Workflow Automation
OmegaCube ERP’s Workflow Automation features enable you to cut critical production time, improve personnel and operational efficiency, reduce costs and eliminate manual operating methods.
Through tight integration with manufacturing, shipping, and communication applications, you can digitize entire workflows and reduce order-to-cash cycles.
Key Benefits of Workflow Automation
- Push-based workflow automation for business efficiency.
- Improves collaboration between team members, intra-teams, departments and branches.
- Reduce paper-usage, storage, postage, archive retrieval, procurement etc.
- Speed up business cycles due to quick flow of information to customers and partners.
- Improve data quality due to elimination of data entry errors, loss of documents etc.
- Reduce waiting time, order-to-cash cycles owing to real-time visibility to data.
- Reduce purchasing costs by automating procurement workflow.
- Reduce reliance on spreadsheets and rely on workflow automation for financial transactions.
Key Features of Workflow Automation
- Configure workflows as per your manufacturing and business processes.
- Alerts, actions and reports link to specific steps on the workflow.
- Subscription based access to events and alerts for workflow automation.
- Send automated reminders to purchase managers & suppliers to delay or expedite shipments based on certain pre-defined rules.
- Auto-initiate material procurement by raising a Purchase Order (PO) or Request for Quotation (RFQ) with designated suppliers.
- Set up personnel reminders and custom notifications for personnel.
- Manage support & service departments using a workflow based approach.
- Email integration for a seamless email workflow.
- Exchange critical information with your suppliers and third-party vendors in real-time through EDI.
- Automate shipping workflows for global and local shipping operations through integration with shipping applications.
- Automate Purchase Order workflow by using approvals based on roles and spending limits
- Automatically create work orders from Sales Orders, MRP, Quality repairs, and Kanban.
- Automatically update dispatch list after scheduling run.
- Automate tracking of incoming raw materials, and inventory movement through bar code and RFID integration.
- Automate entire parts cutting operation right from work order dispatch to cutting stage through nesting integration.
Our Customers are Our Purpose and Our Strength

We have everything running through OmegaCube and people across all disciplines interact with the system. If we want to know anything about production, sales, a particular job, maintenance on a job or raw material costs on a job we only have to go to one place to look for it. That’s powerful.”

Well, I can just say that it’s impossible to make a mistake now. The close-knit process within OmegaCube ERP ensures that almost no mistake can be committed.
For example, a purchase order lines up with a purchase receipt, and you can’t enter an invoice without a purchase receipt. In the ERP, you cannot duplicate the purchase receipt because it’s tagged to this purchase order. Therefore, the system makes it entirely difficult to make any sort of mistakes of course, unknowingly.

This was March 2020 and then COVID-19 hit. If we were still using the old FoxPro system and the manual way of operating, I don’t think we could have had everybody go home and work remotely.
With OmegaCube ERP, we were able to work remotely and still operate during the pandemic. Even though we just completed setting up our initial ERP system, our employees were able to run with it while working remotely and that ended up working out great. The system operated efficiently for sales, engineering, and purchasing.
I don’t think we could have done that with the old FoxPro system as we did with OmegaCube ERP. So the timing of implementing OmegaCube ERP was perfect.
