Production Management
With OmegaCube ERP’s Production Management capabilities, you can automate workflows that drive operational efficiency, maximizes yield and improves resource utilization.
With integrated functionalities such as material requirement planning, production scheduling, product configuration, shop-floor, work order, quality and maintenance management etc. manufacturers can comprehensively manage shop-floor operations and track them in real-time.
Key Benefits
- Get real-time operational view at every production stage
- Access data from anywhere, anytime from any supported hand-held device
- Proactively respond to impending delays, machine breakdowns, quality issues to prevent disruptions and ensure on-time delivery
- Improve operator productivity by providing access to critical information at their fingertips
- Improve capacity utilization by providing the right information at the right time to the right people
Key Capabilities
Actions & Alerts
Eliminate manual communication methods and improve productivity by pushing key action items and operational alerts from OmegaCube ERP to personnel’s workcenters/devices in real-time.
Digital & Paperless Capabilities
Gage Calibration
Engineering Change Management
Equipment Maintenance
Minimize production disruptions by improving overall operating life of machines, parts, equipment and tools with OmegaCube ERP’s Equipment MRO capability.
Manufacturing Execution
Quality Management
Shop Floor Management
Tool & Fixture Management
Work Order Management
Workflow Automation
Material Requirement Planning (MRP)
Our Customers are Our Purpose and Our Strength

OmegaCube has gone to a painstaking amount of work to make sure that we can instantaneously navigate to all the data we need. That applies to the front office as well as the shop floor, which means we’re saving time, doing more work and cutting costs throughout the operation – without sacrificing quality or delivery.”

