- OmegaCube Technologies
- Product
- Suppliers and Purchasing
Suppliers and Purchasing
Key Benefits of Purchase Management
Key Features of Purchase Management
- Create and maintain purchase order including blankets, and outside assembly purchases
- Create Pos or blanket releases from MRP
- Apply correct pricing from pricing files or last purchase data
- Automate workflow by using approvals based on roles and spending limits
- Email PO directly from ERP
- Utilize MRP output to determine purchasing requirements
- Create or add to existing purchase orders from MRP
- Automatically compute and use Lot sizes for purchasing
- Consolidate purchases into one PO per vendor to reduce paperwork
- Create blanket releases from MRP
- Maintain detailed vendor data including ratings and approval
- Gain insights from comprehensive metrics on supplier performance
- Review supplier quality, on-time performance by various parameters like Item numbers, Item Type, and Vendor
- Publish performance and dashboard data to users based on roles
- Create purchase orders for work in process inventory
- Create shipping documents
- Track outside inventory and publish vendor inventory on dispatch list and work order status reporting
- Define and use vendor and part lead times and utilize actual lead times in scheduling
- Track quality on outside service receiving
- Manage returns and AP process for outside service purchases
- Receive goods and outside service purchases
- Perform quality inspections and manage returns process efficiently
- Automatically generate AP invoices
- Generate bar coded labels and receiving documents
- Receive inventory based on lot or serial number
- Receive using mobile devices
- Create AP automatically from receiving
- Create credit memo from returns
- Track accrued purchased and pending bills
- Track variances in purchase price and AP price
- Create and maintain purchase order including blankets, and outside assembly purchases
- Create Pos or blanket releases from MRP
- Apply correct pricing from pricing files or last purchase data
- Automate workflow by using approvals based on roles and spending limits
- Email PO directly from ERP
- Utilize MRP output to determine purchasing requirements
- Create or add to existing purchase orders from MRP
- Automatically compute and use Lot sizes for purchasing
- Consolidate purchases into one PO per vendor to reduce paperwork
- Create blanket releases from MRP
- Maintain detailed vendor data including ratings and approval
- Gain insights from comprehensive metrics on supplier performance
- Review supplier quality, on-time performance by various parameters like Item numbers, Item Type, and Vendor
- Publish performance and dashboard data to users based on roles
- Create purchase orders for work in process inventory
- Create shipping documents
- Track outside inventory and publish vendor inventory on dispatch list and work order status reporting
- Define and use vendor and part lead times and utilize actual lead times in scheduling
- Track quality on outside service receiving
- Manage returns and AP process for outside service purchases
- Receive goods and outside service purchases
- Perform quality inspections and manage returns process efficiently
- Automatically generate AP invoices
- Generate bar coded labels and receiving documents
- Receive inventory based on lot or serial number
- Receive using mobile devices
- Create AP automatically from receiving
- Create credit memo from returns
- Track accrued purchased and pending bills
- Track variances in purchase price and AP price
Our Customers are Our Purpose and Our Strength

Well, I can just say that it’s impossible to make a mistake now. The close-knit process within OmegaCube ERP ensures that almost no mistake can be committed.
For example, a purchase order lines up with a purchase receipt, and you can’t enter an invoice without a purchase receipt. In the ERP, you cannot duplicate the purchase receipt because it’s tagged to this purchase order. Therefore, the system makes it entirely difficult to make any sort of mistakes of course, unknowingly.

We have to coordinate truckloads of steel, castings and other components from foreign suppliers, and PowerERP helps us balance, plan and schedule our ordering and inventory movements.”

Our customers want a supplier that can be responsive to their requirements, that can give them an accurate picture of what can be accomplished. OmegaCube lets us do that.”
