- OmegaCube Technologies
- Solutions
- By ERP Software Users
- OmegaCube ERP for Supply Chain Managers
Supply Chain Managers and Personnel have a greater challenge of keeping track of shipments that arrive at the manufacturing facility till they leave the facility/warehouse as a finished product. They also have to ensure that time-to-recall is quick and accurate so that defects can be contained quickly, recall costs are less, supplier’s quality is consistent and customer satisfaction remains unaffected.
OmegaCube’s Supply Chain Management solution ensures comprehensive real time visibility over your supply chain operations and performance enabling you to take quick informed decisions.
OmegaCube ERP for Supply Chain Managers
- Digitally collaborate with suppliers and procure materials in the right quantity, at the right time for the right price.
- Ensure procurement of quality materials from seasoned suppliers to improve quality compliance.
- Integrate with third party applications and systems to automate supply chain workflows & improve efficiency.
- Reduce procurement costs and inventory overstocking by timing your purchases based on various factors.
- Quickly trace materials to its exact source within the entire supply chain and improve customer satisfaction.
- Decrease supply chain costs pertaining to inventory overstocking, expedited shipments, warehouse storage & labor.
- Improve supplier performance and long-term collaboration by providing self-service capabilities.
Our Customers are Our Purpose and Our Strength

We have to coordinate truckloads of steel, castings and other components from foreign suppliers, and PowerERP helps us balance, plan and schedule our ordering and inventory movements.”

Well, I can just say that it’s impossible to make a mistake now. The close-knit process within OmegaCube ERP ensures that almost no mistake can be committed. For example, a purchase order lines up with a purchase receipt, and you can’t enter an invoice without a purchase receipt. In the ERP, you cannot duplicate the purchase receipt because it’s tagged to this purchase order. Therefore, the system makes it entirely difficult to make any sort of mistakes of course, unknowingly.”