Browse through our Latest ERP and Technological Insights
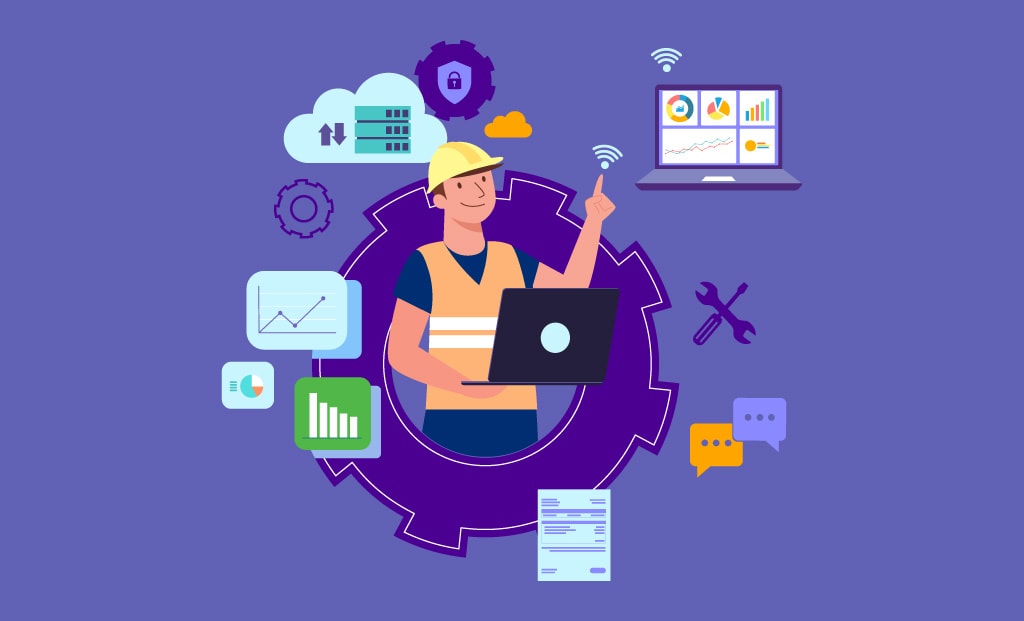