Browse through our Latest ERP and Technological Insights
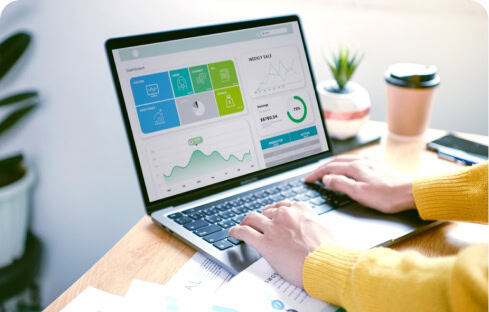
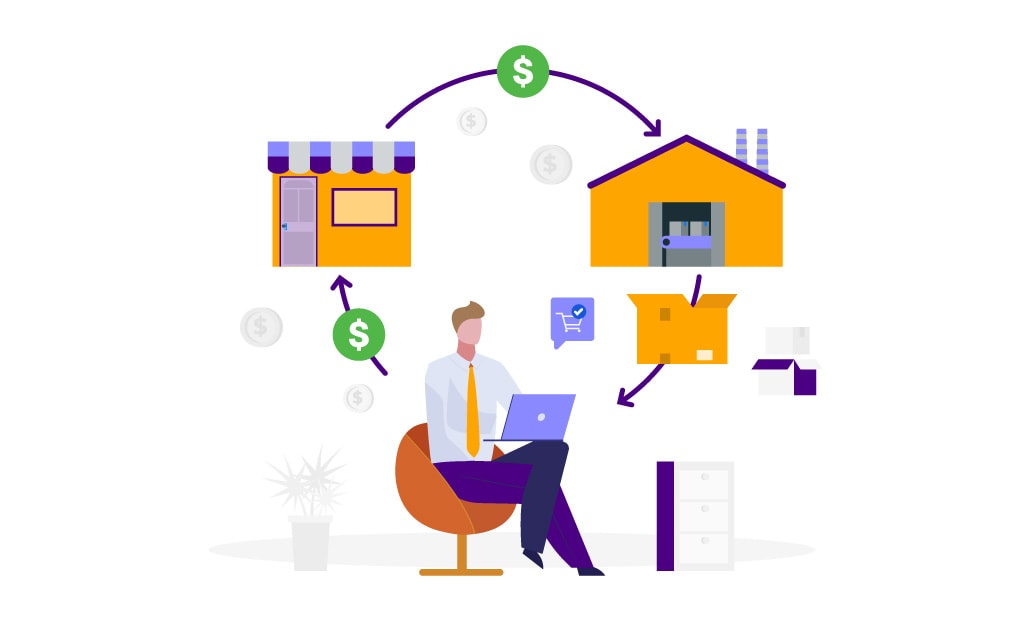
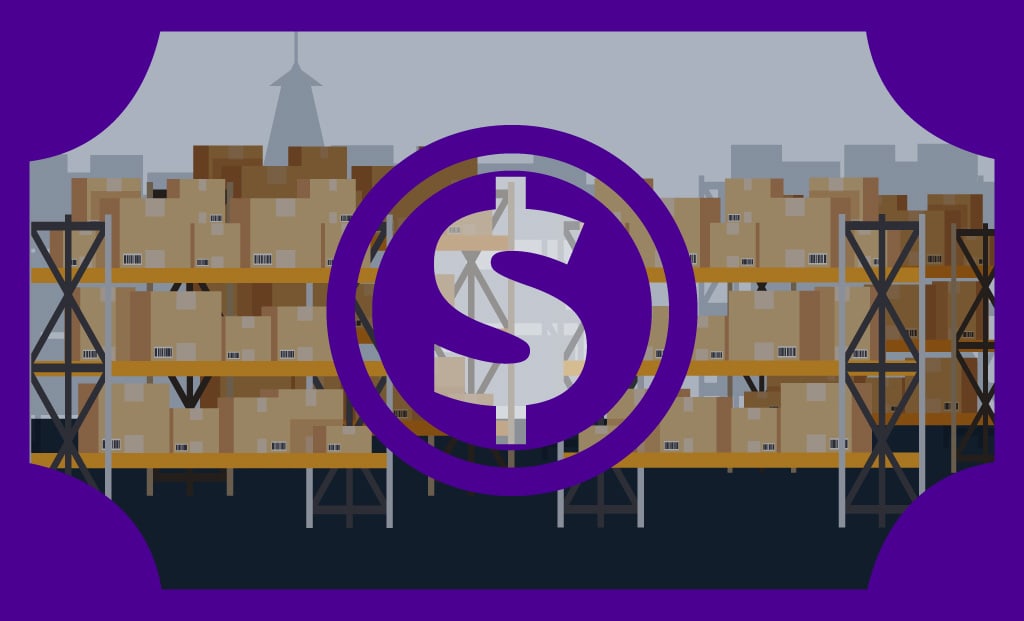
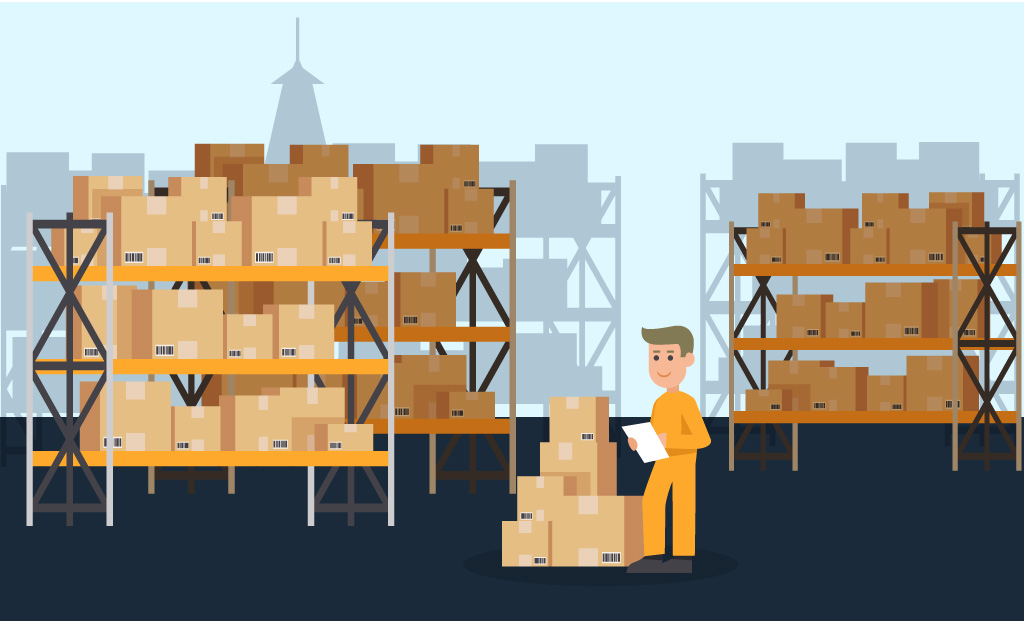
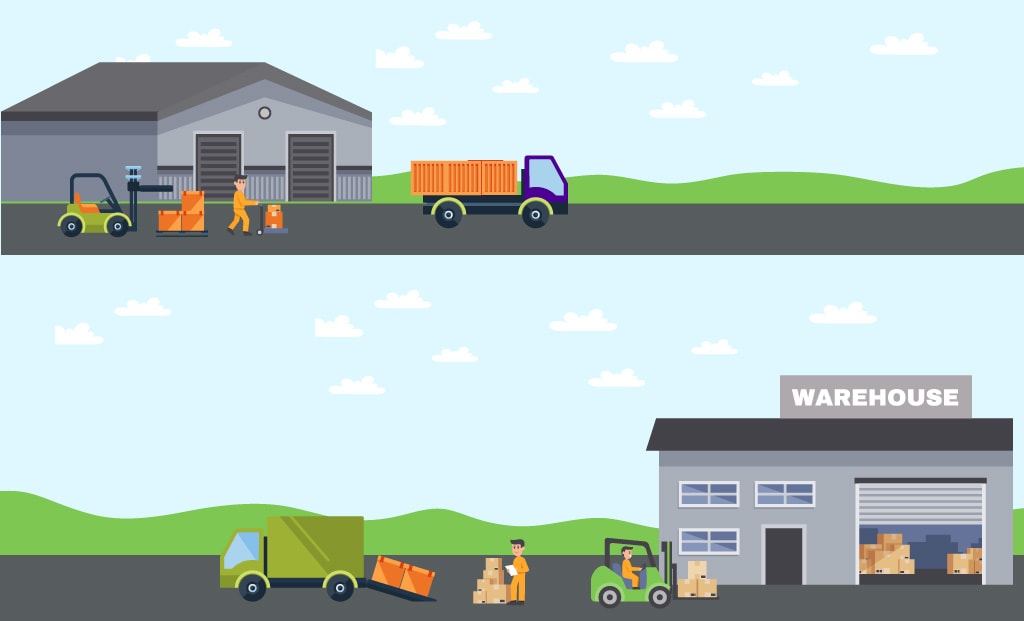
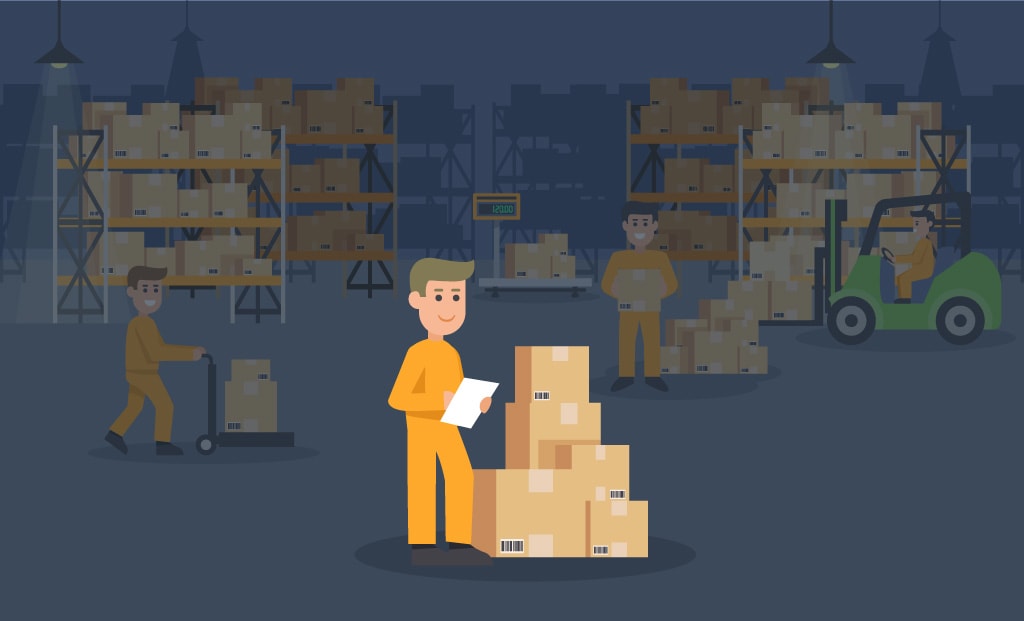
FAQ
Inventory Management in OmegaCube ERP enables manufacturing enterprises to efficiently plan, procure, build, manage and track inventory in real-time. They can maintain optimum inventory levels, improve material traceability and cash flows by ordering the right materials at the right time for the right cost from the right supplier.
Material Requirement Planning (MRP) in OmegaCube ERP helps manufacturers to accurately calculate the number of materials and components to manufacture a product. The calculation takes into account, the total number of orders in hand, existing inventory levels, and the delivery due date. Based on these parameters, material procurement is initiated from approved suppliers.
OmegaCube ERP can be easily integrated with a host of manufacturing applications such as Nesting, CAD, E-commerce, Shipping & Logistics, Barcode & RFID, Machine Monitoring, Email etc. Manufacturers can completely automate inventory, design, planning, and shipping & production workflows with the help of advanced integration capability.