This was March 2020 and then COVID-19 hit. If we were still using the old FoxPro system and the manual way of operating, I don’t think we could have had everybody go home and work remotely.
With OmegaCube ERP, we were able to work remotely and still operate during the pandemic. Even though we just completed setting up our initial ERP system, our employees were able to run with it while working remotely and that ended up working out great. The system operated efficiently for sales, engineering, and purchasing.
I don’t think we could have done that with the old FoxPro system as we did with OmegaCube ERP. So the timing of implementing OmegaCube ERP was perfect.
Browse through our Latest ERP and Technological Insights
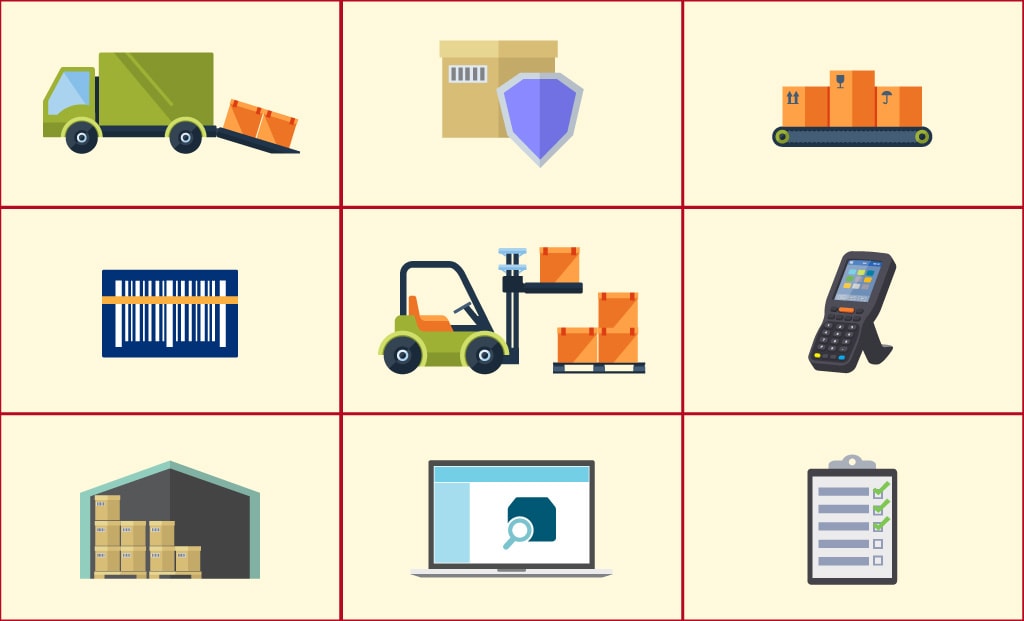
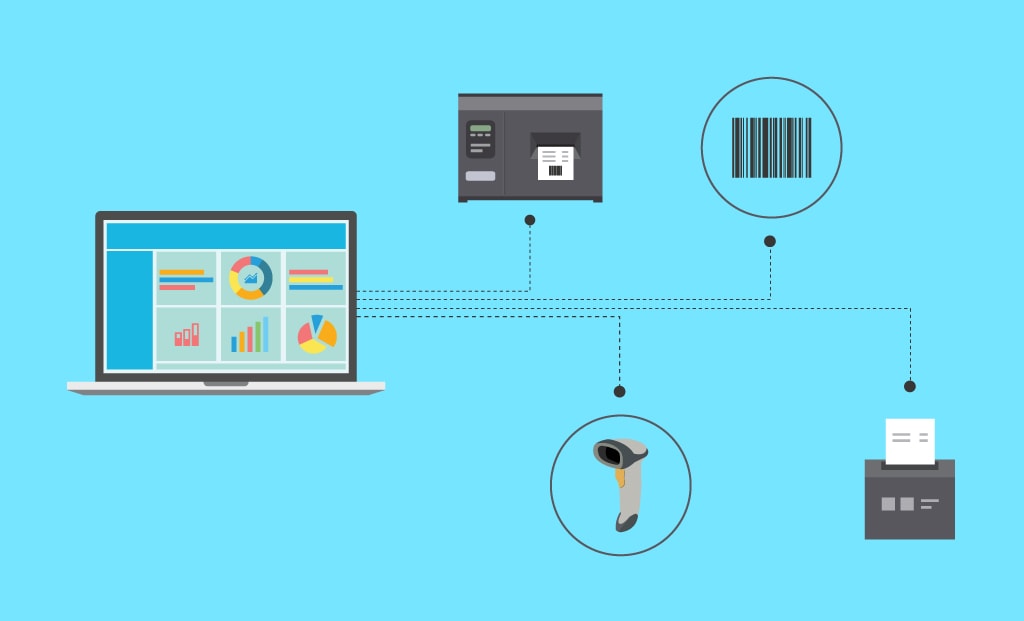
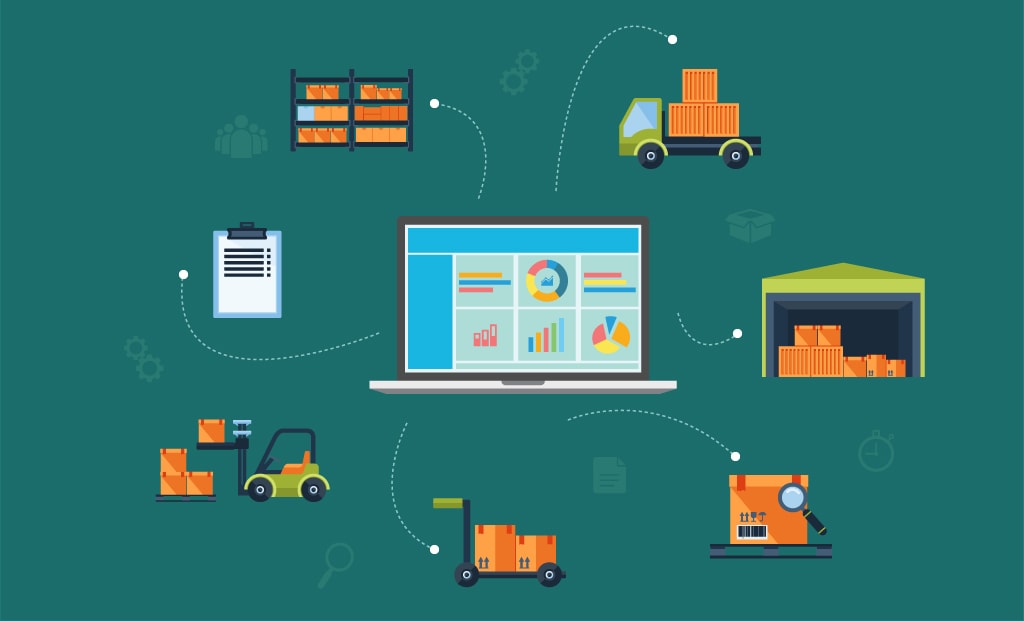
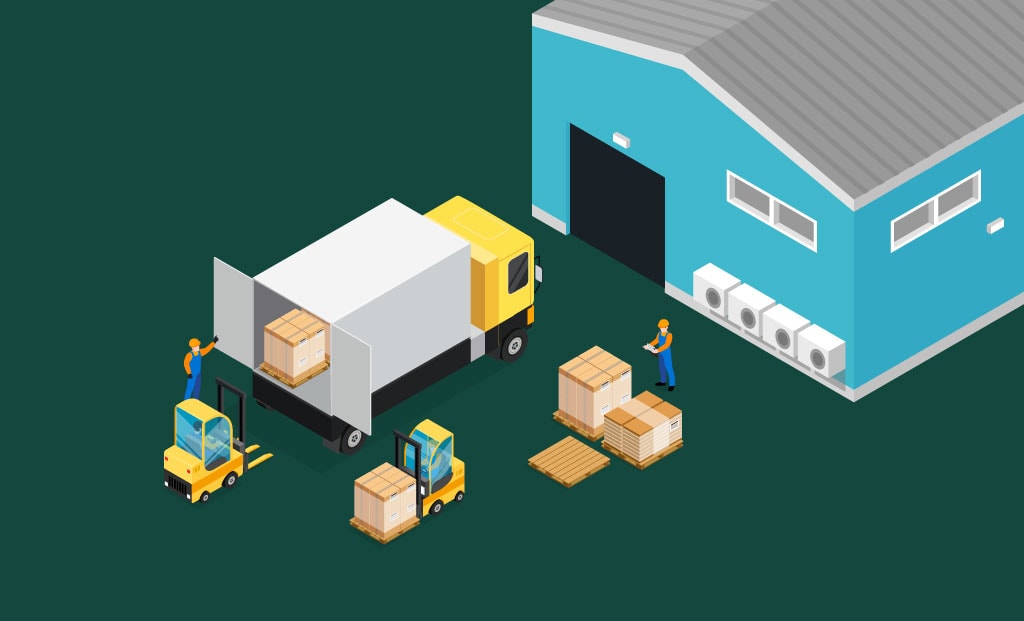
