- OmegaCube Technologies
- Product
- Enterprise Resource Planning
- Production Management
- Quality Management
Quality Management
Key Benefits of Quality Management
Key Features of Quality Management
- Centralized database to store all non-conformance data
- Integrated into RMA, Receiving, Shop floor transactions, and Inventory
- Disposition full or partial quantities
- Multiple dispositions allowed on each QA Hold
- Track defect codes, reasons, and other notes
- Attach pictures to inspection record
- Generate scrap, repair, and rework orders based on disposition
- Allow operators to put work in process or inventory on QA hold
- Generate alerts to QA personnel
- Automatically alert operators using dispatch list, when a part is on QA Hold
- Document corrective and preventive action using the 8D methodology
- Assign tasks to individuals and generate automatic emails and reminders
- Maintain a list of specifications for a part
- User-defined list of specifications a part should meet, their target values, and tolerances
- Enter inspections results at the operator terminal or import them from an external system
- Warn the operator for out of tolerance results
- Trigger QA hold for failed inspections
- Main gages in a centralized database
- Track Gage calibration information, procedures, and frequency of calibration
- Automatically trigger reminders to inspect and calibrate gages based on usage
- Issue and track gages to specific work orders
- Track history of what parts and gages were used
- Meet compliance requirements
- Gain powerful insights using quality dashboards
- Analyze quality metrics for suppliers, parts, manufacturing, operations
- Provide customers with customer metrics on quality
- Use analytical tools to drill down into details of quality metrics of parts, machines, employees
- Centralized database to store all non-conformance data
- Integrated into RMA, Receiving, Shop floor transactions, and Inventory
- Disposition full or partial quantities
- Multiple dispositions allowed on each QA Hold
- Track defect codes, reasons, and other notes
- Attach pictures to inspection record
- Generate scrap, repair, and rework orders based on disposition
- Allow operators to put work in process or inventory on QA hold
- Generate alerts to QA personnel
- Automatically alert operators using dispatch list, when a part is on QA Hold
- Document corrective and preventive action using the 8D methodology
- Assign tasks to individuals and generate automatic emails and reminders
- Maintain a list of specifications for a part
- User-defined list of specifications a part should meet, their target values, and tolerances
- Enter inspections results at the operator terminal or import them from an external system
- Warn the operator for out of tolerance results
- Trigger QA hold for failed inspections
- Main gages in a centralized database
- Track Gage calibration information, procedures, and frequency of calibration
- Automatically trigger reminders to inspect and calibrate gages based on usage
- Issue and track gages to specific work orders
- Track history of what parts and gages were used
- Meet compliance requirements
- Gain powerful insights using quality dashboards
- Analyze quality metrics for suppliers, parts, manufacturing, operations
- Provide customers with customer metrics on quality
- Use analytical tools to drill down into details of quality metrics of parts, machines, employees
Our Customers are Our Purpose and Our Strength

Our customers have highlighted the reduction in quality issues ever since we adopted OmegaCube ERP into our system because we are not mixing up materials or revisions. OmegaCube ERP ensures that old BOM versions are inactive and we are using the most up-to-date version of the Bill of Materials.”

Those checks-and-balances just within the quality department ensure better product and delivery for our customers. When you multiply that process discipline across the organization the results are fantastic. And when you give customers a quality product, delivered when they want it, at a competitive cost you sell more.”

OmegaCube has gone to a painstaking amount of work to make sure that we can instantaneously navigate to all the data we need. That applies to the front office as well as the shop floor, which means we’re saving time, doing more work and cutting costs throughout the operation – without sacrificing quality or delivery.”
