- OmegaCube Technologies
- Solutions
- By Industry
- Fabricated Metals
Fabricated Metals
Key Benefits to Metal Fabricators
- Build detailed quotation and cost estimates to reduce time-to-quote and time-to-estimate leading to faster conversions.
- Integration with nesting software and design software (AutoCAD, SolidWorks) leading to increase in material utilization, machine up-time, and capability to incorporate frequent changes in customer requirements.
- Anticipate material requirements and trigger auto purchase through effective Material Requirement Planning (MRP) & Scheduling.
- Enhance customer satisfaction & market reputation by tracking products/parts all the way to the supplier using bar-code and labeling.
- Maintain optimum inventory levels, reduce storage costs, and decrease re-order times with efficient Inventory Management & Control.
Top Functional Areas in OmegaCube ERP for Metal Fabricators
- Get realtime visibility into inventory levels & movement for quick order fulfillment.
- Auto-update of inventory levels owing to integration with sales & purchase management, order management, and accounting systems.
- Auto reorder of raw materials, and components in case of shortage detected by the inventory monitoring system.
- Enter quotes for customers or prospects with expiration control and multiple revisions.
- Build detailed estimates that include operation costs, material costs, outside services, etc.
- Part and routing calculators with a multi-level Bill of Materials.
- Trigger supplier RFQ and use the RFQ results in estimates.
- Automatically create opportunities in CRM and track follow-up, callbacks, etc. in CRM.
- Import nesting information from ProNest, SigmaNest, etc.
- Report layout completions & drops.
- Capture completions, part weight, labor, and drop information from the machine controller through an XML interface.
- Link work orders and automatically adjust work order due dates based on sales order due dates.
- Utilize electronic dispatch to provide job schedule, drawings, work instructions and other documents to machine operators.
- Automatically re-sequence schedule based on change in job priority.
- View day and period-wise dispatch lists for each employee that includes job details, operation schedule times etc.
- Pull up relevant material and heat-treating certificates during shipping automatically.
- Track non-conformance through a centralized database integrated with RMA, Shop Floor transactions & Inventory.
- Quality tracking with 1st piece inspections, rejects, and SCARs.
- Analyze quality metrics for suppliers, parts, manufacturing, and operations using quality management dashboards.
- Schedule key EDI processes such as Accounting, Inventory control, Revision Control etc.
- Synchronize operations between internal departments, with your vendors & customers.
- Manage simultaneous operations that can possibly cause conflicts.
- Have complete view of in-process jobs on the shop floor along with their status.
- Integrated scheduling to determine start/stop times for all assembly and sub-job operations.
- Have visibility of shop-floor performance including efficiency ratios via manufacturing metrics.
- Record time and job information quickly and accurately.
- Manage your distributor or end-user data and communications in CRM.
- Provide self-service reordering of repeat items using portals.
- Manage and maintain multiple warehouses and track inventory movements between them.
- Select the right pickup patterns, take faster routes, and track shipments.
- Keep a tab on each container and ensure your customers have received their orders intact and on time.
- Get realtime visibility into inventory levels & movement for quick order fulfillment.
- Auto-update of inventory levels owing to integration with sales & purchase management, order management, and accounting systems.
- Auto reorder of raw materials, and components in case of shortage detected by the inventory monitoring system.
- Enter quotes for customers or prospects with expiration control and multiple revisions.
- Build detailed estimates that include operation costs, material costs, outside services, etc.
- Part and routing calculators with a multi-level Bill of Materials.
- Trigger supplier RFQ and use the RFQ results in estimates.
- Automatically create opportunities in CRM and track follow-up, callbacks, etc. in CRM.
- Import nesting information from ProNest, SigmaNest, etc.
- Report layout completions & drops.
- Capture completions, part weight, labor, and drop information from the machine controller through an XML interface.
- Link work orders and automatically adjust work order due dates based on sales order due dates.
- Utilize electronic dispatch to provide job schedule, drawings, work instructions and other documents to machine operators.
- Automatically re-sequence schedule based on change in job priority.
- View day and period-wise dispatch lists for each employee that includes job details, operation schedule times etc.
- Pull up relevant material and heat-treating certificates during shipping automatically.
- Track non-conformance through a centralized database integrated with RMA, Shop Floor transactions & Inventory.
- Quality tracking with 1st piece inspections, rejects, and SCARs.
- Analyze quality metrics for suppliers, parts, manufacturing, and operations using quality management dashboards.
- Schedule key EDI processes such as Accounting, Inventory control, Revision Control etc.
- Synchronize operations between internal departments, with your vendors & customers.
- Manage simultaneous operations that can possibly cause conflicts.
- Have complete view of in-process jobs on the shop floor along with their status.
- Integrated scheduling to determine start/stop times for all assembly and sub-job operations.