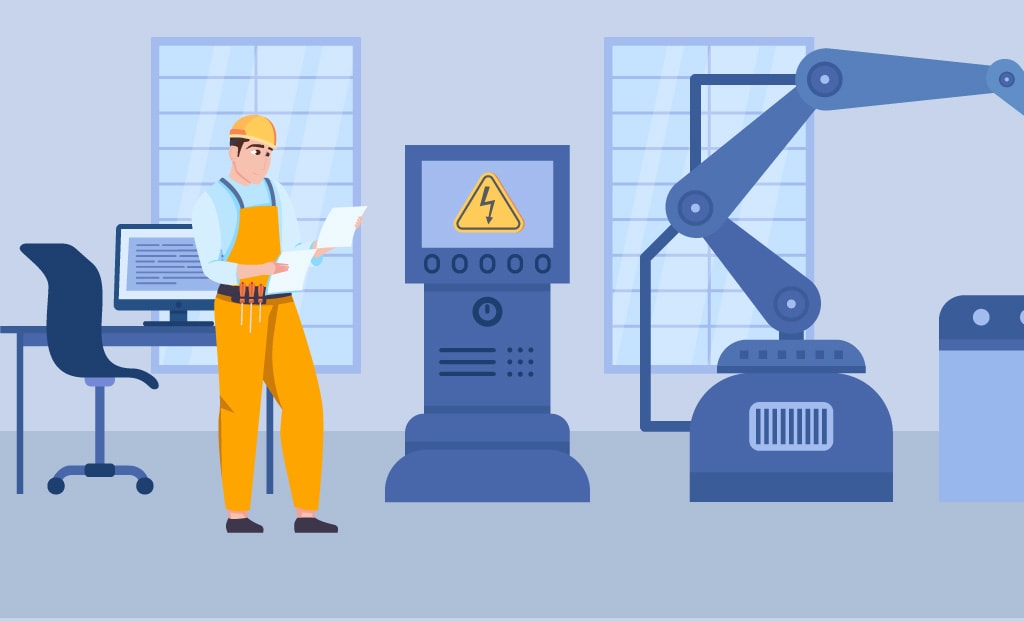
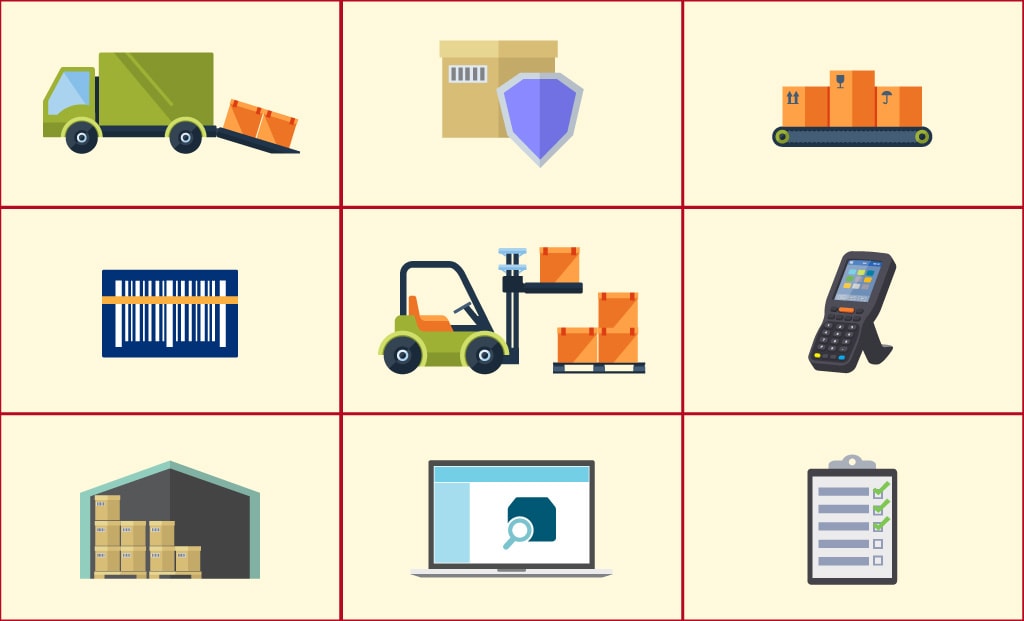
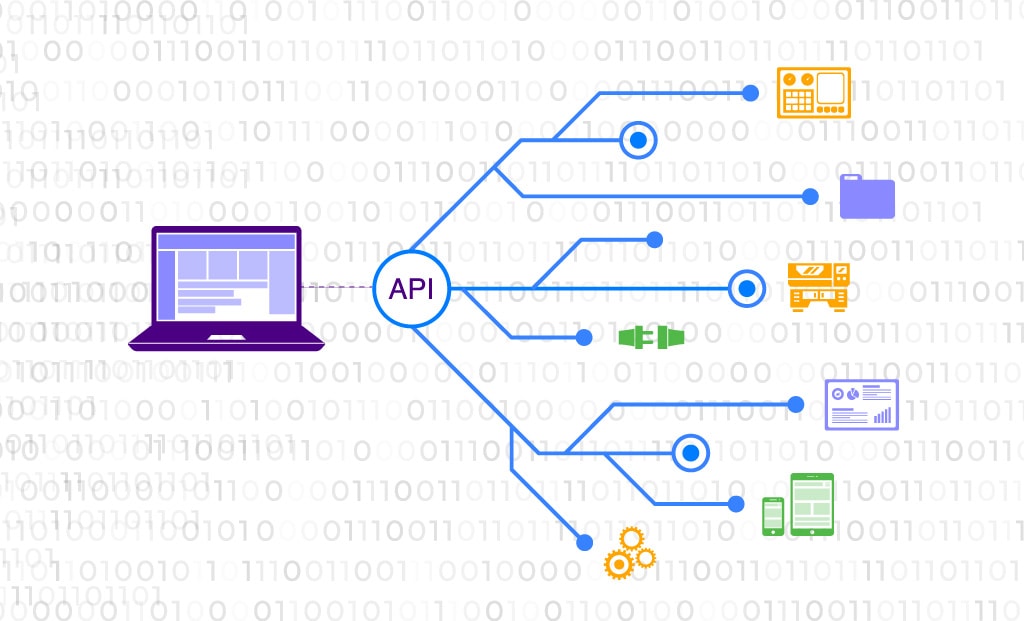