Browse through our Latest ERP and Technological Insights
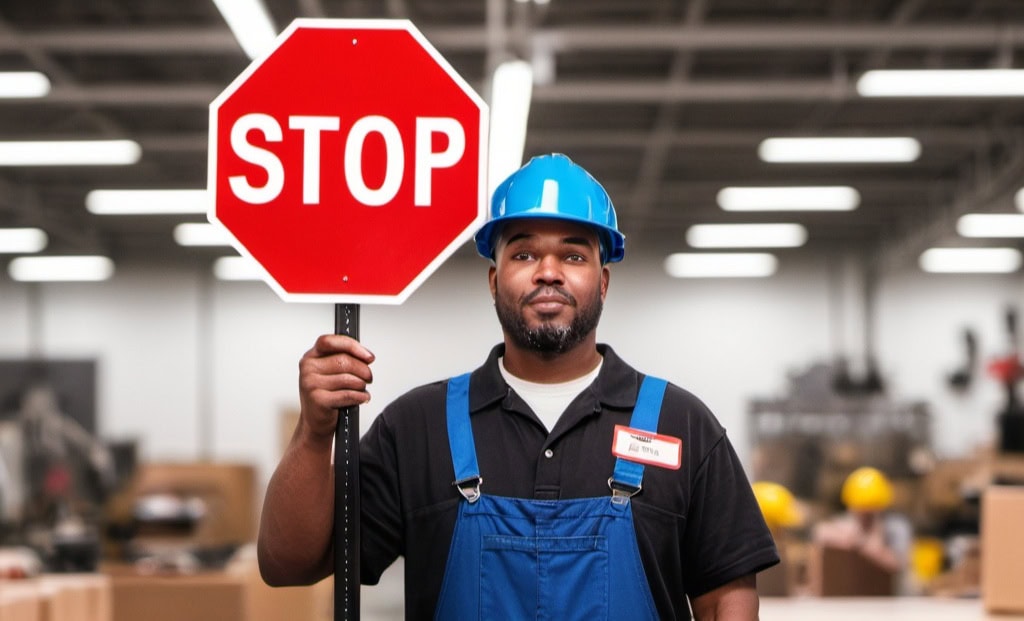
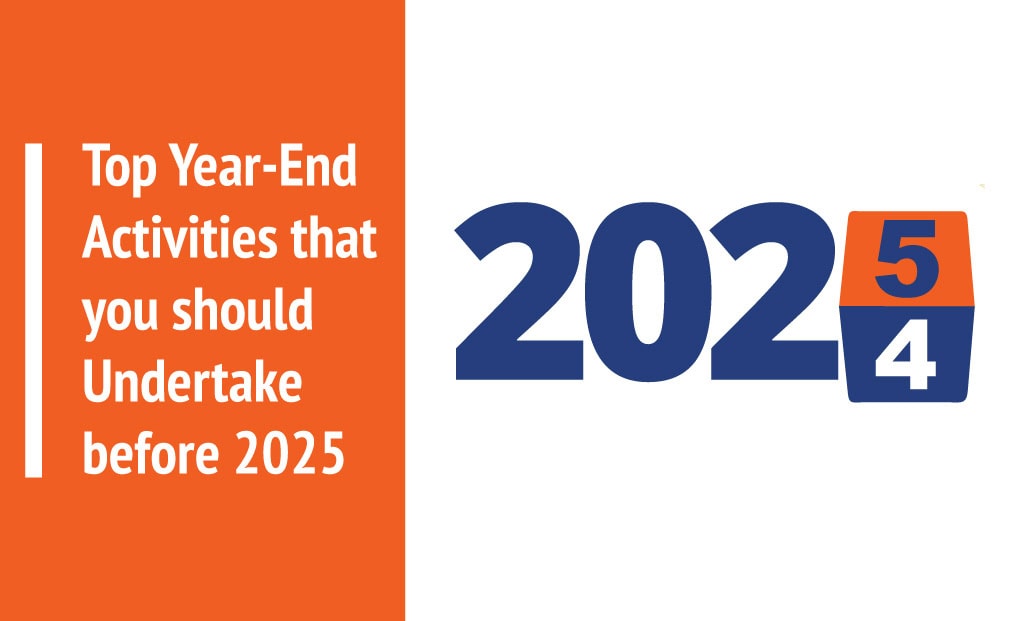
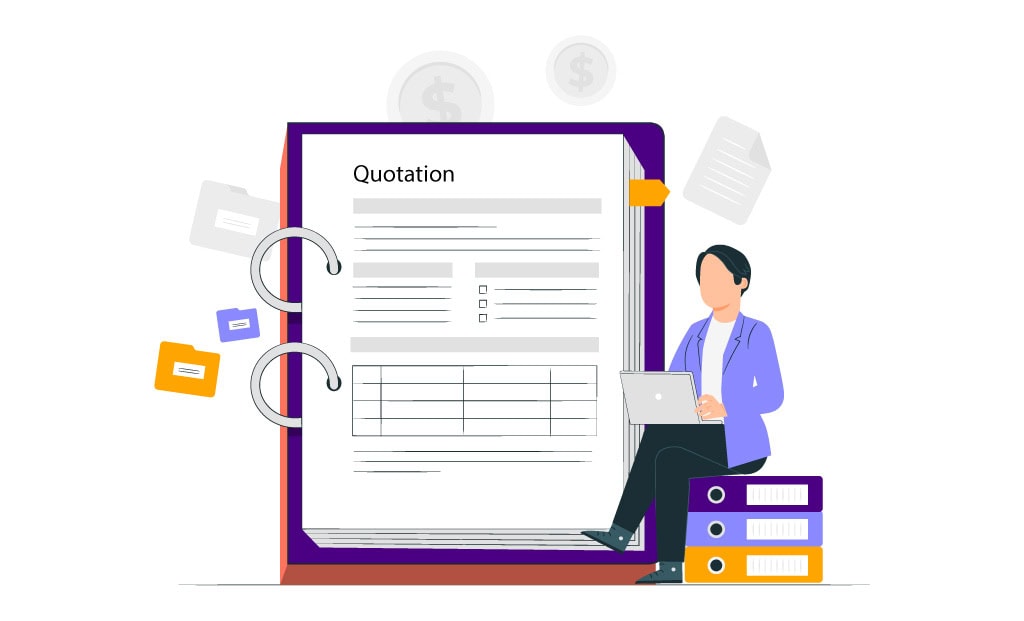
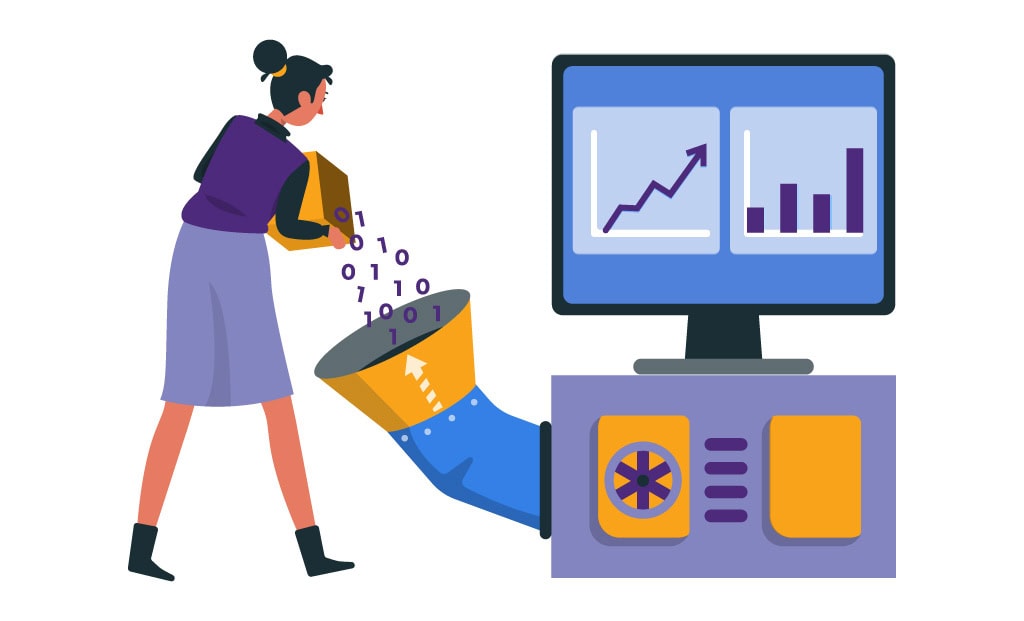
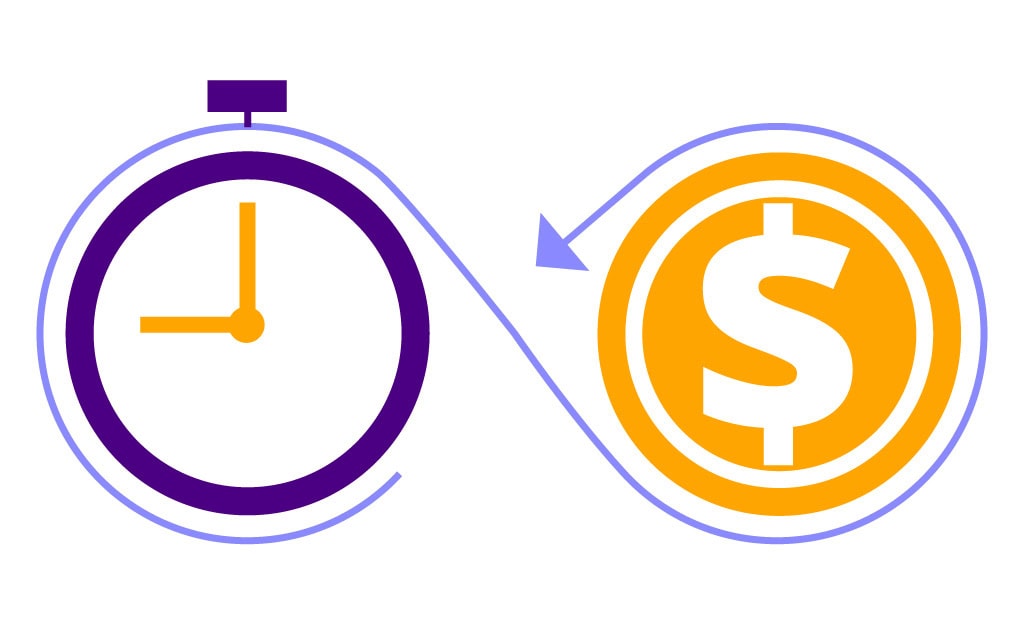
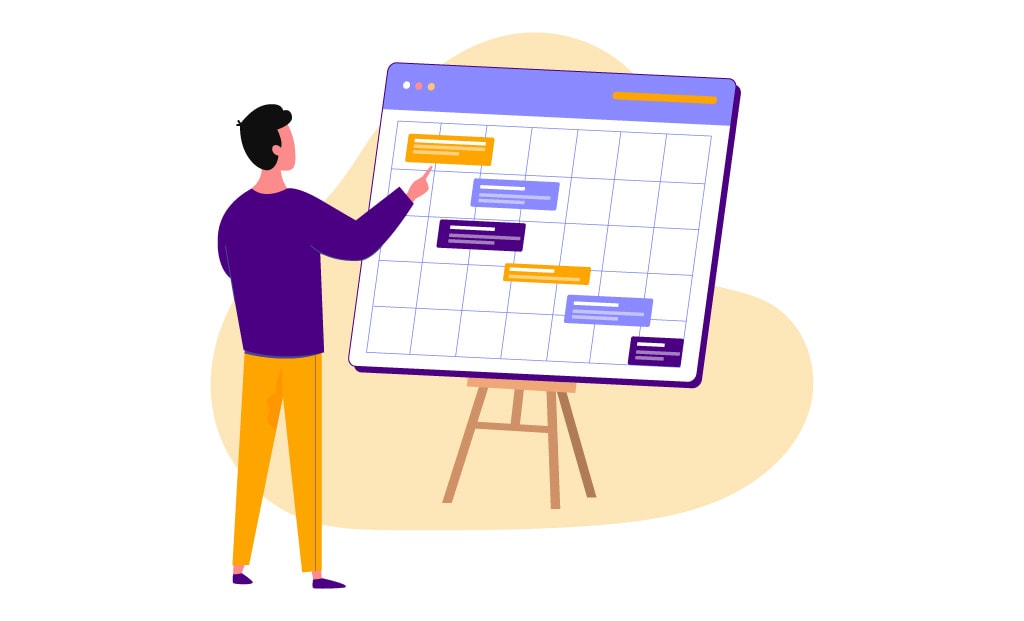
FAQ
Suppliers and Purchasing in OmegaCube ERP helps manufacturers to efficiently track and manage the entire flow of raw materials right from its suppliers to the warehouse, to the factory till the final product reaches the customer. It helps improve supplier relationships via continuous goods monitoring, quality control, data-sharing via EDI, and self-service portals for suppliers.
Planning and Scheduling in OmegaCube ERP automates production planning and scheduling workflows by taking material, manpower and machine availability into consideration. It improves capacity utilization during production, operator productivity, optimum supply chain planning, and on-time delivery to customers.
Inventory Management in OmegaCube ERP enables manufacturing enterprises to efficiently plan, procure, build, manage and track inventory in real time. They can maintain optimum inventory levels, improve material traceability and cash flows by ordering the right materials at the right time for the right cost from the right supplier.