- Have visibility of shop-floor performance including efficiency ratios via manufacturing metrics.
- Record time and job information quickly and accurately.
- Manage your distributor or end-user data and communications in CRM.
- Provide self-service reordering of repeat items using portals.
- Manage and maintain multiple warehouses and track inventory movements between them.
- Select the right pickup patterns, take faster routes, and track shipments.
- Keep a tab on each container and ensure your customers have received their orders intact and on time.
Enterprise solution for every industry
Our Customers are Our Purpose and Our Strength

People expect that an ERP system will allow them to run their business exactly how they want to, but more often than not, the ERP system is the glove and you’re the hand that has to squeeze into it.
Not so with OmegaCube. They helped us meet our vision rather than requiring us to formulate our processes around their solution.

There were competitors who weren’t as flexible as OmegaCube. OmegaCube assured us that they can do whatever we want them to do and they can adjust to fit our organization and not the other way around. They provided us insights into what they did for other customers and we saw what work they have done for them. This was, eventually, the final selling point for us.”

This was March 2020 and then COVID-19 hit. If we were still using the old FoxPro system and the manual way of operating, I don’t think we could have had everybody go home and work remotely.
With OmegaCube ERP, we were able to work remotely and still operate during the pandemic. Even though we just completed setting up our initial ERP system, our employees were able to run with it while working remotely and that ended up working out great. The system operated efficiently for sales, engineering, and purchasing.
I don’t think we could have done that with the old FoxPro system as we did with OmegaCube ERP. So the timing of implementing OmegaCube ERP was perfect.
Browse through our Latest ERP and Technological Insights
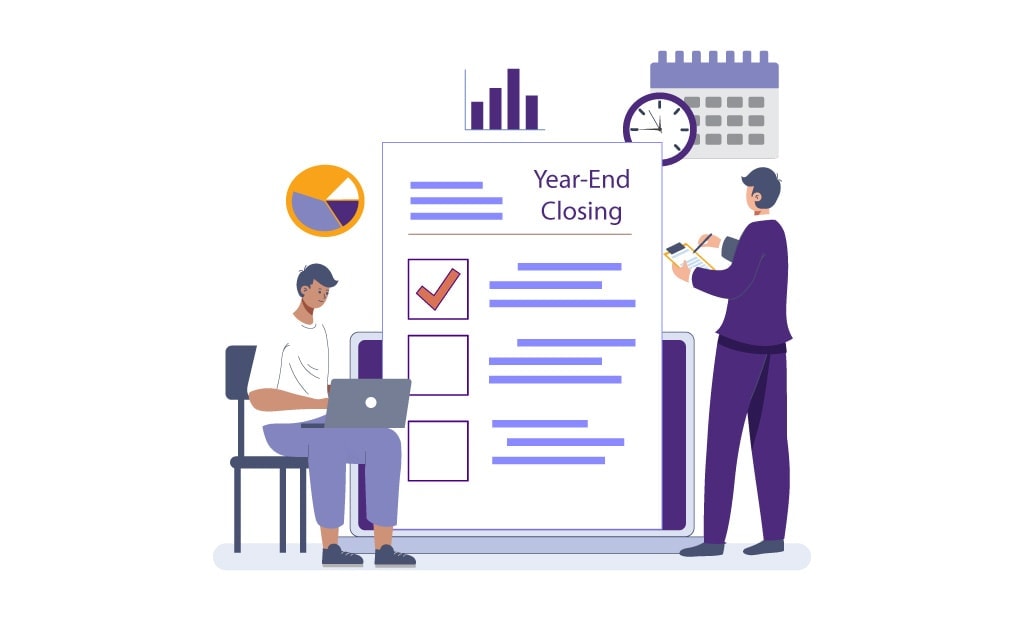
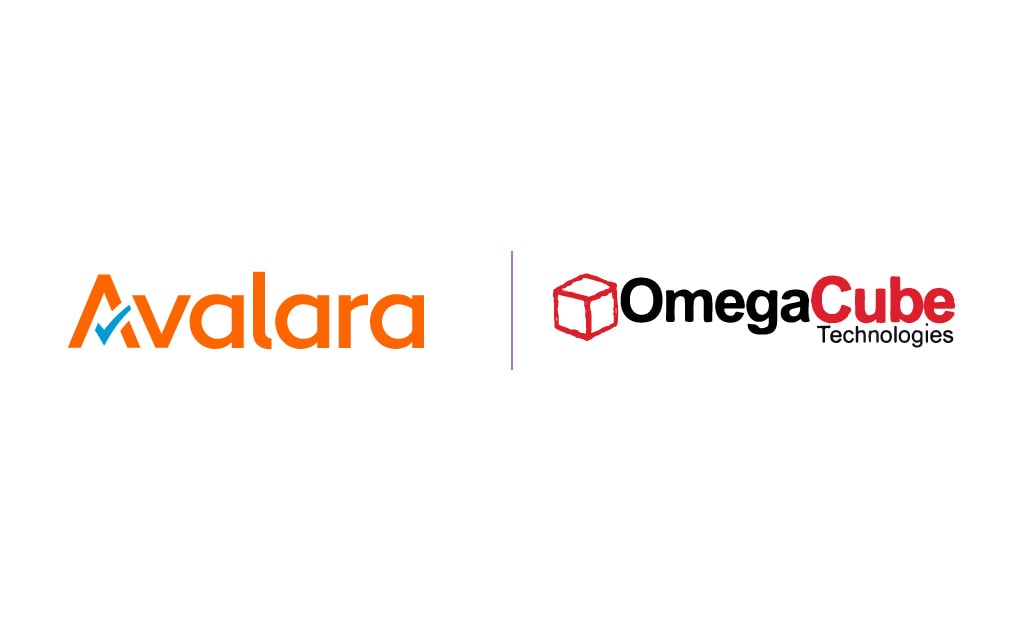
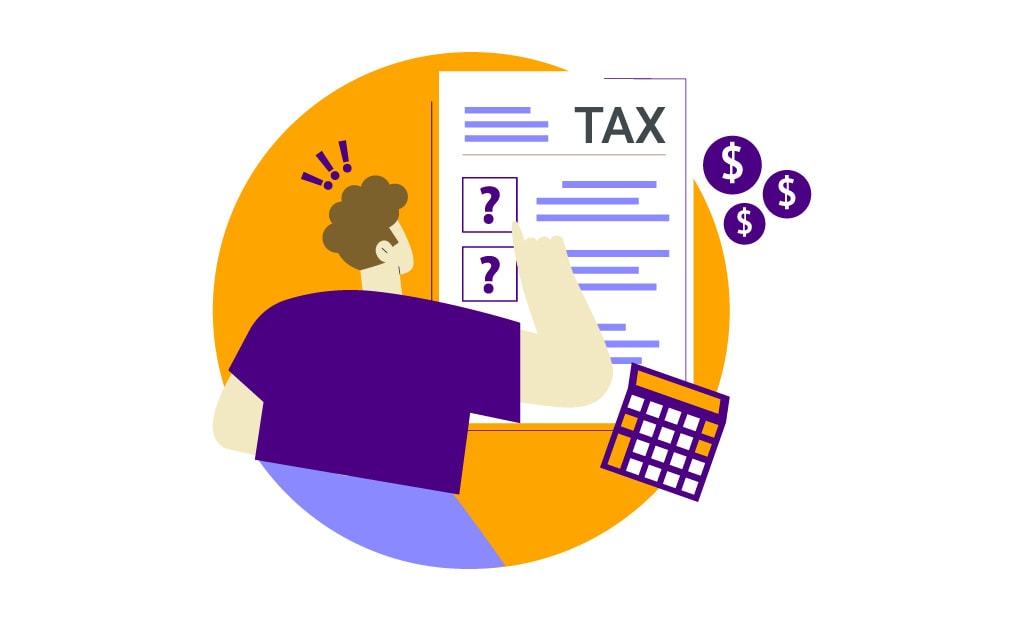
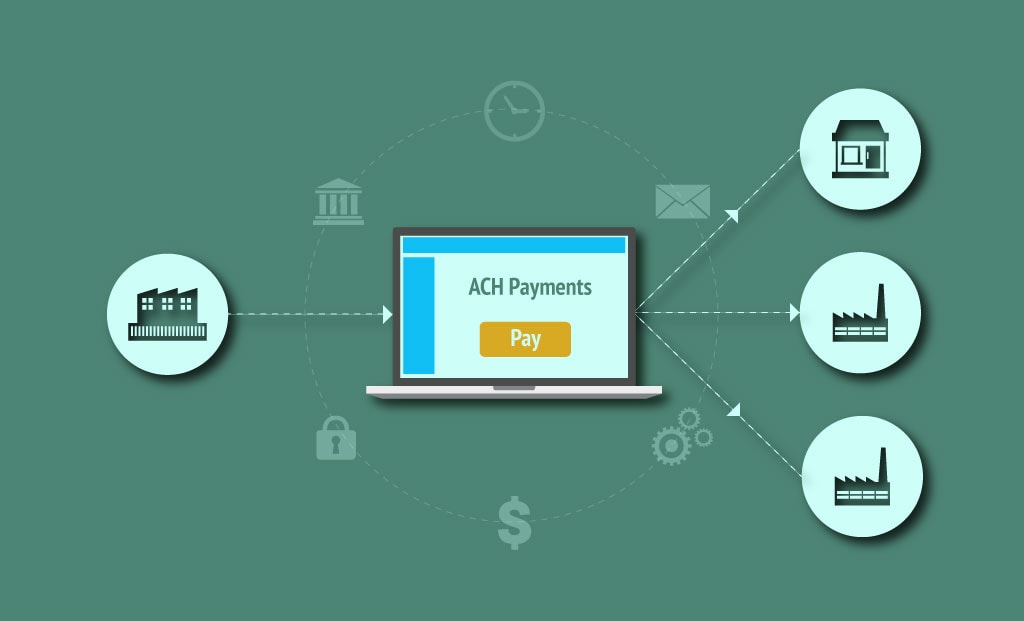
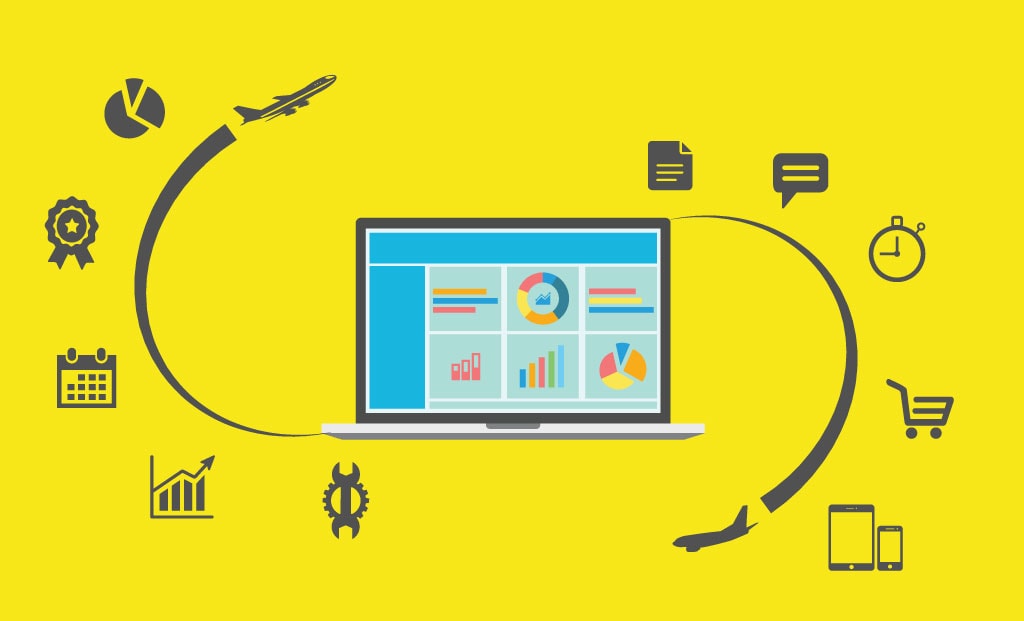
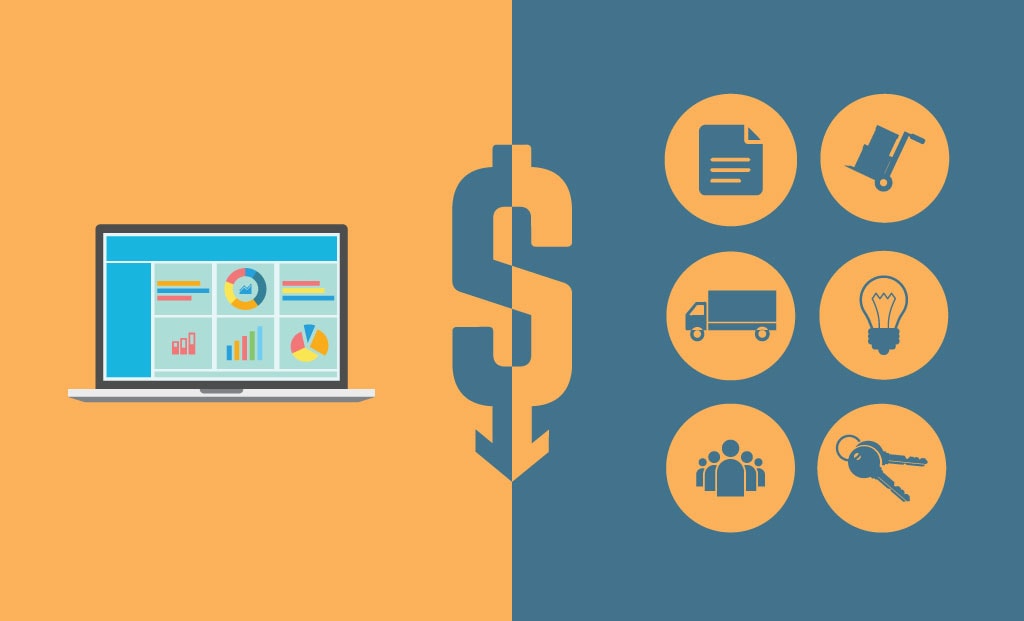