Engineering Change Management
With OmegaCube ERP’s Engineering Change Management, manufacturers can create and approve Engineering Change Notices (ECN) for any changes made to a component or item.
This helps manufacturers stay up-to-date with any changes in items, components, or materials throughout all stages of production, thanks to the comprehensive tracking and documentation capabilities of the system.
Key Benefits of Engineering Change Management
- Stay on top of engineering changes in your enterprise.
- Track engineering changes for tools, materials, items in real-time.
- Reduce overall impact of engineering changes on production.
- Robust engineering change documentation & versions.
- Reduce associated costs and production delay.
Key Features of Engineering Change Management
- Revision tracking for finished products, BOM items and routing changes.
- Ability to track revision numbers at every level of BOM.
- Full history of previous revisions.
- Recalculation of finished product cost based on change of BOM or routing.
- Track status of changes in operation and Work Centers upon changes approval.
- Where used search and analysis of revision change.
- Track disposition information for existing material stock.
- Information on the list of affected documents linked to the given item and revisions.
- Specify documents affected by the change with pre and post change revision details.
- Get summary of the changes with description, expected and completion date for ECN changes.
- Check status of ECN request, such as active, pass, fail, pending for review.
- Get detailed information about the reason for changes from existing revision.
Our Customers are Our Purpose and Our Strength

OmegaCube has gone to a painstaking amount of work to make sure that we can instantaneously navigate to all the data we need. That applies to the front office as well as the shop floor, which means we’re saving time, doing more work and cutting costs throughout the operation – without sacrificing quality or delivery.”

With OmegaCube ERP, we have expanded our production schedule by 7 times i.e., from one day to one week. Previously, the crew would know the scheduling only for the following day. However, with the ERP they know what to do for the entire week. They also have an approximate production schedule for the next 30 days but that keeps adjusting based on various factors.”

