Tool and Fixture Management
Key Benefits of Tool and Fixture Management
- Comprehensive planning to procurement visibility of tools, gages, dies and fixtures.
- Reduce repair & maintenance costs by continuously tracking tool assets, planning repair/maintenance schedule well in advance.
- Reduce procurement costs by ordering tools from approved suppliers on time.
- Prevent production disruption due to tool breakdowns and failures.
Key Features of Tool and Fixture Management
- Maintain a master list of tools, tool sets, dies, and fixtures.
- Specify Items that utilize the tool during manufacturing.
- Specify tool information in routings and work orders.
- Define tool maintenance schedules or usage based automatic maintenance.
- Automatically generate alerts when tool maintenance is due.
- Maintain detailed logs of tool procurement, repair and maintenance.
- Utilize tool issue/returns to specify what parts where made when using a specific tool or die.
- Maintain detailed digital documentation of tool and fixture usage, SOPs, safety instructions etc.
Our Customers are Our Purpose and Our Strength

As soon as jobs are completed everyone knows an order is ready to ship. An email is sent via mobile devices so people throughout the facility are notified no matter where they are. When new jobs are created people can immediately check BOMs and inventory levels, so tools and materials can be ordered within minutes.”

We have everything running through OmegaCube and people across all disciplines interact with the system. If we want to know anything about production, sales, a particular job, maintenance on a job or raw material costs on a job we only have to go to one place to look for it. That’s powerful.”

This was March 2020 and then COVID-19 hit. If we were still using the old FoxPro system and the manual way of operating, I don’t think we could have had everybody go home and work remotely.
With OmegaCube ERP, we were able to work remotely and still operate during the pandemic. Even though we just completed setting up our initial ERP system, our employees were able to run with it while working remotely and that ended up working out great. The system operated efficiently for sales, engineering, and purchasing.
