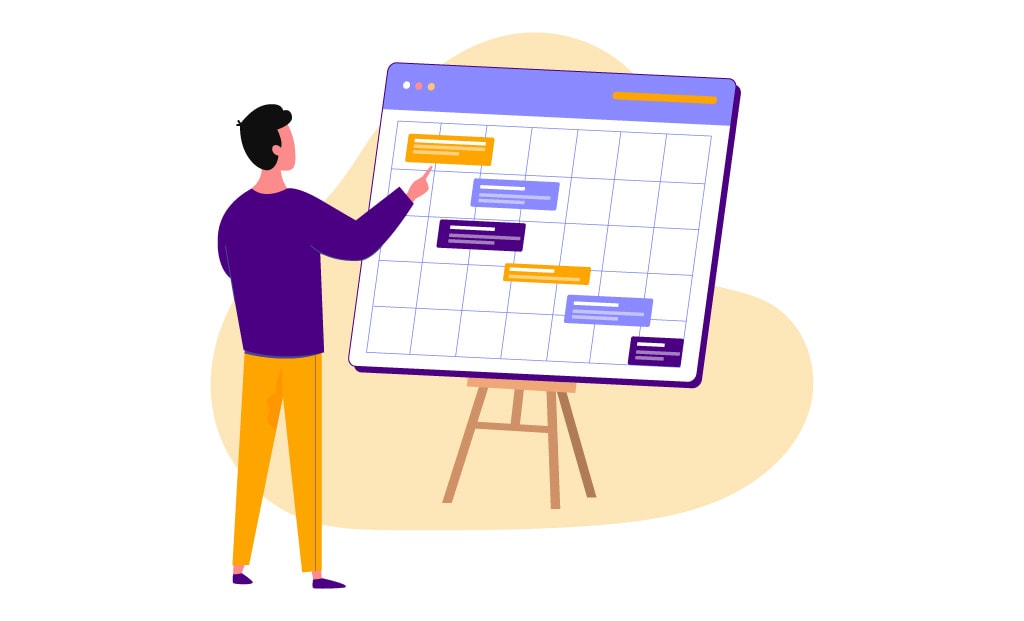
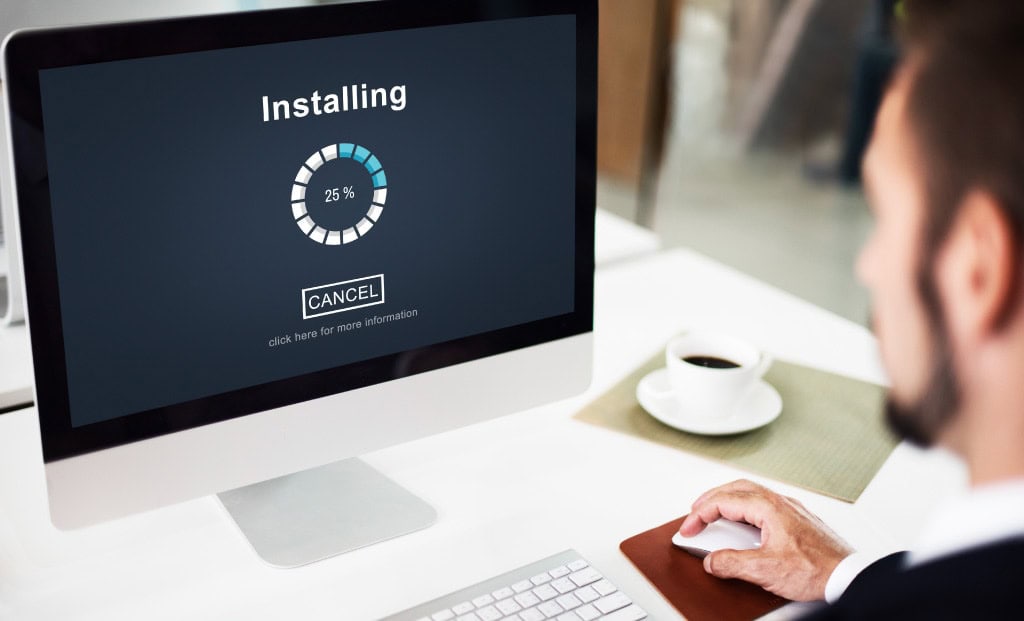
FAQ
Tool and Fixture Management in OmegaCube ERP helps manufacturers to efficiently track and maintain machine tool equipment, tool sets, utilities, and spare parts. Maintenance/repair schedules can be easily created based on the production schedule to ensure continuous availability of tools during production.
Quality Management in OmegaCube ERP enables manufacturing and distribution enterprises to track, manage and document quality parameters at each step of operations. With its tightly knit integration with other modules, enterprises can easily comply to industry standards and quality regulations.
Work Order Management in OmegaCube ERP helps manufacturers to accurately schedule work orders, prioritize based on customer requirement and dispatch them to the shop floor. They can track work order progress throughout the production process, combine work orders and increase overall manufacturing efficiency.