If I know how much capacity I have and I know my bookings I can decide on whether we can handle a particular order or if we need to buy another machine, subcontract the job or turn down the business. Before OmegaCube ERP, it was pretty much guesswork.”

OmegaCube has gone to a painstaking amount of work to make sure that we can instantaneously navigate to all the data we need. That applies to the front office as well as the shop floor, which means we’re saving time, doing more work and cutting costs throughout the operation – without sacrificing quality or delivery.”

With OmegaCube ERP, we have expanded our production schedule by 7 times i.e., from one day to one week. Previously, the crew would know the scheduling only for the following day. However, with the ERP they know what to do for the entire week. They also have an approximate production schedule for the next 30 days but that keeps adjusting based on various factors.”
Browse through our Latest ERP and Technological Insights
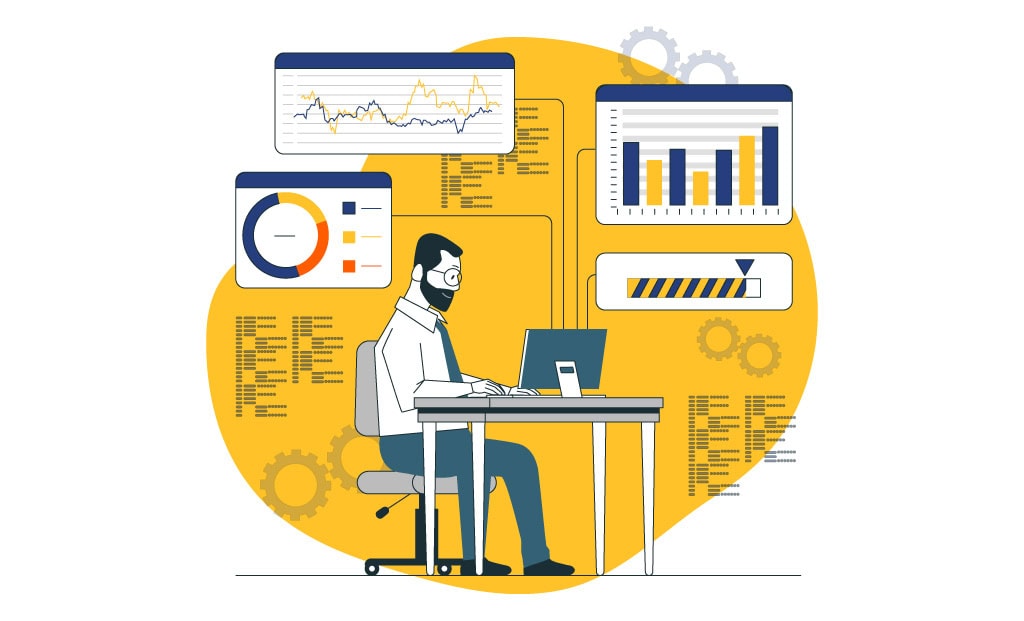
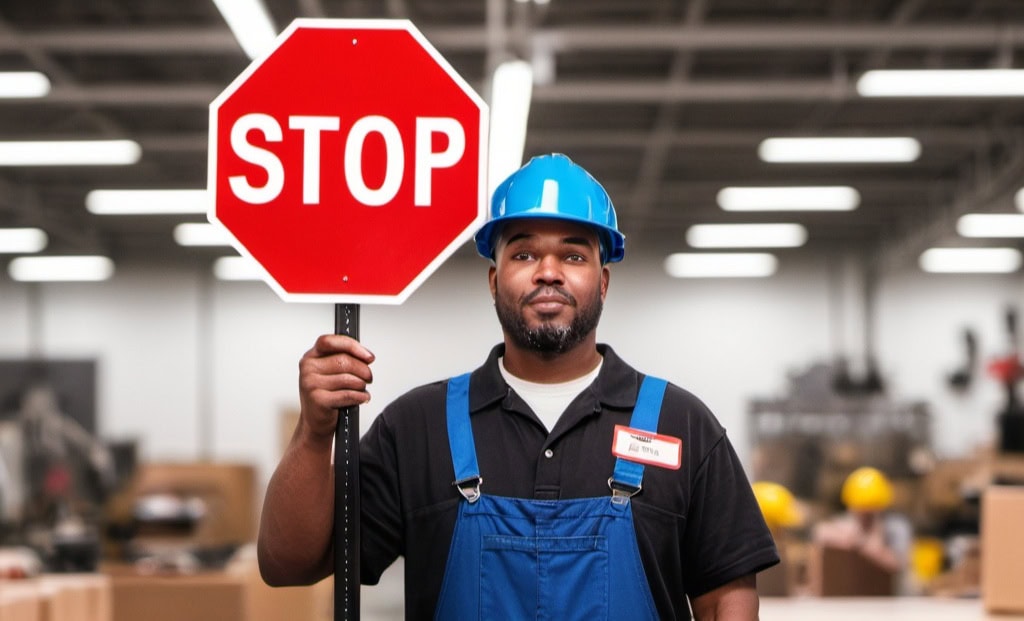
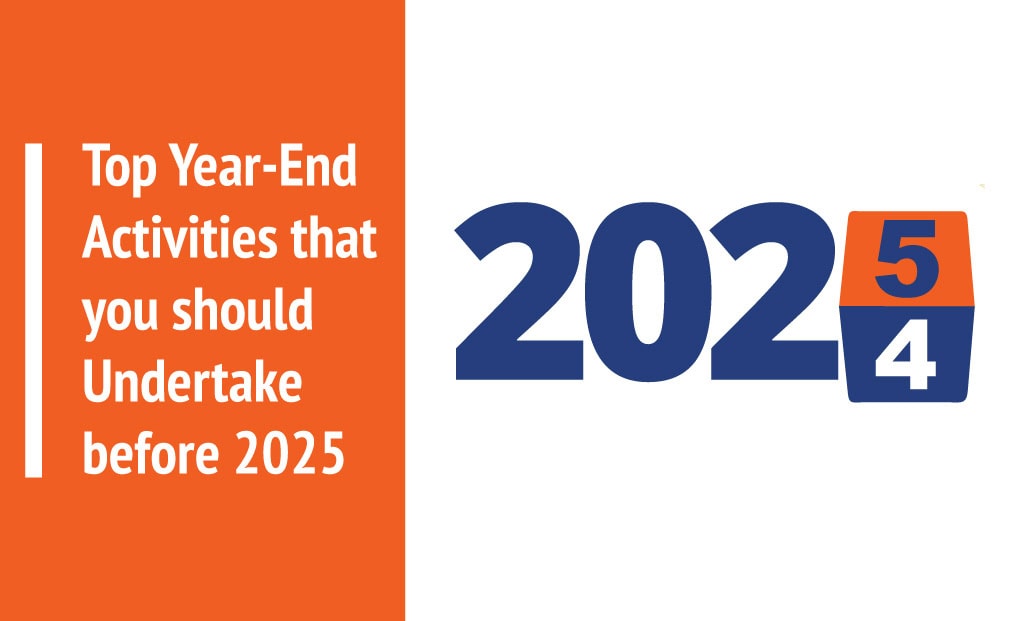
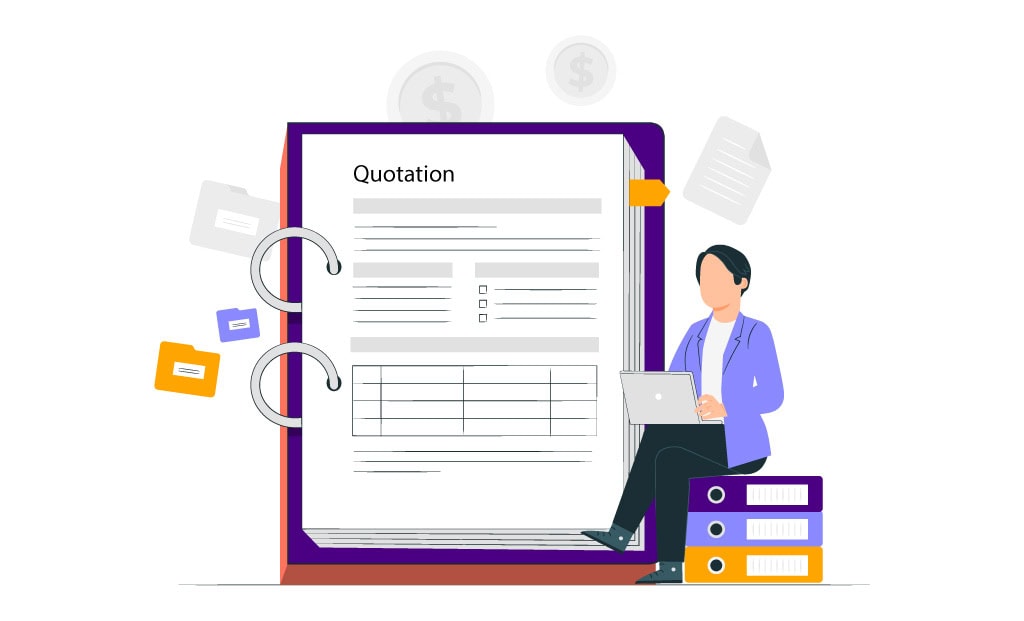
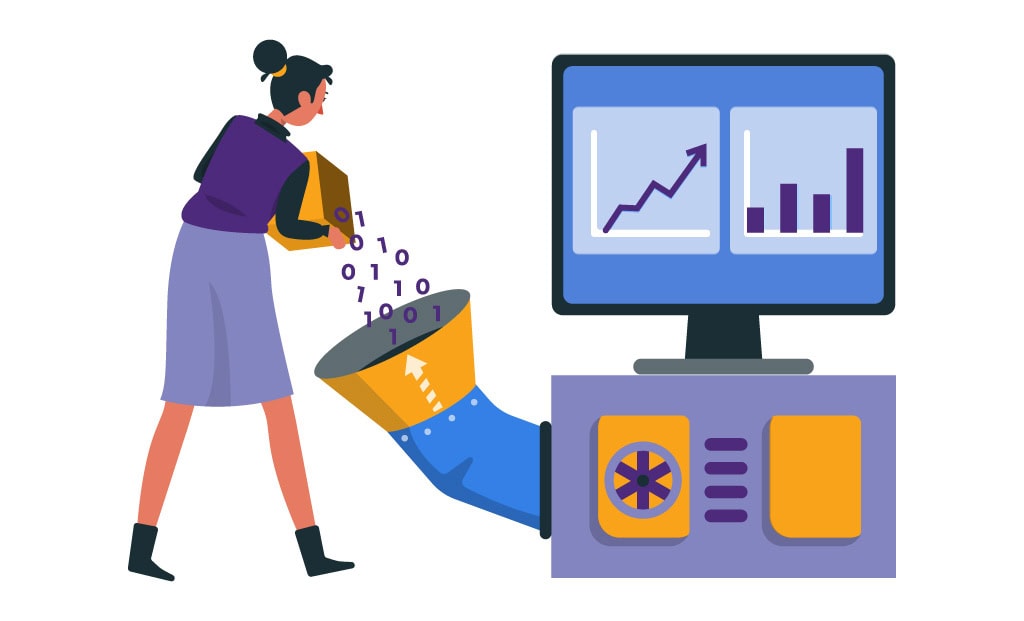
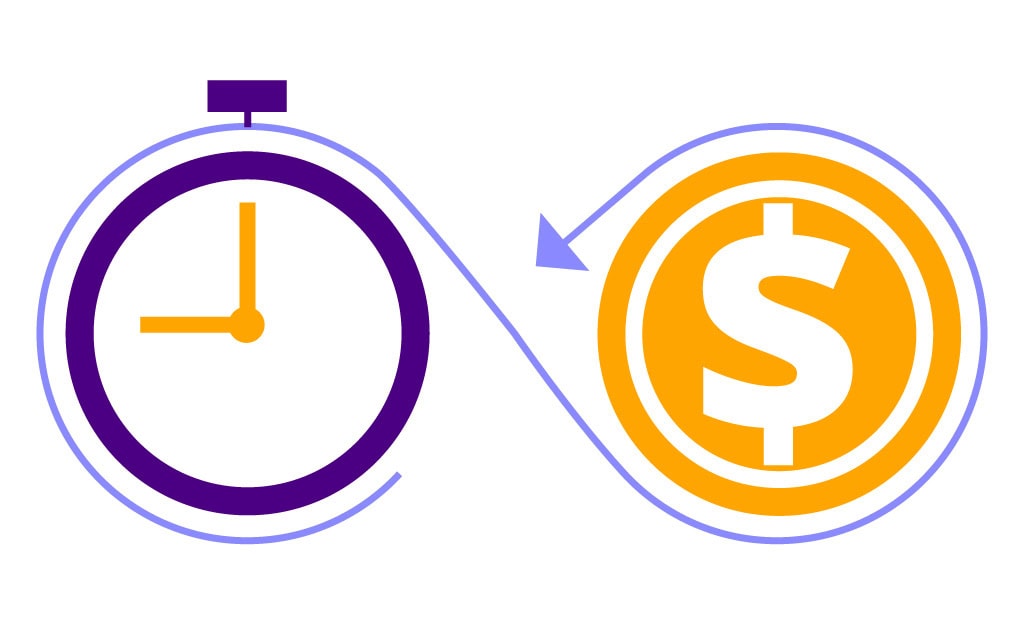
FAQ
Work Order Management in OmegaCube ERP helps manufacturers to accurately schedule work orders, prioritize based on customer requirement and dispatch them to the shop floor. They can track work order progress throughout the production process, combine work orders and increase overall manufacturing efficiency.
Planning and Scheduling in OmegaCube ERP automates production planning and scheduling workflows by taking material, manpower and machine availability into consideration. It improves capacity utilization during production, operator productivity, optimum supply chain planning, and on-time delivery to customers.
Shop Floor Management in OmegaCube ERP helps manufacturers to get real-time view of their shop floor operations, track & improve resource utilization, improve yield quality, meet compliance standards, reduce machine breakdown/idle time and improve overall efficiency.