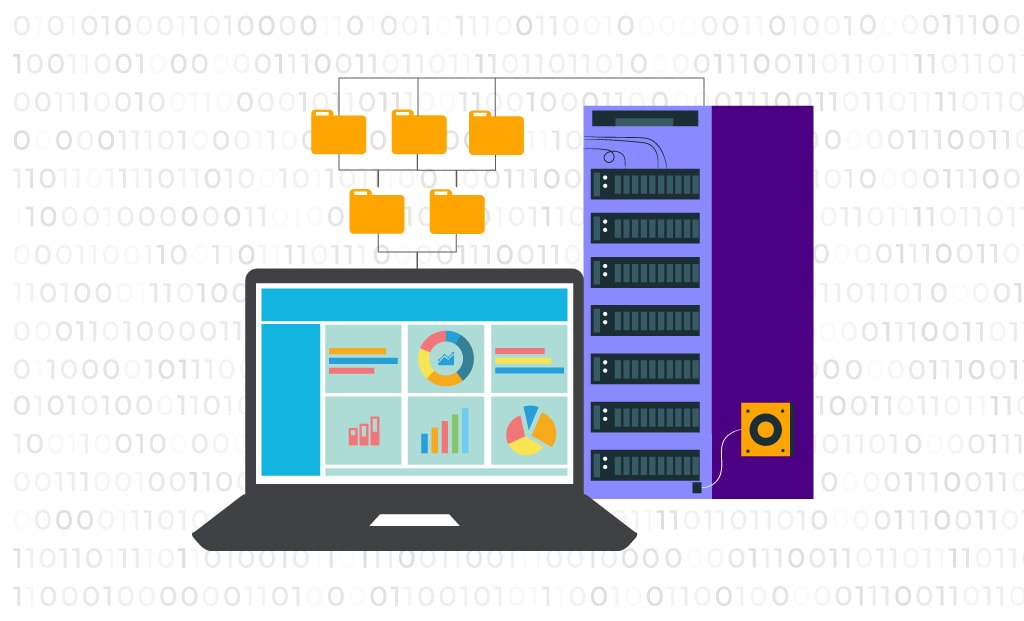
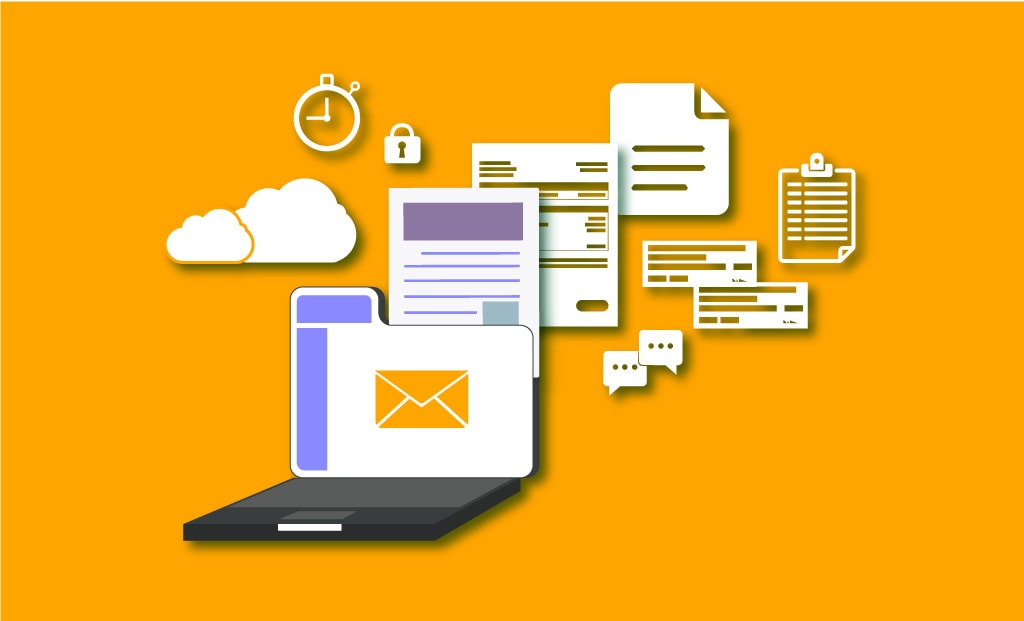