I don’t think we could have done that with the old FoxPro system as we did with OmegaCube ERP. So the timing of implementing OmegaCube ERP was perfect.
Browse through our Latest ERP and Technological Insights
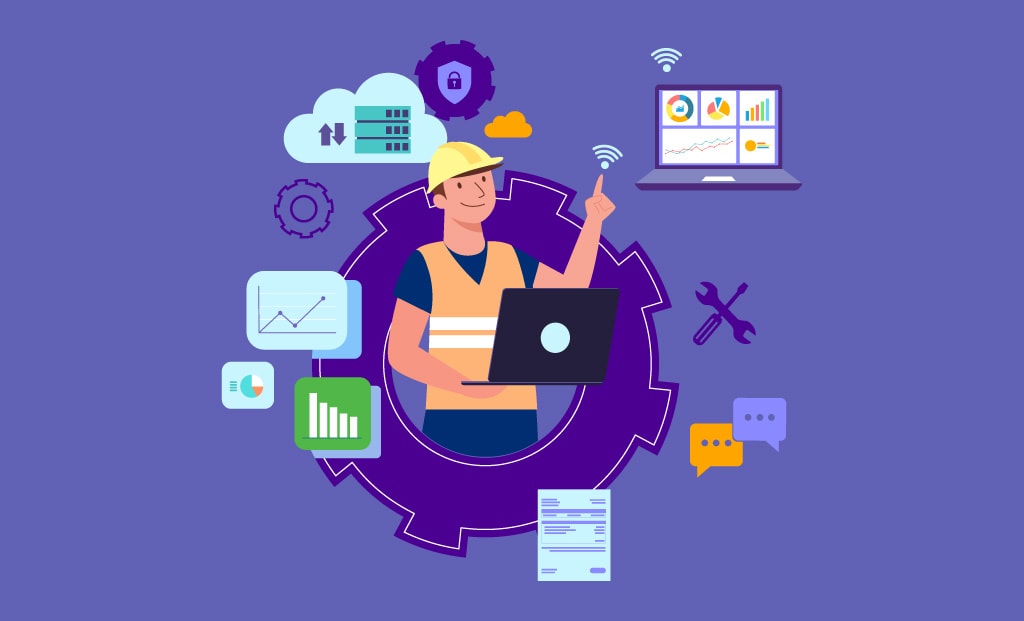
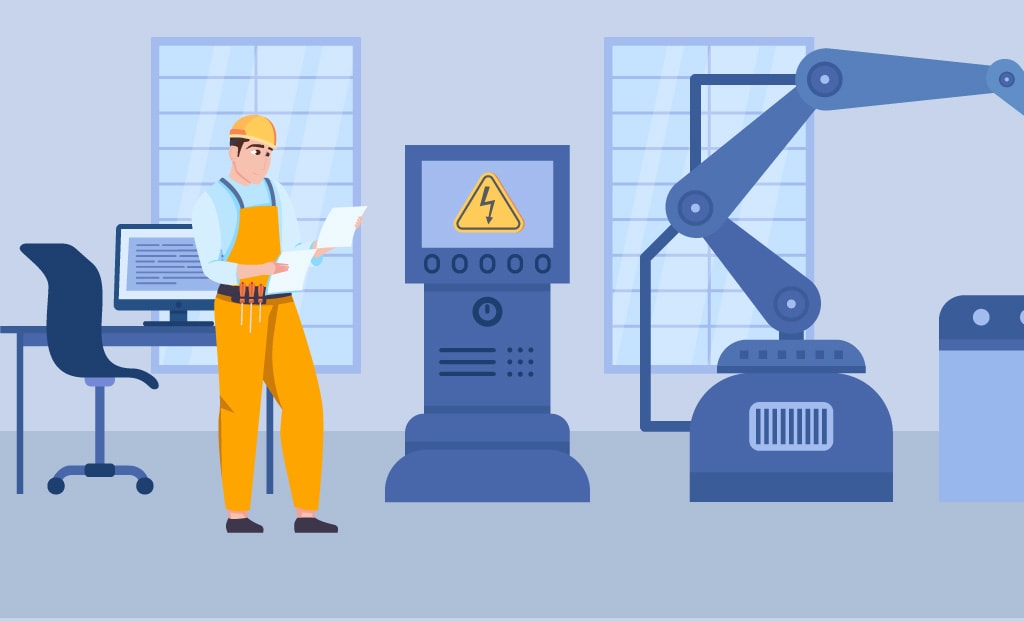
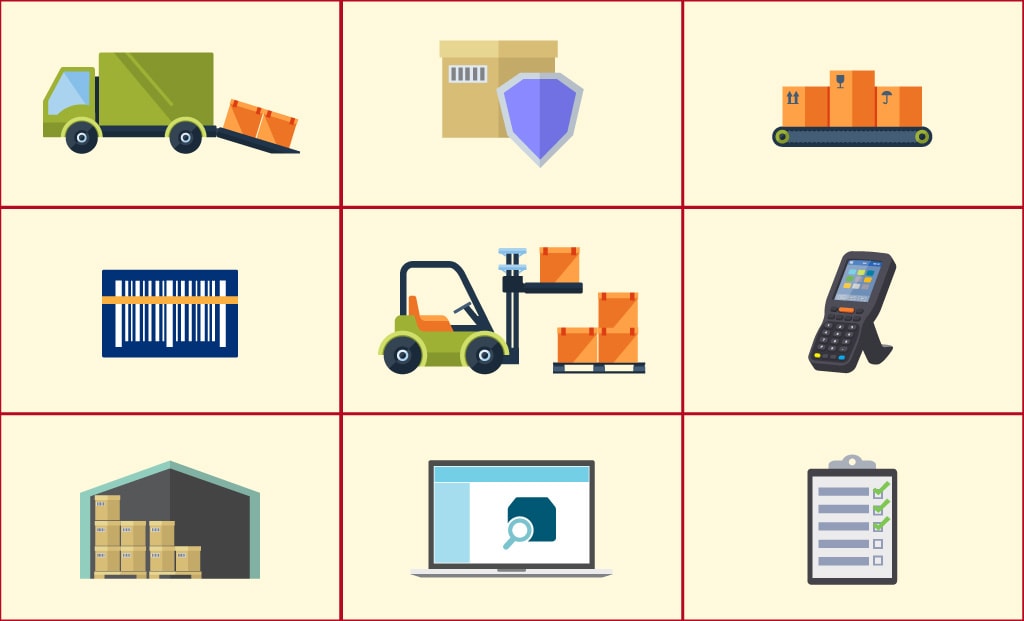
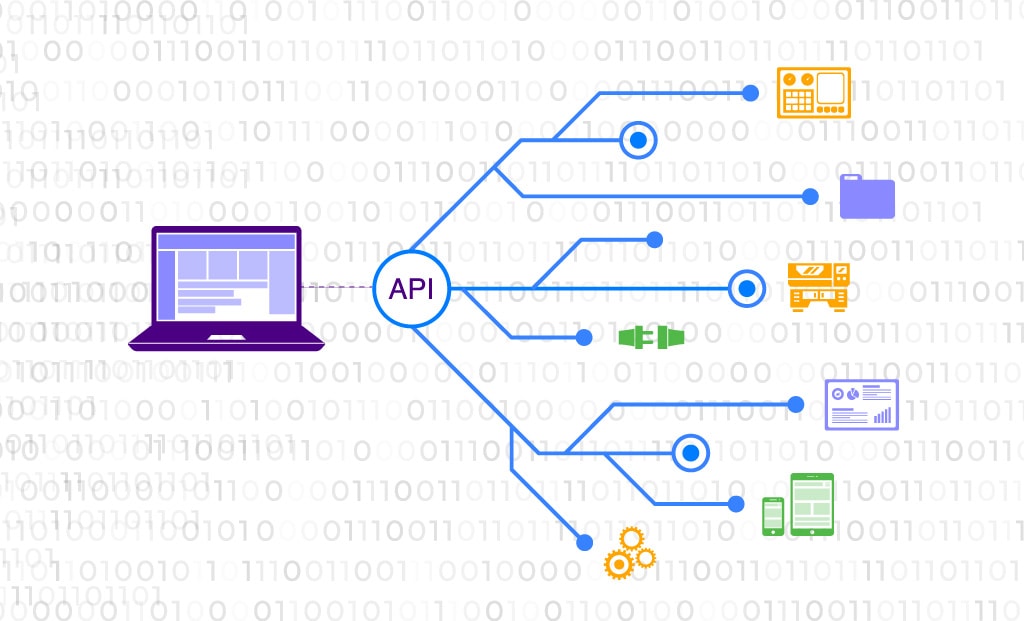
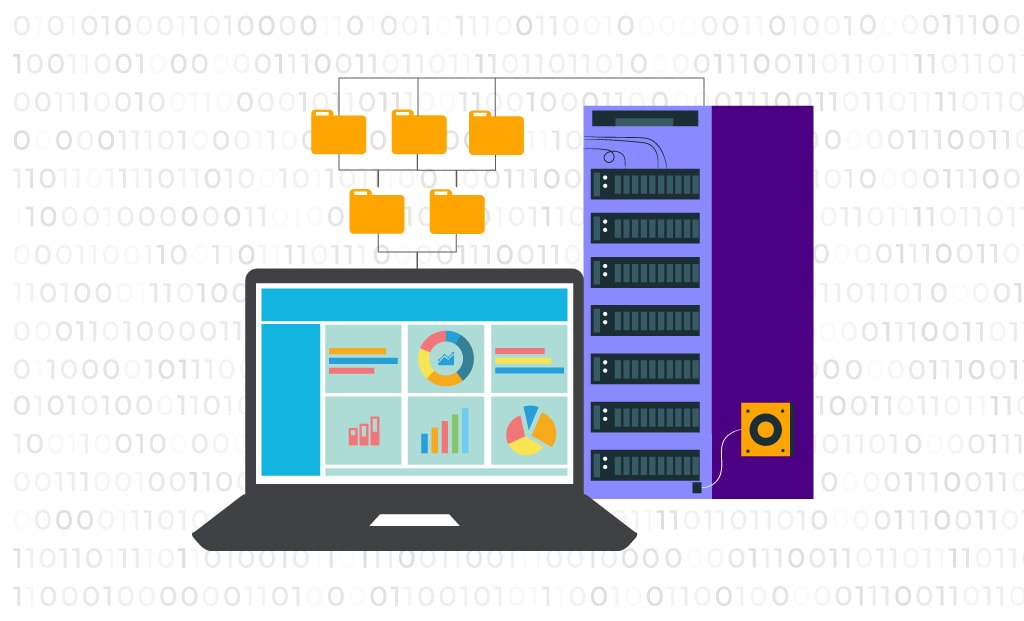
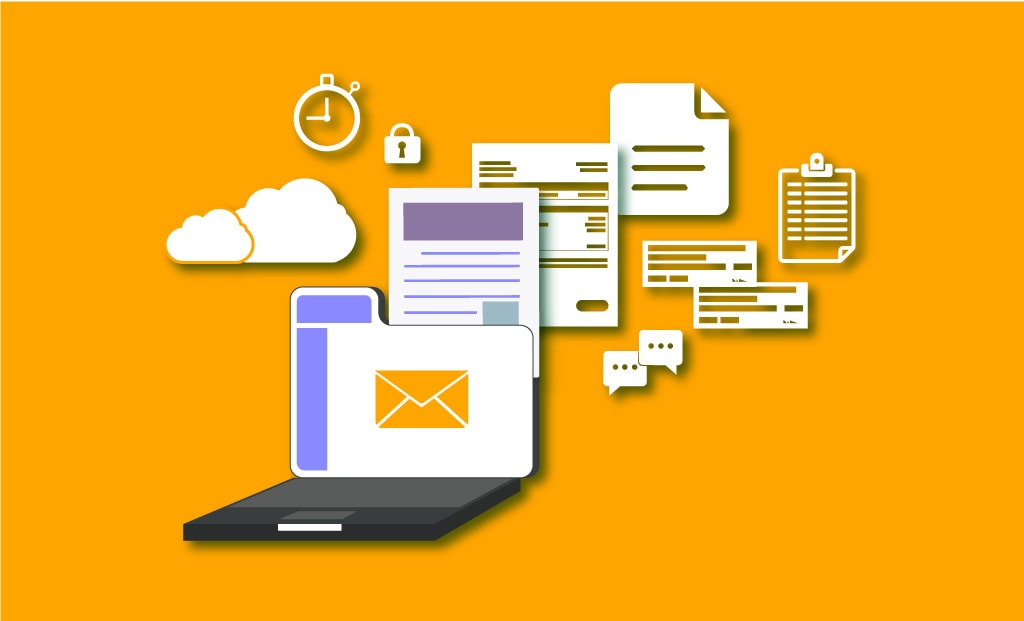
How can you Automate Document Distribution to Improve Enterprise Efficiency and Productivity?
FAQ Headline goes here
Shop Floor Management in OmegaCube ERP helps manufacturers to get real-time view of their shop floor operations, track & improve resource utilization, improve yield quality, meet compliance standards, reduce machine breakdown/idle time and improve overall efficiency.
Equipment Maintenance in OmegaCube ERP helps manufacturers to keep a steady track of maintenance planning and schedule of manufacturing equipment and machines. It helps them prevent maintenance-related breakdowns and potential production delays.