With OmegaCube ERP, we have expanded our production schedule by 7 times i.e., from one day to one week. Previously, the crew would know the scheduling only for the following day. However, with the ERP they know what to do for the entire week. They also have an approximate production schedule for the next 30 days but that keeps adjusting based on various factors.”

If I know how much capacity I have and I know my bookings I can decide on whether we can handle a particular order or if we need to buy another machine, subcontract the job or turn down the business. Before OmegaCube ERP, it was pretty much guesswork.”

OmegaCube has gone to a painstaking amount of work to make sure that we can instantaneously navigate to all the data we need. That applies to the front office as well as the shop floor, which means we’re saving time, doing more work and cutting costs throughout the operation – without sacrificing quality or delivery.”

With OmegaCube ERP, we have expanded our production schedule by 7 times i.e., from one day to one week. Previously, the crew would know the scheduling only for the following day. However, with the ERP they know what to do for the entire week. They also have an approximate production schedule for the next 30 days but that keeps adjusting based on various factors.”
Browse through our Latest ERP and Technological Insights
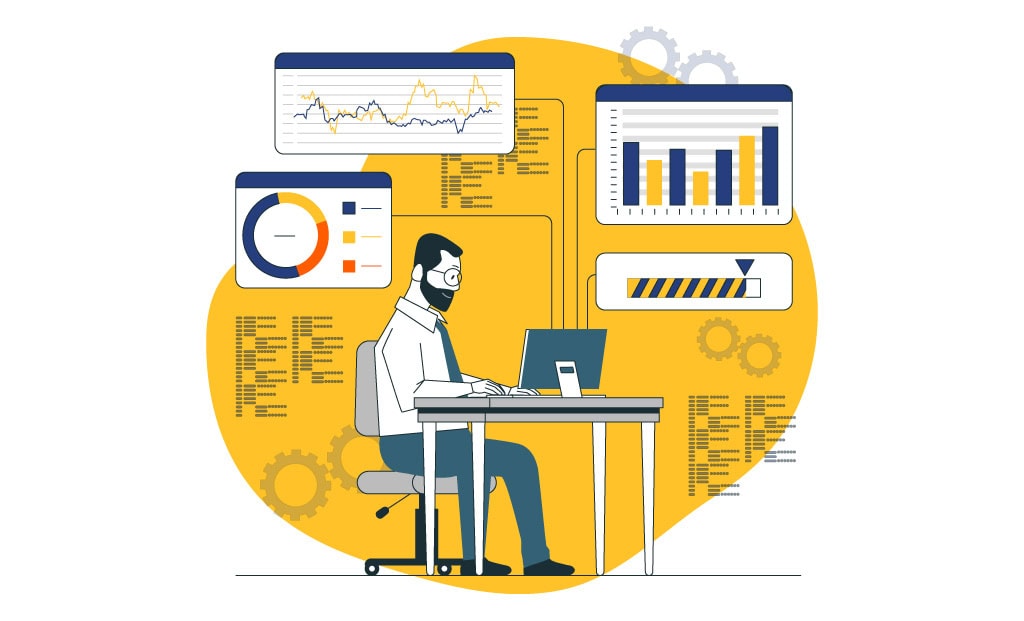
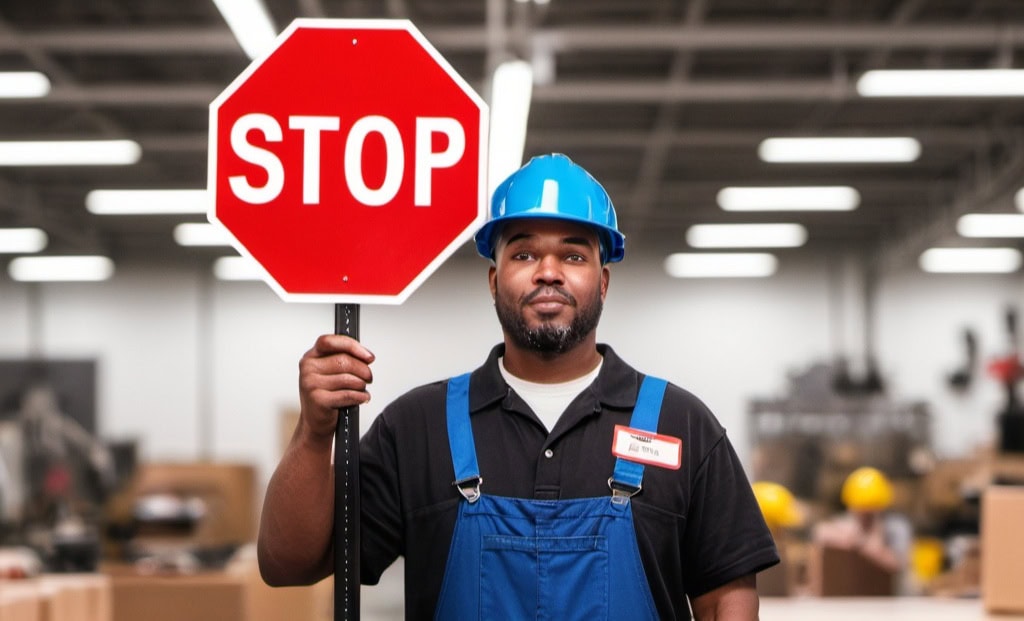
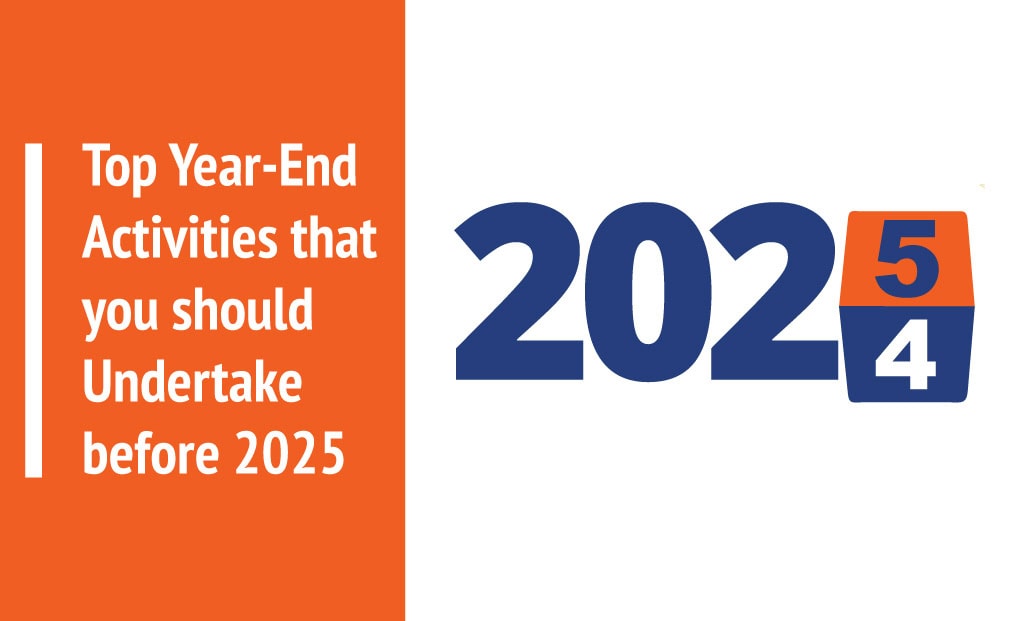
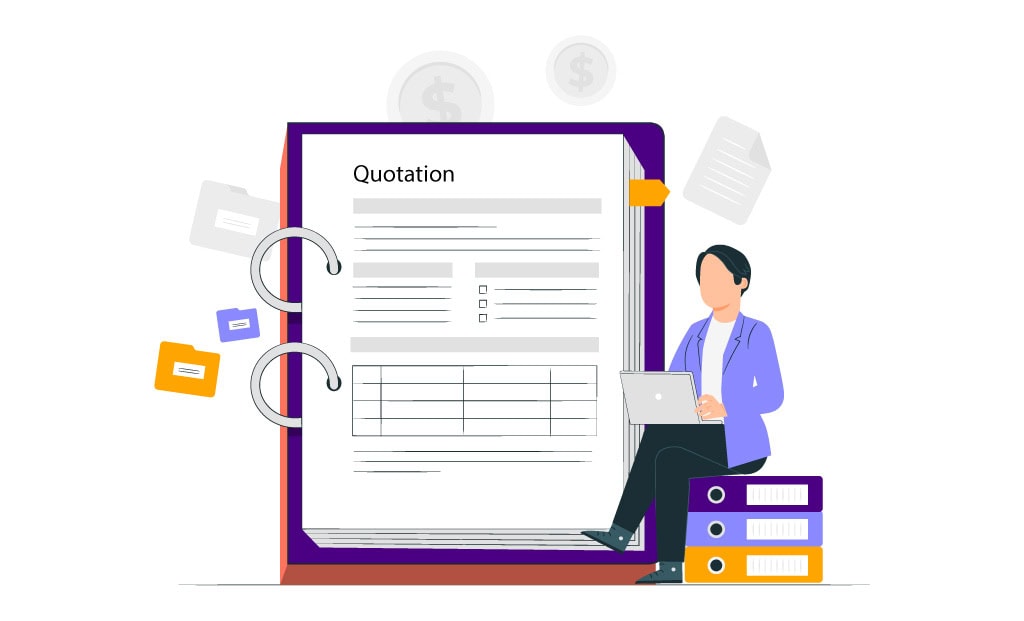
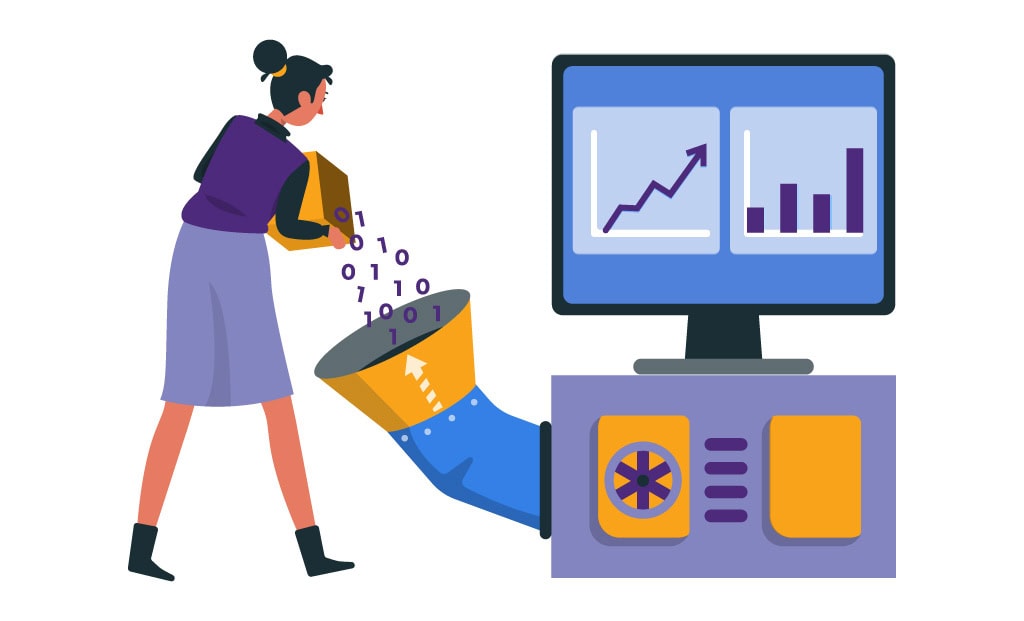
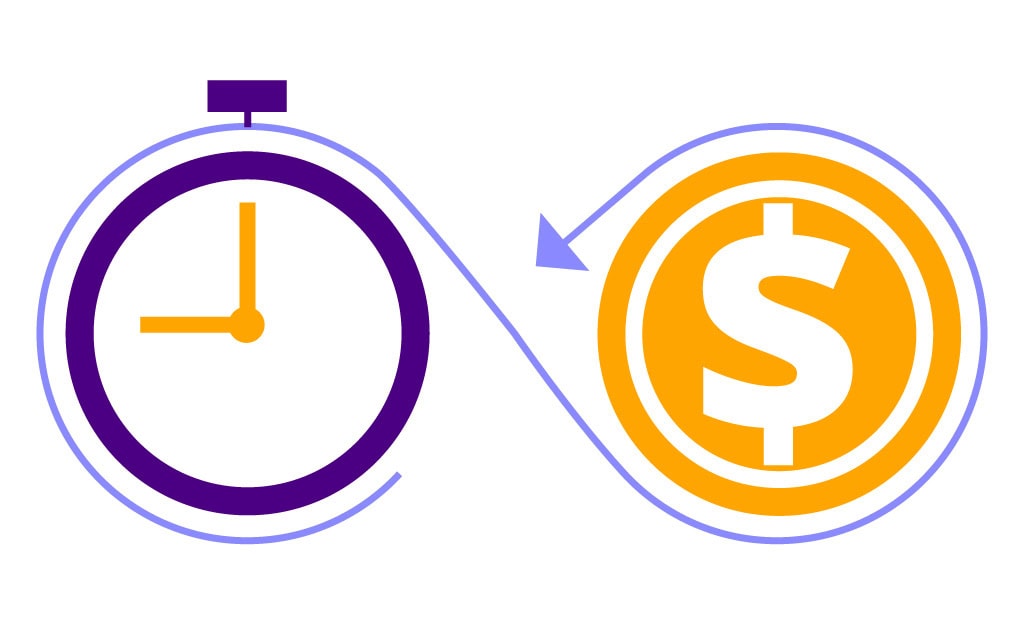
FAQ
Shop Floor Management in OmegaCube ERP helps manufacturers to get a real-time view of their shop floor operations, track & improve resource utilization, improve yield quality, meet compliance standards, reduce machine breakdown/idle time and improve overall efficiency.
Equipment Maintenance in OmegaCube ERP helps manufacturers to keep a steady track of maintenance planning and schedule of manufacturing equipment and machines. It helps them prevent maintenance-related breakdowns and potential production delays.